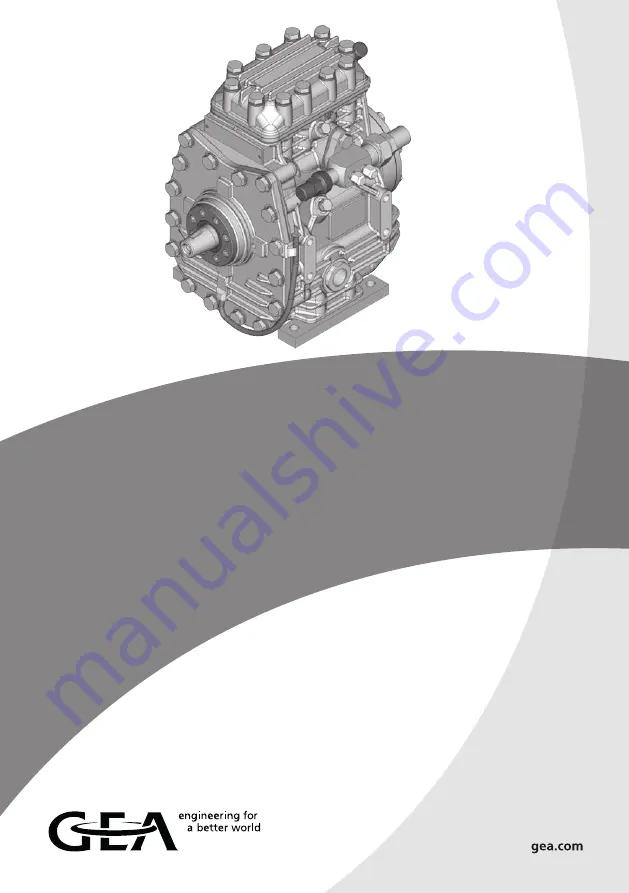
GEA Bock FK30
Assembly instructions
09705-01.2018-Gb
Translation of the original instructions
FK30/235 N
FK30/275 N
FK30/325 N
FK30/235 K
FK30/275 K
FK30/325 K
FK30/235 TK
FK30/275 TK
FK30/325 TK
FKX30/235 N
FKX30/275 N
FKX30/325 N
FKX30/235 K
FKX30/275 K
FKX30/325 K
FKX30/235 TK FKX30/275 TK FKX30/325 TK