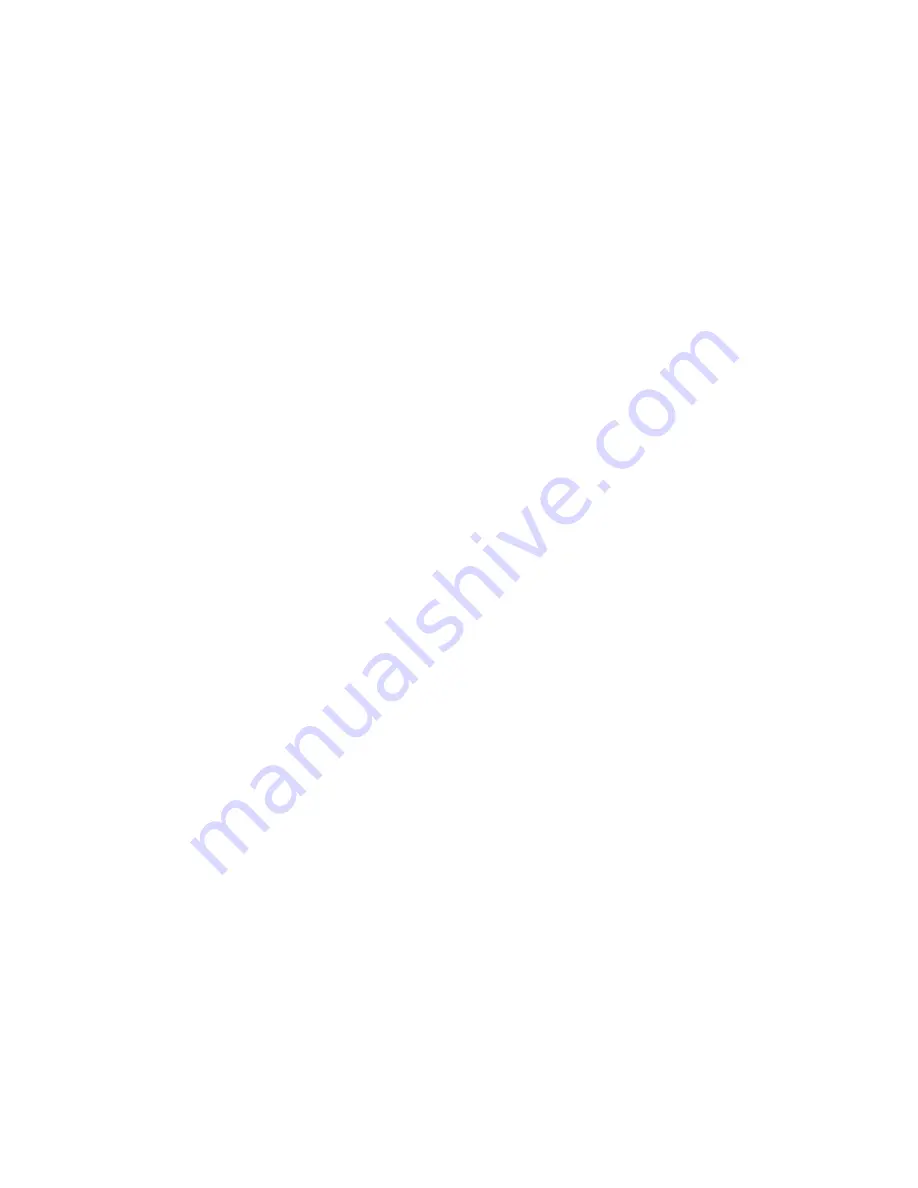
University of Arkansas Animal Facility
700 Research Center Blvd.
Fayetteville, AR. 72701
Tag: AHU / CU
Liebert/Vertiv Closeout Documentation
•
Liebert MiniMate User Manual (AHU)
•
Liebert PFH Condenser User Manual (CU)
•
Liebert Warranty
ITS Solutions
5200 Northshore Dr.
North Little Rock, AR. 72118
501-687-0286
Dated 7/13/2020
Summary of Contents for PFH020A-L
Page 3: ......
Page 74: ...Liebert Prop Fan Condensing Unit 50 Hz and 60 Hz Installer User Guide ...
Page 77: ...5 Troubleshooting 37 Vertiv Liebert PFH Installer User Guide ii ...
Page 86: ...Figure 2 6 General piping arrangement Vertiv Liebert PFH Installer User Guide 9 ...
Page 105: ...Vertiv Liebert PFH Installer User Guide 28 This page intentionally left blank ...
Page 109: ...Vertiv Liebert PFH Installer User Guide 32 This page intentionally left blank ...
Page 116: ......