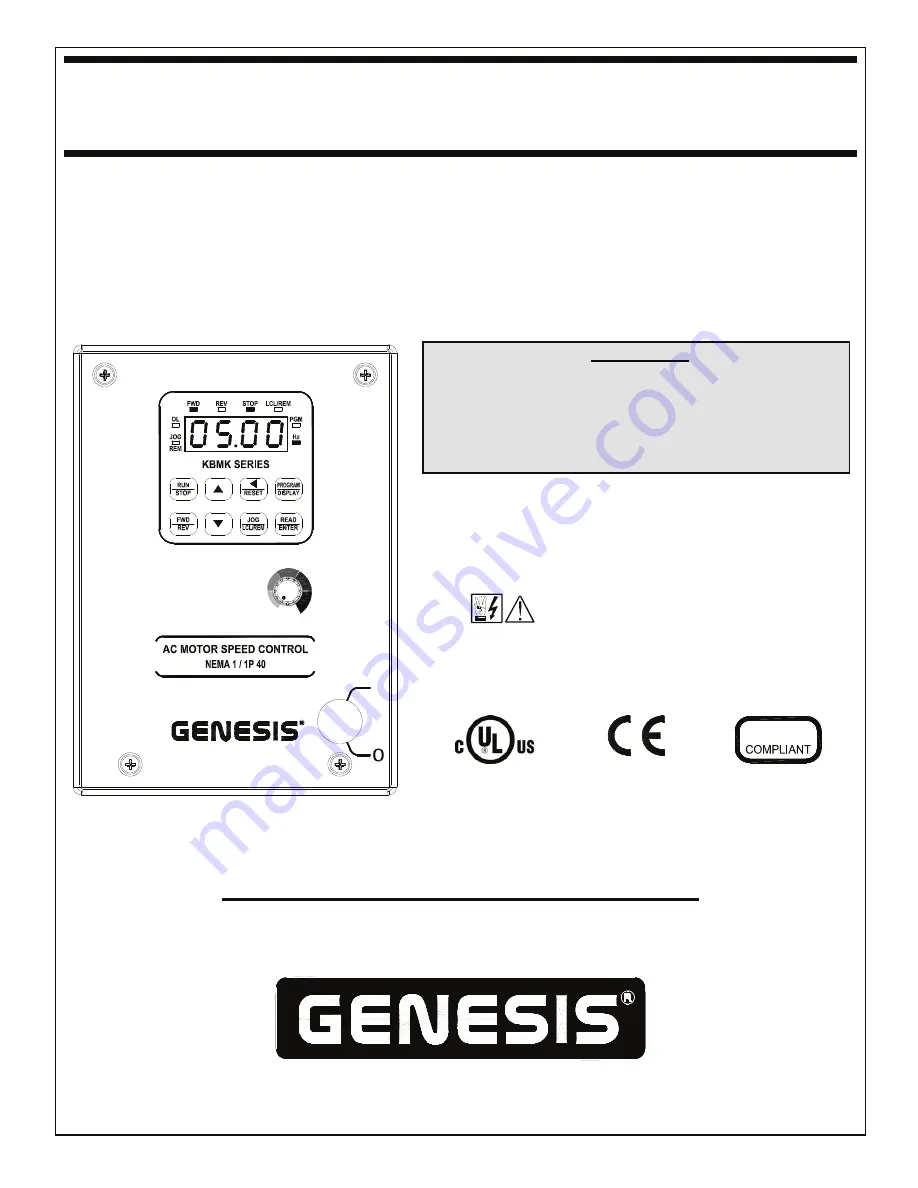
INSTALLATION AND OPERATION MANUAL
KBMK SERIES
Adjustable Frequency Drives
for 1/8 HP thru 1 HP 3-Phase AC Motors Rated 208 – 230 VAC, 50/60 Hz
NEMA-1 / IP-40
Operate from 115* and 208/230 Volt 50/60 Hz AC Line
Variable Speed / Soft-Start with Electronic Motor Overload Protection
1
*IMPORTANT
This drive is factory set for:
1. 60 Hz Motors.
For 50 Hz motors, see Figure 12, on page 16.
2. 208/230 Volt AC Line Input.
For 115 Volt AC line input, see Section 7, on page 14.
See Safety Warning, on page 5.
I
LISTED
IND. CONT.
EQ. – 70ZA
2
RoHS
This Manual Covers Models KBMK-24D and KBMK-24DF
2
The information contained in this manual is intended to be accurate. However, the
manufacturer retains the right to make changes in design which may not be included herein.
Notes:
1.
UL approved as an electronic overload protector for motors.
2.
Model KBMK-24DF contains a built-in
AC line Class A RFI (EMI) filter which meets CE Council Directive 89/336/EEC Industrial Requirement. For Class
B Residential Requirement, install the KBRF-300 RFI (EMI) Filter (Part No. 9484).
Automation and Control
COPYRIGHT © 2008 KB Electronics, Inc.
(see back cover)
Summary of Contents for KBMK Series
Page 9: ...9 FIGURE 3 COVER LAYOUT I FIGURE 4 DRIVE LAYOUT...
Page 50: ...50 NOTES...
Page 51: ...51 NOTES...