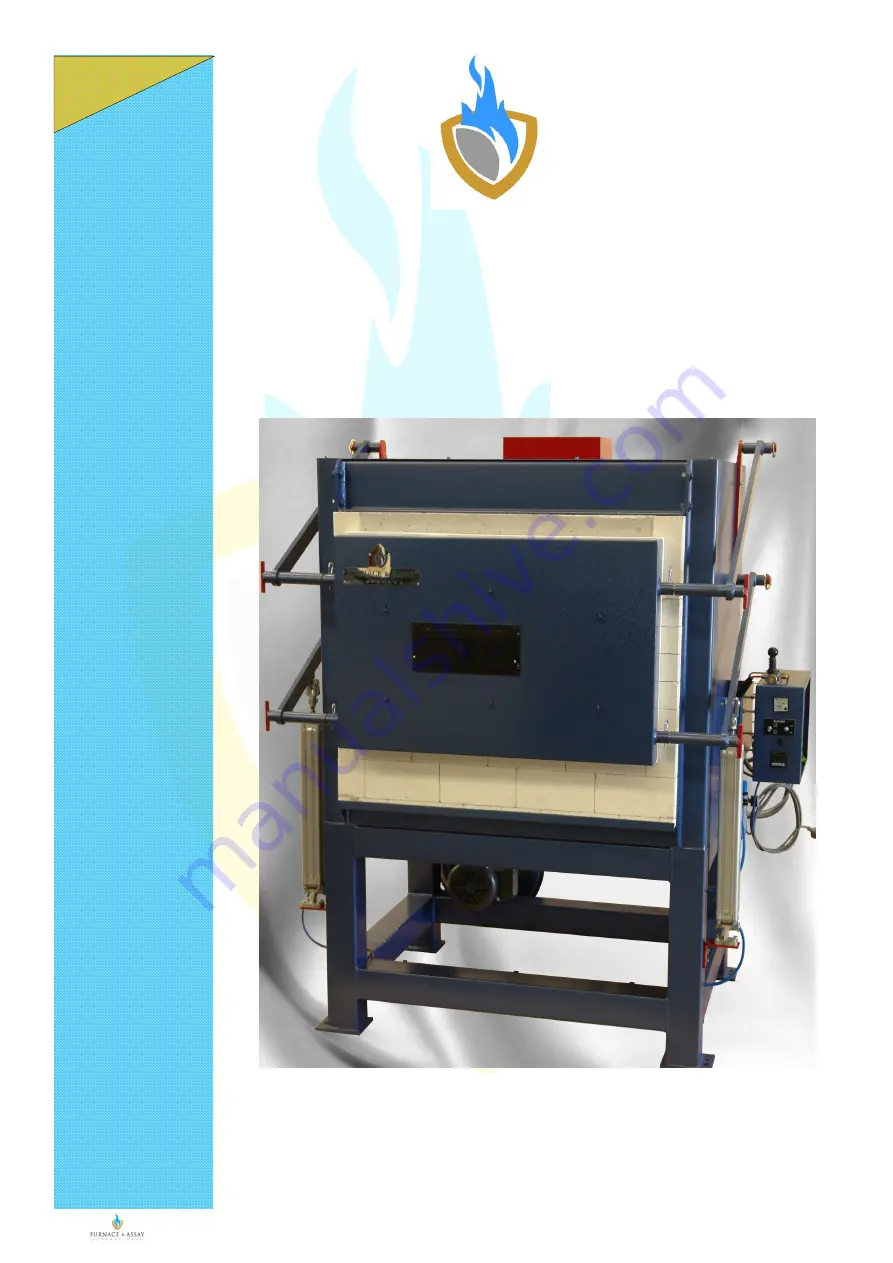
ABN: 68 606 541 468 Email: [email protected] 1
168 Place Cupellation Furnace
Operation & Maintenance Manual
Tel: +61 8 9399 9299
E-mail: [email protected]
Website: fandasupplies.com/
FURNACE & ASSAY
——
S U P P L I E S
—––
Fuel Source:
LPG
Manufacturing
Date
Electrical:
220-240V
Working Area
●
650mm Deep
●
650mm Wide
●
220mm High
Combustion
Chamber
Volume:
0.19
Swept Volume:
0.2