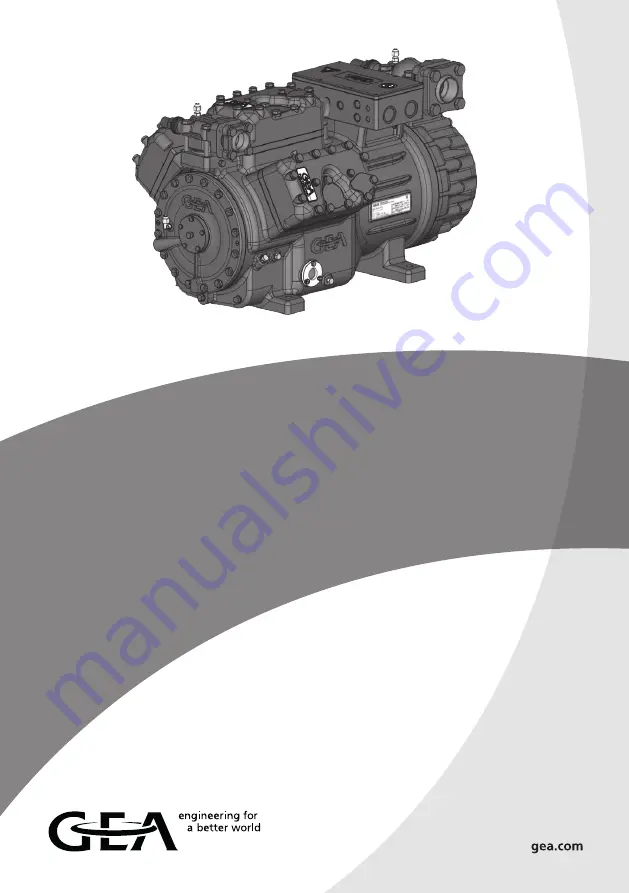
GEA Bock HG66e (HC/LG)
Assembly instructions
96446-09.2020-Gb
Translation of the original instructions
HG(X)66e/1340-4 (S)
HG66e/1340-4 (S) HC
HG(X)66e/1540-4 (S)
HG66e/1540-4 (S) HC
HG(X)66e/1750-4 (S)
HG66e/1750-4 (S) HC
HG(X)66e/2070-4 (S)
HG66e/2070-4 (S) HC
HGX66e/1340 ML 28 LG
HGX66e/1340 S 35 LG
HGX66e/1540 ML 34 LG
HGX66e/1540 S 40 LG
HGX66e/1750 ML 44 LG
HGX66e/1750 S 50 LG
HGX66e/2070 ML 50 LG
HGX66e/2070 S 60 LG
Summary of Contents for HG66e Series
Page 39: ......