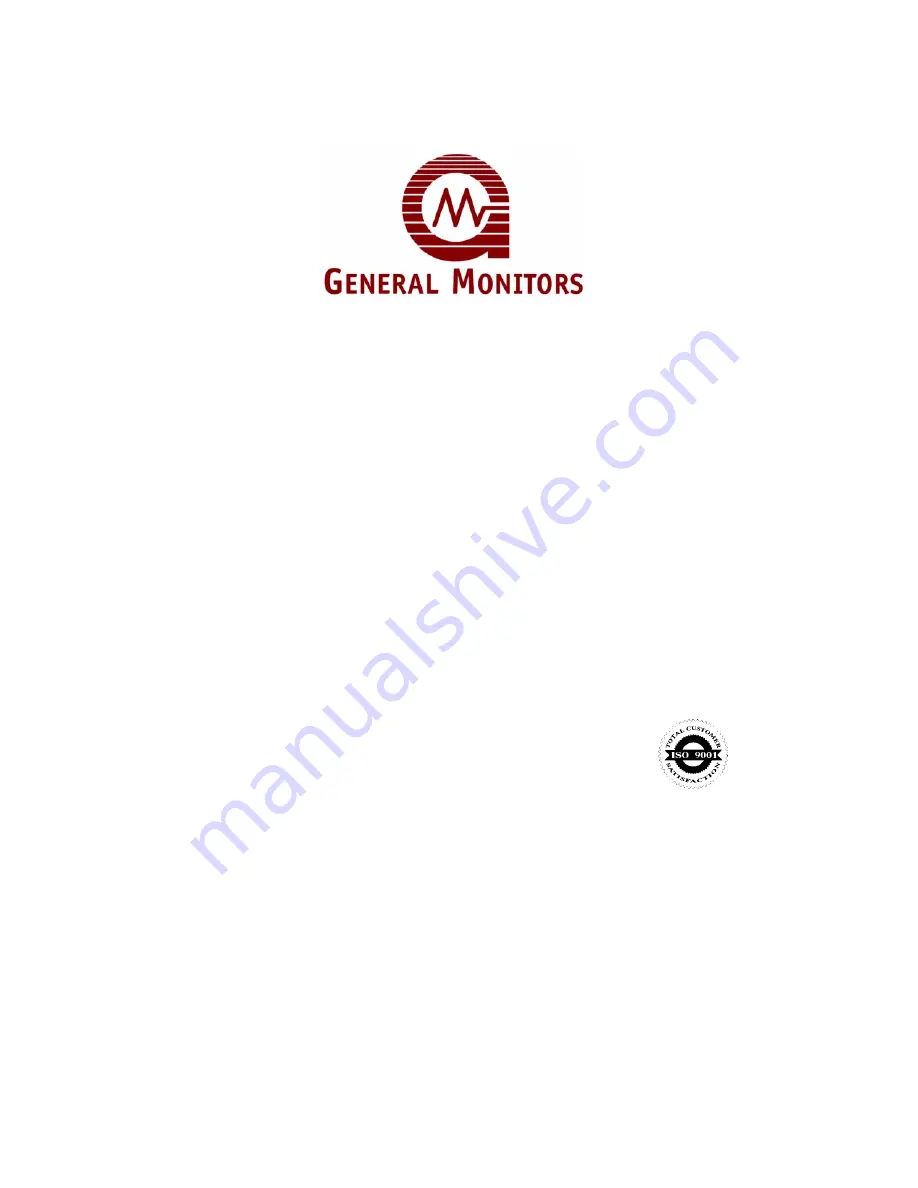
The information and technical data disclosed in
this document may be used and disseminated
only for the purposes and to the extent
specifically authorized in writing by General
Monitors.
Instruction
Manual
03-03
General Monitors reserves the right to change
published specifications and designs without
prior notice.
MANTS4000
Part
No.
MANTS4000
Revision
C/03-03
Model TS4000
Intelligent Sensor for
Toxic Gas Detection