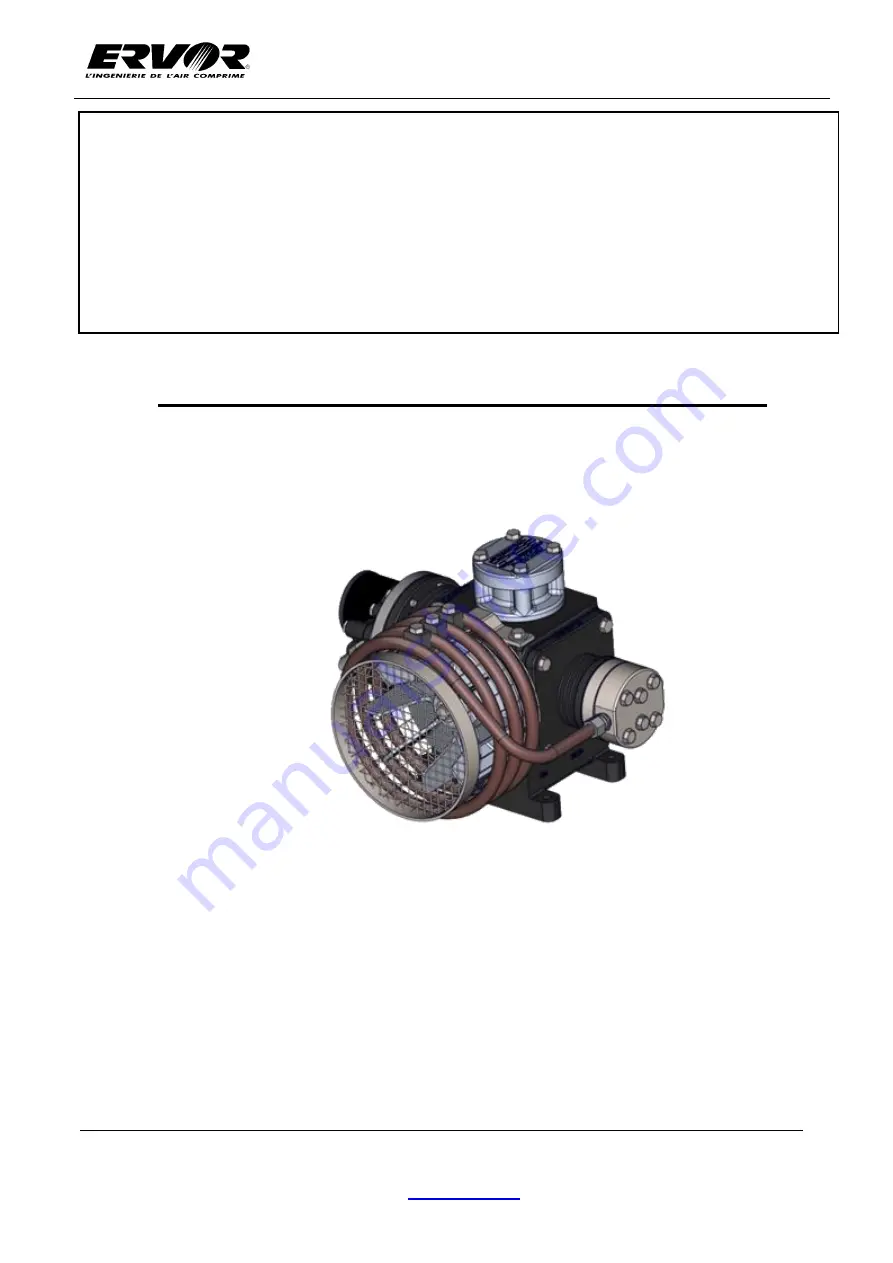
Rev. : A
Date : 05/05/20
Operating and Maintenance Manual for Air compressor G04
All rights reserved copyright - We reserve the right to make technical modifications - Illustrations are not contractual
8_101_000
ERVOR
(SCA)
– Z.I. du Val d’Argent
6 rue Désiré Granet - 95100 ARGENTEUIL
– France
(33) 1 34 11 50 00
(33) 1 34 11 50 10
Web :
Page : 1/37
AIR COMPRESSOR G04
(Ref: 8101000)
OPERATING AND MAINTENANCE MANUAL