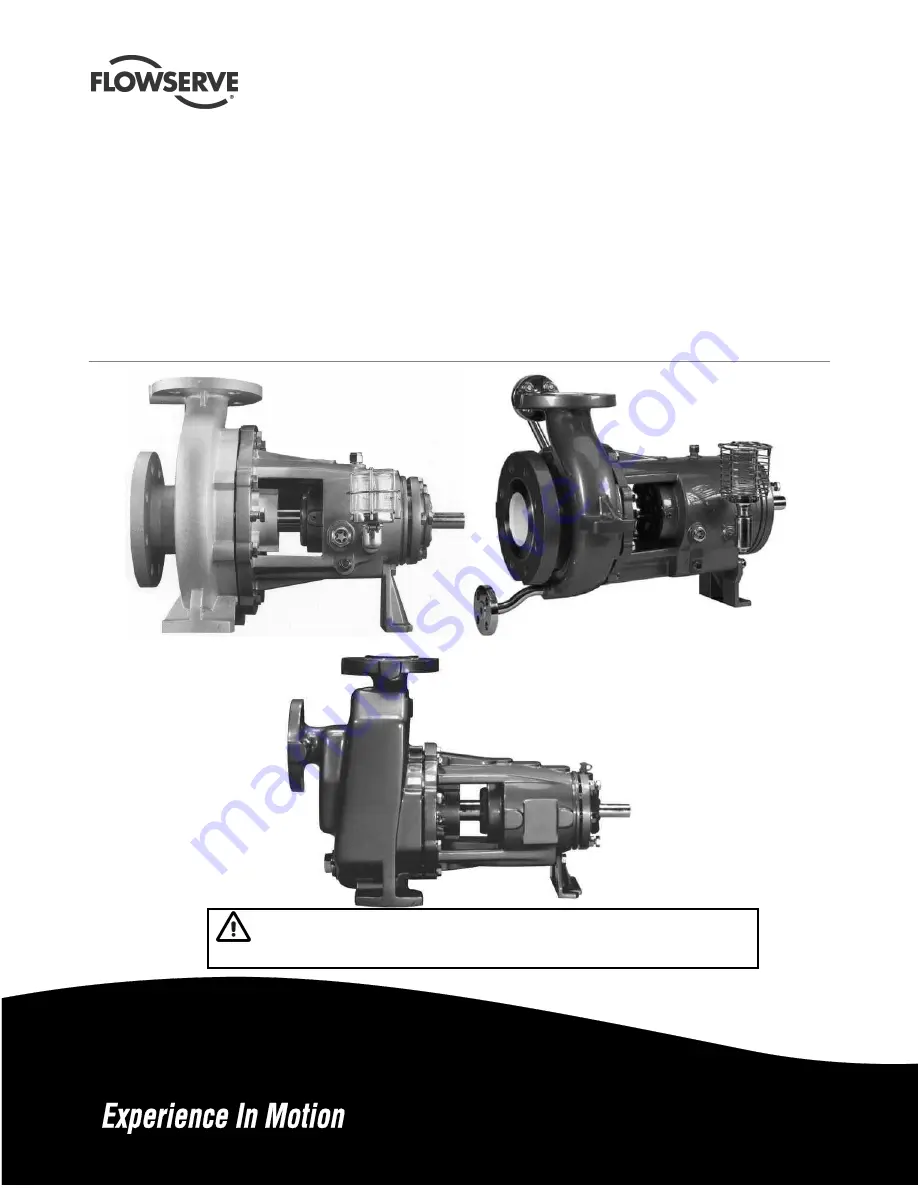
USER INSTRUCTIONS
CPX, CPXR, CPXN and CPXP
Single stage, end suction, centrifugal, chemical process
pumps
PCN=71569117 02-10 (E) (Based on C937KH013, C937KH054,
C961KH001 and C937KH067.) Original instructions.
Installation
Operation
Maintenance
These instructions must be read prior to installing,
operating, using and maintaining this equipment.