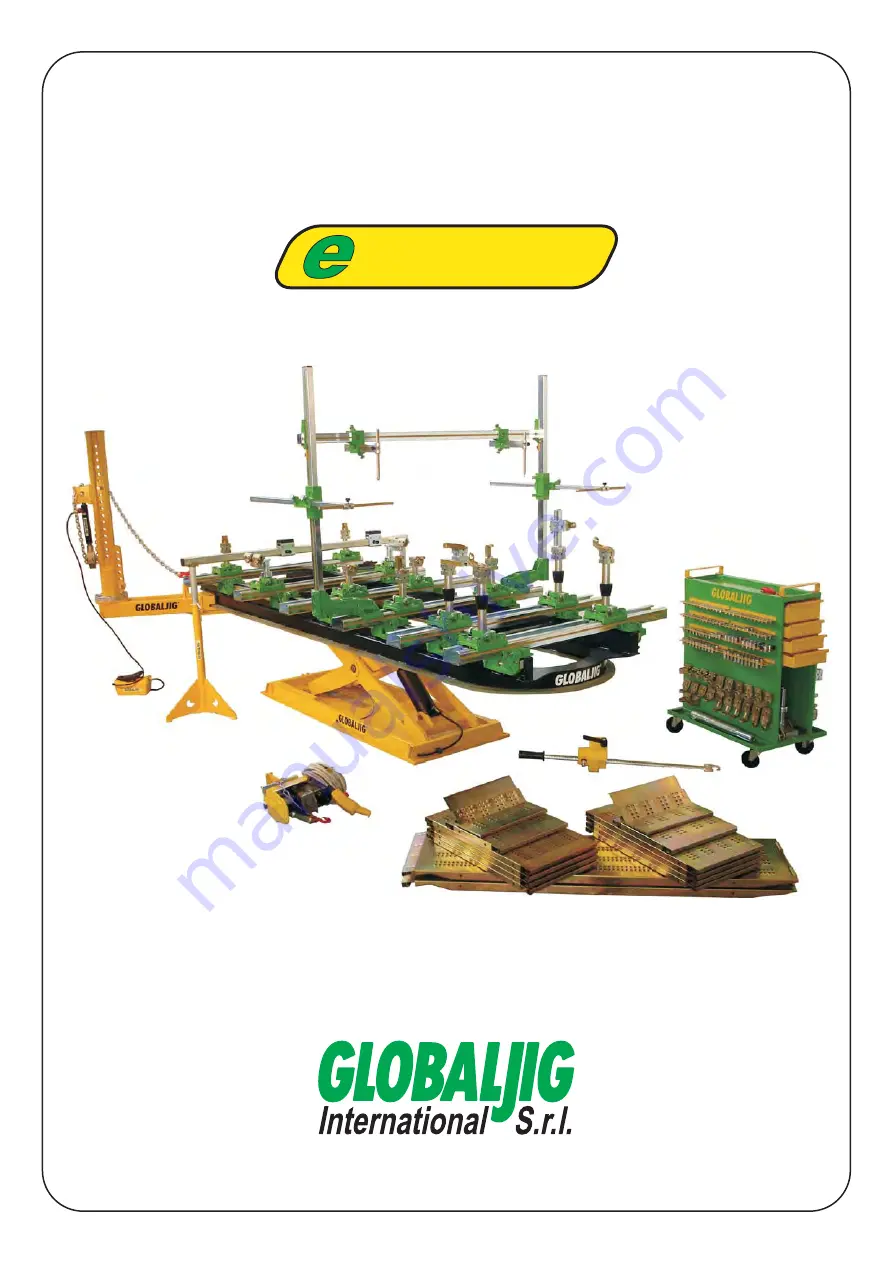
USER’S MANUAL
volution
Via Aurelia Ovest, Km. 383 - 54100 Massa (MS) - ITALY - Tel.: +39 0585 8364 - Fax: +39 0585 833880 - www.globaljig.it
Società unipersonale sotto la direzione e controllo della Bellini Srl. -
Iscritta al Reg. Imprese di Massa Carrara al N° 01064230459
Capitale sociale € 100.000,00 i.v.
Summary of Contents for Evolution
Page 2: ...volution USER S MANUAL Year of Manufacture ...
Page 12: ...10 ...
Page 13: ...11 ...
Page 14: ...12 ...
Page 15: ...13 ...
Page 23: ...21 ...
Page 24: ...22 ...
Page 36: ...34 10 1 Attachment 01 Lift bench dimensions ...
Page 37: ...35 10 2 Attachment 02 Lift bench work area ...
Page 39: ...37 10 4 Attachment 04 Electronic data ...
Page 40: ...38 10 5 Attachment 05 Hydraulic system diagram ...
Page 43: ...41 10 8 Attachment 08 Figures ...
Page 46: ...44 ...