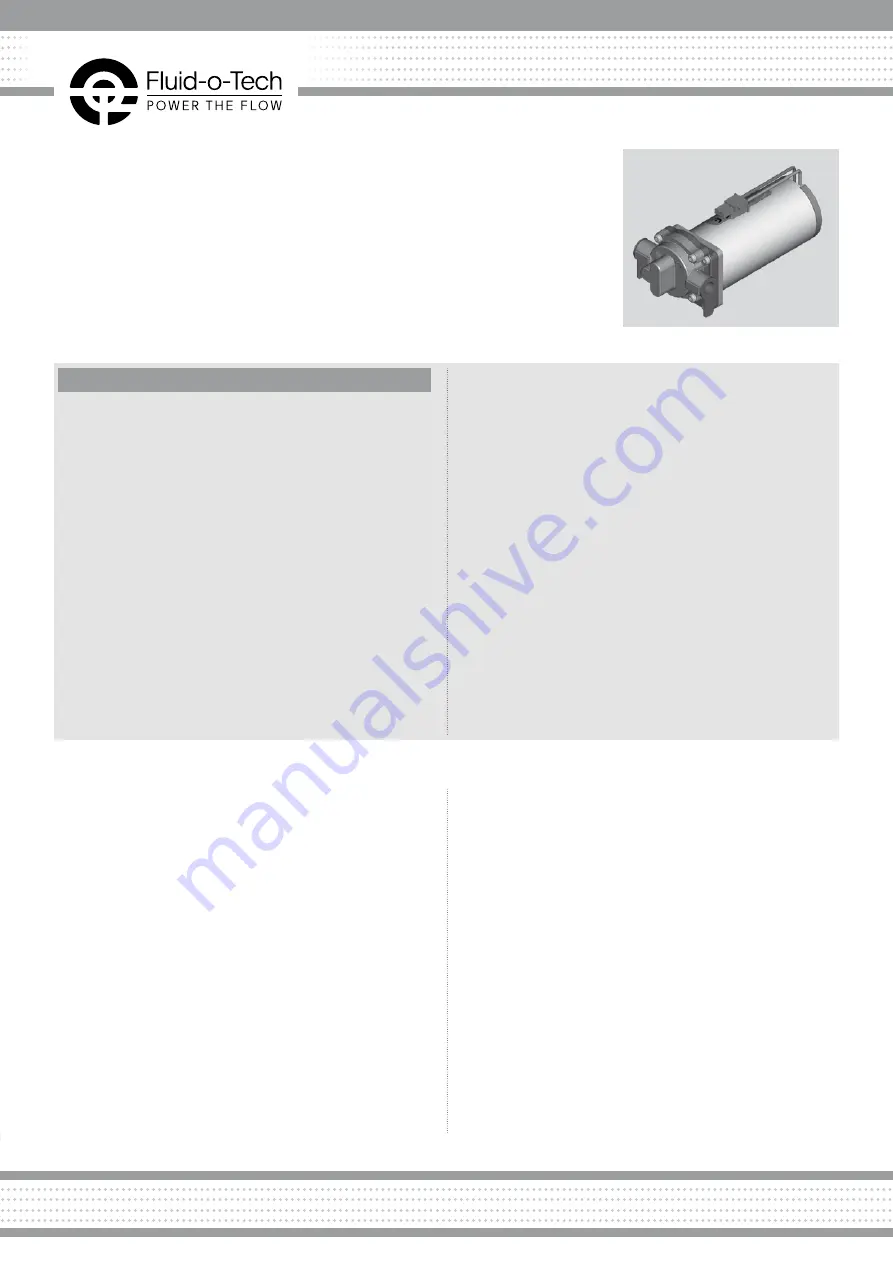
www.fluidotech.com
INSTRUCTION
MANUAL
GEAR PUMPS IN PEEK, DGD PRO SERIES
Please read the following instructions carefully before
conducting a new installation. DGD PRO series pumps
are direct drive. They must only be handled by specialised
personnel who have the basic technical knowledge related
to electromechanical and hydraulic installations.
WARNINGS
DGD PRO series gear pumps are normally assembled with
non-protected motors in the case of “locked rotor”. This is
why we recommend inserting a fuse and adequately sized
components in a power supply circuit to withstand this
condition.
Inadequate circuits and/or components may overheat, causing
damage and/or a fire. Before connecting the motor it is
necessary to check the polarity is correct. During installation
be careful not to inverse the polarity, in which case the pump
would rotate in the opposite direction and for some motors this
could cause permanent damage to the unit itself.
The unit cannot operate continuously but only in ON/OFF
cycles. It must be installed in a ventilated space in order to
dissipate the heat produced by the motor. In order to avoid
noise and vibrations on mechanical parts, we recommend
installing the unit with rubber anti-vibration mounts. Take
special care when connecting the pump to the fittings in order
to prevent potential leaks. We recommend removing the plastic
plugs located on the pump’s intake and delivery ducts only just
before mounting the fittings and pipes to prevent solid foreign
objects from entering inside, as they could damage the internal
components of the pump. Do not use liquid sealant as drops
could fall in the ducts and cause the pump to block. For use in
the food industry, the pumps (even if NSF-certified) must first
be sterilised by circulating water inside them at a temperature
of 80°C. The water used for this operation must not be reused
during the sterilisation or thereafter, but must be flushed
away. If the unit is replaced, it is necessary to ensure that the
model matches the one being replaced. The circuit must be
thoroughly cleaned and rinsed before starting up the unit.
INSTALLATION
GENERAL SAFETY ADVICE
1
The DGD PRO pumps are often driven with DC motors with
brushes, a known source of ignition. Do not use these motors
in potentially explosive atmospheres.
2
After prolonged use or applications with hot fluids, the surfaces
of the pump and motor could be hot and potentially cause
injury to skin or burns. After disconnecting the power supply,
wait for the pump to cool down before touching it.
3
Do not place the pump near materials with low auto-ignition
temperature/flammable materials. The outer surfaces of the
unit can reach high temperatures. Install the pump in a dry area
protected from dust, splashes and condensation.
4
Often motors are cooled by natural convection. We recommend
installing the unit in areas where maximum and adequate
ventilation is ensured. As an indication, the minimum distance
from the walls around the unit should be at least 50 mm. Do
not wrap the unit with insulation material and do not install it
near hot surfaces. Do not use the pump in environments or
with fluids at temperatures higher than those reported in the
catalogue.
5
Check the compatibility with the fluid used beforehand. Do not
use or allow the pump to come in contact with chemicals that
could damage the unit.
6
An inadequate circuit could cause excessive pressure or
overheating. Make sure the unit is used in accordance with
to the curves in the catalogue. Install the hydraulic circuit
with adequate safety margins, both in terms of pressure and
temperature. We recommend a minimum safety factor of
1.5. Protect the DGD PRO units from frost. Freezing could
permanently damage the pump and pipes.
7
The DGD PRO units are low voltage devices, though it is still
necessary to comply with the relevant safety standards. The
installer is responsible for making sure current regulations,
closely associated with the final application, are complied with.
8
Insert a filter of a suitable size upstream of the pump to prevent
solid particles with a diameter greater than 10μm from entering
inside. The surface of the filter must be sized in relation to the
flow rate and type of circuit in order to prevent excessive drops in
pressure. This filter must be cleaned periodically. If the filter is not
kept clean, the pump may operate in cavitation and break quickly