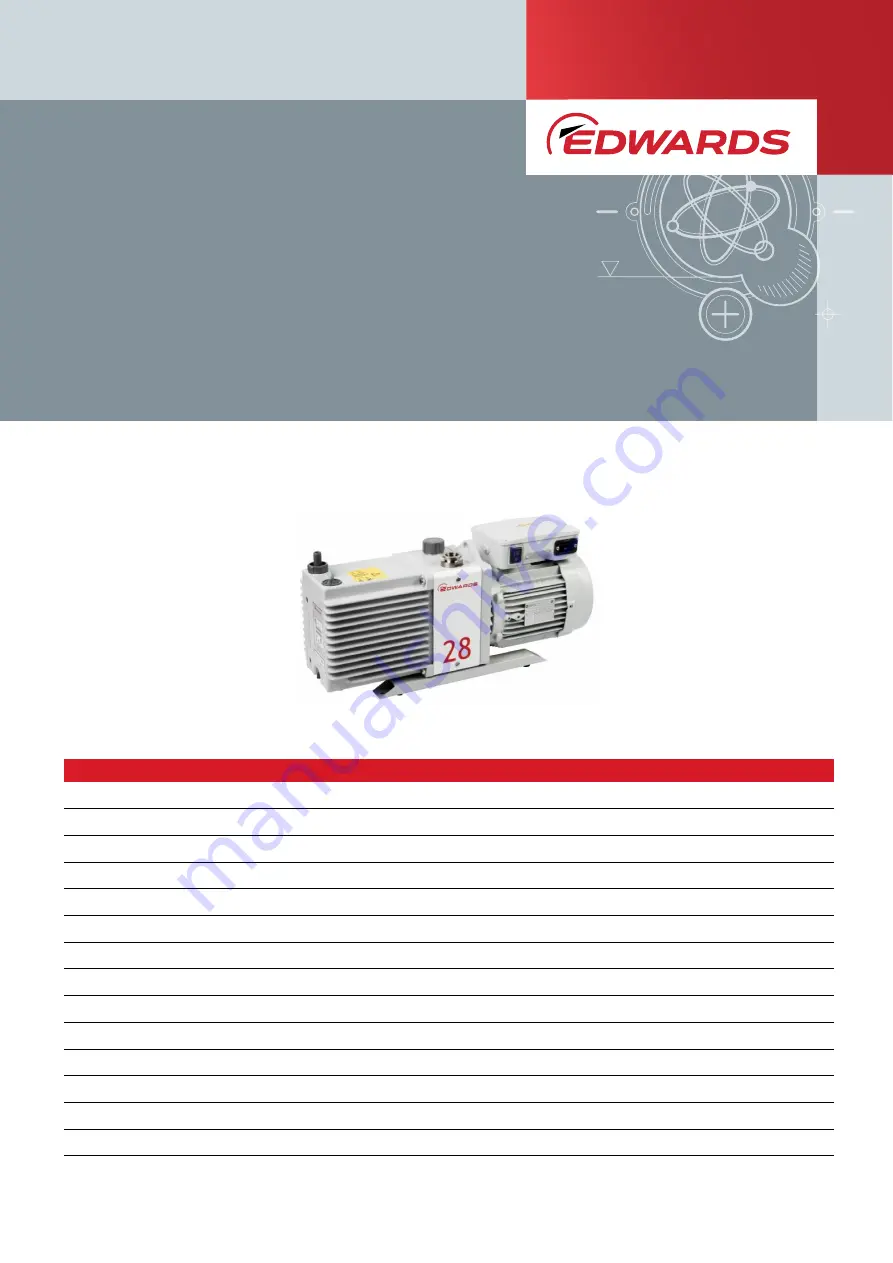
E2M28 and E2M30 Rotary
Vacuum Pumps
INSTRUCTION MANUAL
A37310880_V
Original instructions
edwardsvacuum.com
DESCRIPTION
ITEM NUMBER
E2M28, 100/200 V, 50 Hz or 100-105/200-210 V, 60 Hz, single-phase
A37315904
E2M28, 115/230 V, 60 Hz, single-phase
A37315981
E2M28, 200-240 V, 50 Hz, or 230-240 V, 60 Hz, single-phase
A37315903
E2M28, 380/400 V, 50 Hz, or 230/460 V, 60 Hz, three-phase
A37333940
E2M28, 200 V 50/60 Hz, or 380 V, 60 Hz, three-phase
A37333934
E2M28, 200-240 V, 50 Hz, or 230-240 V, 60 Hz, single-phase (Amphenol)
A37316903
E2M28, 110/200-240 V, 50 Hz, or 115-120/200-230 V, 60 Hz, single-phase
A37317984
E2M28-FF, 110/220-240 V, 50 Hz, or 115/200-230 V, 60 Hz, single-phase, (Fomblin) filled A37325984
E2M28-FF, 220/240 V, 50 Hz, or 230/240 V, 60 Hz, single-phase
A37325903
E2M28-FF, 380/400 V, 50 Hz, or 230/460 V, 60 Hz, three-phase
A37343940
E2M28-FF, 200 V, 50/60 Hz, or 380 V, 60 Hz, three-phase
A37343934
E2M30, 100/200 V, 50 Hz or 100-105/200-210 V, 60 Hz, single-phase
A37415904
E2M30, 115/230 V, 60 Hz, single-phase
A37415981
E2M30, 200-240 V, 50 Hz, or 230-240 V, 60 Hz, single-phase
A37415903
Summary of Contents for A37315903
Page 6: ...This page has been intentionally left blank ...
Page 55: ...Page 51 A37310880_V Service ...
Page 56: ...edwardsvacuum com ...