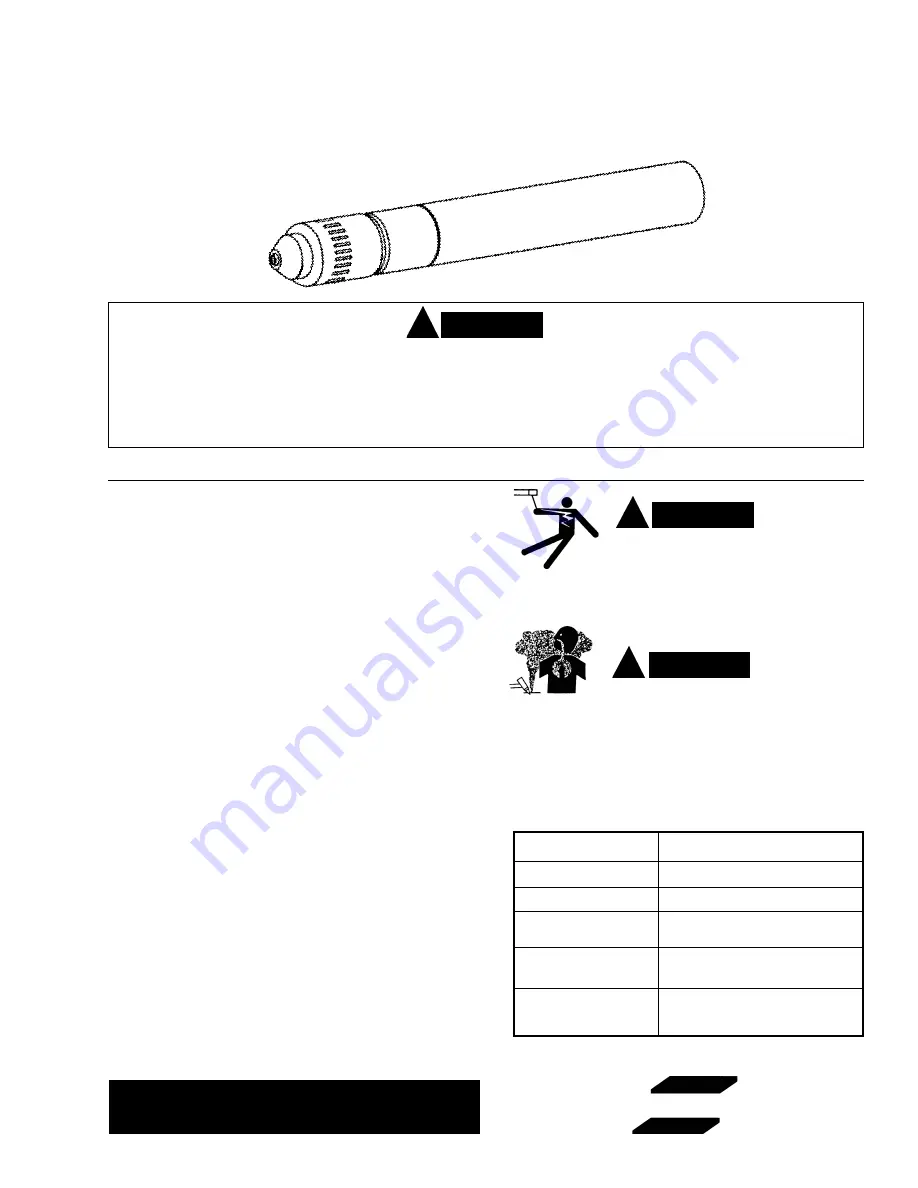
Current Rating
Duty Cycle
Diameter of Torch
Length of Torch W/O
Leads
Cooling Requirements
Gas Consumption
(Arc On)
260A
(150 A w/PCM-150 0r PCM-1500)
100%
2 in. (50.8mm)
15.5 inches (393.7mm)
0.75 gpm min. @ 90 psig (150 A)
1.00 gpm min. @ 120 psig (250 A)
35 cfh (50 A)
65 cfh (150 AA)
110 cfh (250A)
Table 1-1. PT-19XL Specifications
!
DANGER
High Voltage can kill
Disconnect Power supply from incoming electrical
power before touching or servicing the torch. Metal
parts of the torch can be at high voltage.
PLASMA Cutting can produce Deadly Fumes, Fire,
or Explosion.
• Gases used for plasma cutting can cause suffoca-
tion, fire, or explosion.
• Loud noise from plasma cutting can cause hear-
ing loss.
!
DANGER
1.1 INTRODUCTION
The PT-19A is a mechanized torch designed for plasma
arc cutting without water injection. The torch is water
cooled for long consumable life at high currents.
1.2 AVAILABLE MODELS
P/N 34956 Torch Assembly PT-19XL 4-1/2 ft.*
P/N 34093 Torch Assembly PT-19XL 6 ft.*
P/N 34094 Torch Assembly PT-19XL 12 ft.*
P/N 34090 Torch Assembly PT-19XL 15 ft.*
P/N 34095 Torch Assembly PT-19XL 17 ft.*
P/N 34091 Torch Assembly PT-19XL 20 ft.*
P/N 34092 Torch Assembly PT-19XL 25 ft.*
P/N 20390 Torch Assembly PT-19XL 50 ft**
*Used on the ESP-1000 Plasma Cutting Outfits with ESP
ULTRA-LIFE 300 or ESP-400 Power Sources. Also used
on PCM-1500 console units modified for use with PCC-
12 control.
**Used on PCM-150 or PCM-1500 console units with
PCC-11 control.
NOTE
All of the above torches can be used with PCM-8XL pack-
ages. Use of 34090 through 34095 with PCC-11/PCM-
150 packages require modification of PCC-11 control (see
Section 3).
NOTICE:
This torch and its components are protected by
various U.S. and foreign patents with additional patents pend-
ing. It is the policy of ESAB Welding & Cutting Products to react
vigorously to patent infringement of unauthorized manufac-
ture, sale, or use of its patented products or spare parts.
CAUTION
!
These instructions are for experienced operators. If you are not fully familiar with the principles of operation and safe
practices for arc welding equipment, we urge you to read our booklet, “Precautions and Safe Practices for Arc
Welding, Cutting and Gouging,”, Form 52-529. Do NOT permit untrained persons to install, operate, or maintain this
equipment. Do NOT attempt to install or operate this equipment until you have read and fully understand these
instructions. If you do not fully understand these instructions, contact your supplier for further information. Be sure
and read the Safety Precautions (pages 2 & 3) before installing or operating this equipment.
SECTION 1 INTRODUCTION
INSTRUCTIONS
for
F-15-147-A
January, 1996
PT-19XL MECHANIZED
PLASMARC CUTTING TORCH
Be sure this information reaches the operator.
You can get extra copies through your supplier.
ESAB
ESAB Welding &
Cutting Products