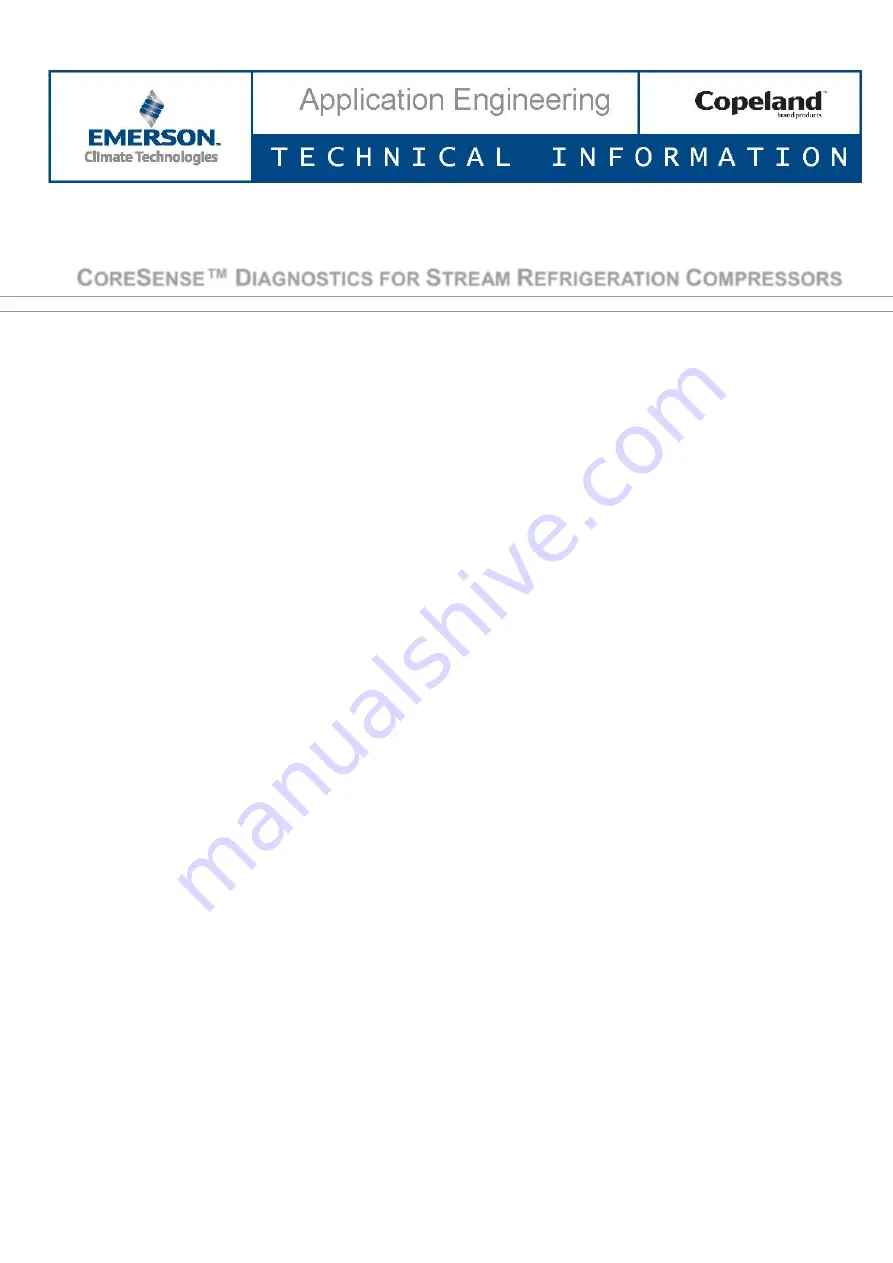
D7.8.4/0112-0415/E
1/17
Date of last update: Apr-15
Ref: D7.8.4/0112-0415/E
Application Engineering Europe
C
ORE
S
ENSE
™
D
IAGNOSTICS FOR
S
TREAM
R
EFRIGERATION
C
OMPRESSORS
3.10 Flash memory information ........................................................................................................................... 5
3.11 Modbus® communication ............................................................................................................................. 6
3.12 Reset ............................................................................................................................................................. 7
3.13 Alarm history and running conditions .......................................................................................................... 7
3.14 Compressor status codes .............................................................................................................................. 7
3.15 LEDs on the module to display the failure alarms ........................................................................................ 7
3.16 Oil functionality self-test option ................................................................................................................... 9