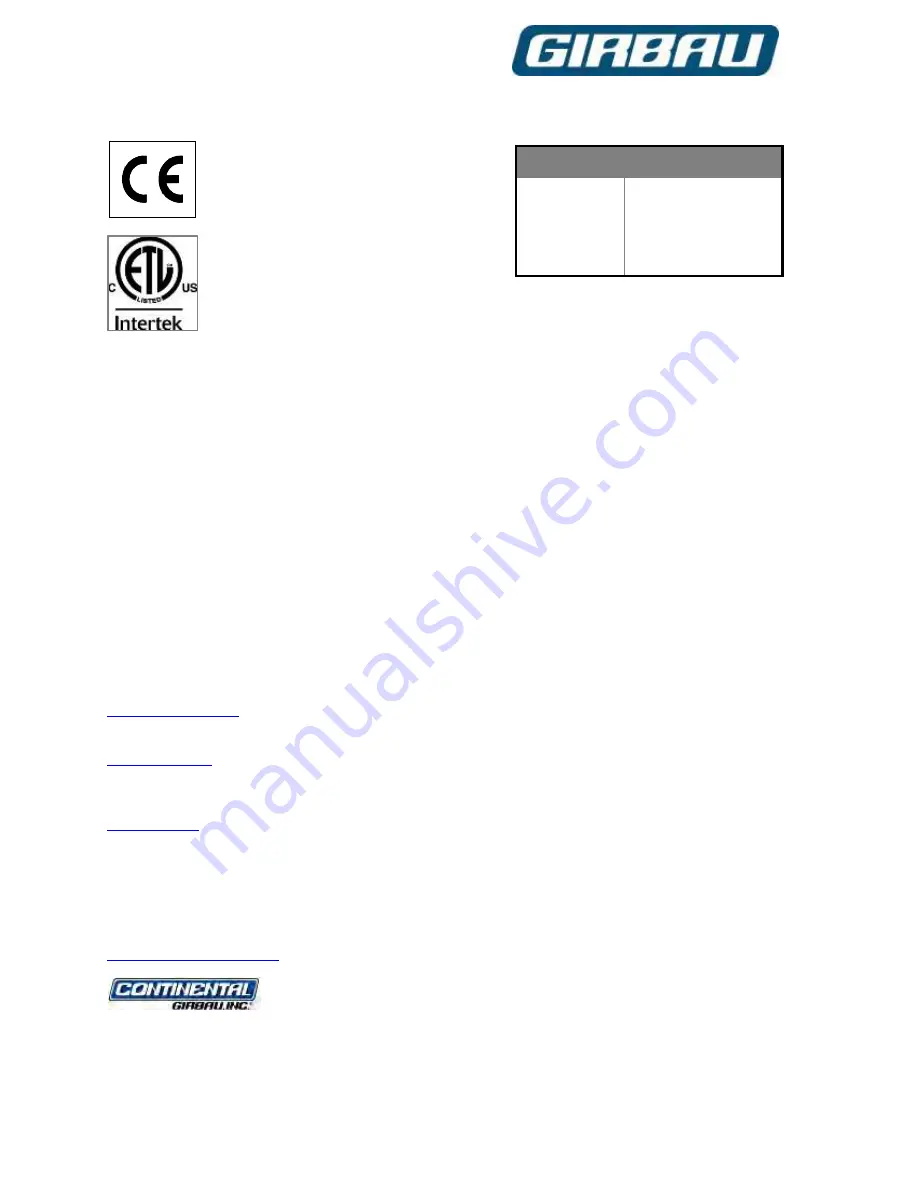
Code No. 549758
Rev. nº 10/0418
Model
From Machine No.
ED260
ED340
ED460
ED660
ED900
ED1250
2,215,001
2,240,001
2,265,001
2,290,001
2,480,001
2,470,001
Installation Instruction Manual for
ED
dryers
GIRBAU, SA
Crta de Manlleu, km. 1
08500 VIC (Barcelona) • SPAIN
National sales:
T.(+ 34) 902 300 359
International sales:
T.(+ 34) 938 862 219
Service:
T.(+ 34) 902 300 357
www.girbau.es
For
USA and CANADA:
CONTINENTAL GIRBAU Inc.
2500 State Road 44
WI 54904 Oshkosh • USA
Tel. 1(920) 231-8222
www.continentalgirbau.com
EN
Installation
ED260/ED340
ED460/ED660
ED900/ED1250