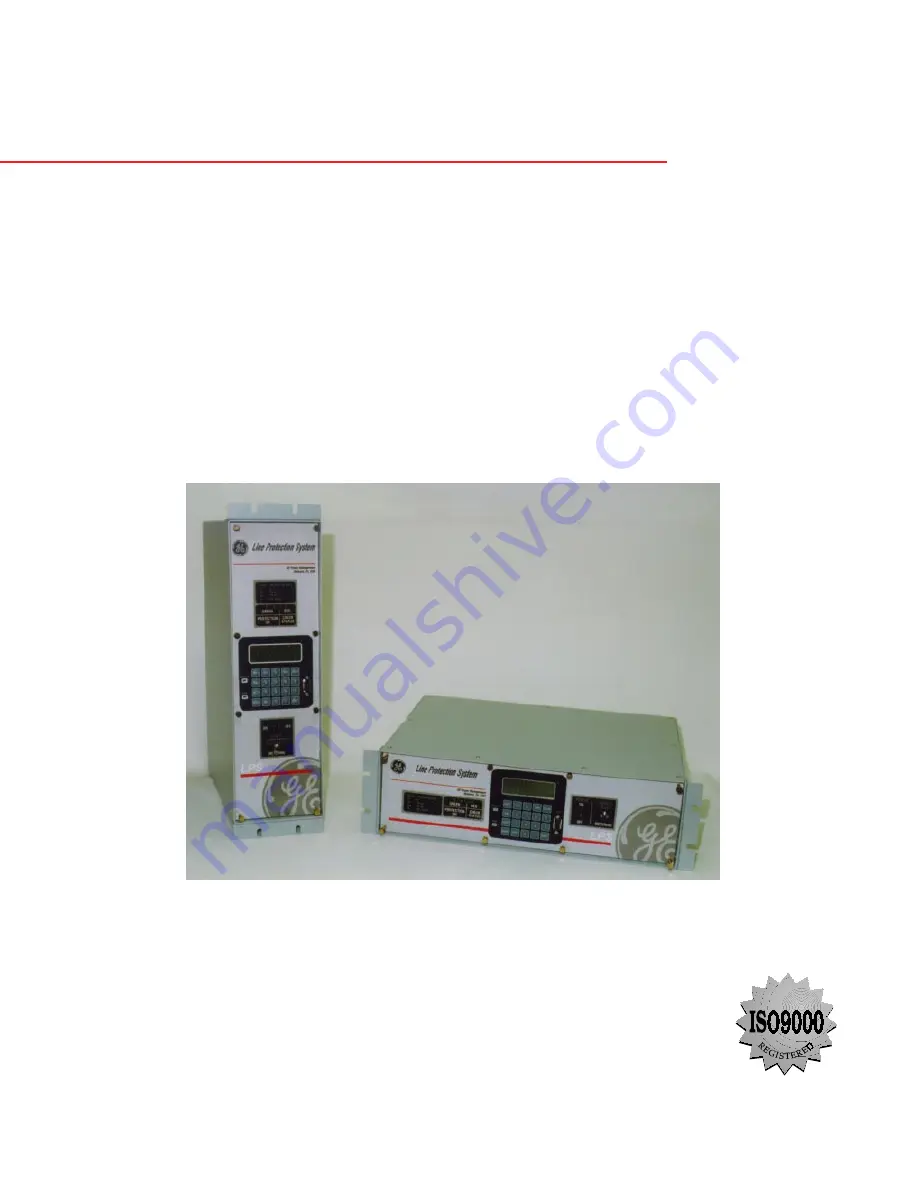
LPS-O
Line Protection™ System
Instruction Manual
LPS-O Revision: V0001.03AA20
Manual P/N: GEK-106266A
Copyright © 2001 GE Power Management
GE Power Management
215 Anderson Avenue, Markham, Ontario
Canada L6E 1B3
Tel: (905) 294-6222 Fax: (905) 201-2098
Internet: http://www.GEindustrial.com/pm/
Note: All relays must be powered up at least once per year to
avoid deterioration of electrolytic capacitors and
subsequent relay failure.
Manufactured under an
ISO9002 Registered system.
g
GE Power Management
Summary of Contents for LPS-O
Page 2: ......
Page 4: ......
Page 14: ...x LPS O Line Protection System GE Power Management TABLE OF CONTENTS ...
Page 208: ...9 8 LPS O Line Protection System GE Power Management 9 3 TROUBLESHOOTING 9 SERVICING 9 ...
Page 226: ...10 18 LPS O Line Protection System GE Power Management 10 8 HELP MENU 10 ALPS TEST PROGRAM 10 ...
Page 288: ...B 4 LPS O Line Protection System GE Power Management B 2 FIGURES APPENDIXB B ...
Page 292: ...C 4 LPS O Line Protection System GE Power Management C 1 KEYPAD MENUS APPENDIXC C ...
Page 294: ...D 2 LPS O Line Protection System GE Power Management D 1 WARRANTY INFORMATION APPENDIXD D ...
Page 306: ...xii LPS O Line Protection System GE Power Management INDEX INDEX ...
Page 307: ...GE Power Management LPS O Line Protection System NOTES ...