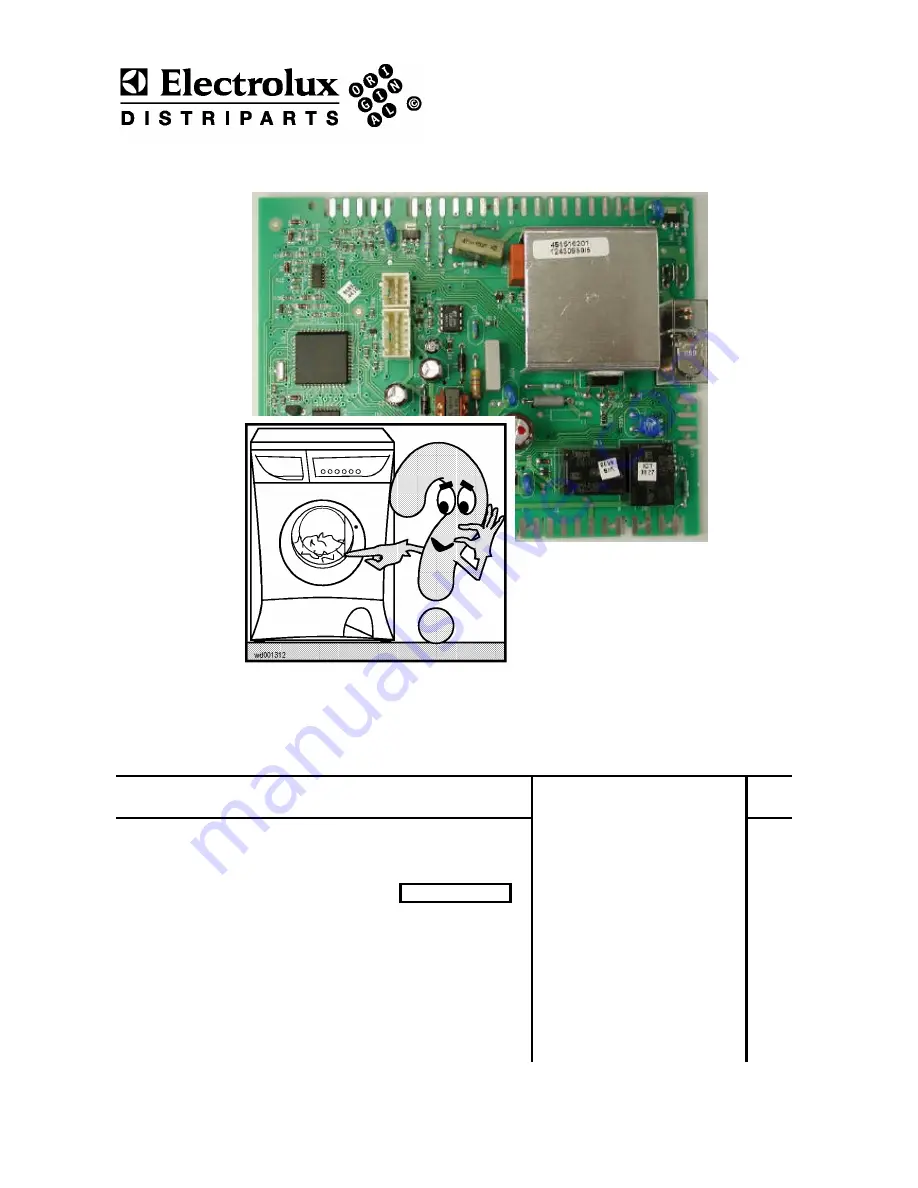
SSD-P APdV, EB, HD 01/05
I
599 34 71-47
SERVICE MANUAL
WASHING
Publication no.
599 34 71-47
ELECTROLUX-ZANUSSI S.p.A.
SPARE & SERVICE DOCUMENTATION
Corso Lino Zanussi,30
I - 33080 PORCIA /PN
ITALY
Fax +39 0434 394096
Edition: 2001.05.
31
EN/eb
Diagnostics Guide to
EWM2000 Electronic
Control
WASHING MACHINES
&
WASHER DRYERS
Production:
ZP Porcia (Italy)
Summary of Contents for EWM2000
Page 2: ...SSD P APdV EB HD 01 05 II 599 34 71 47 ...
Page 6: ...SSD P APdV EB HD 01 05 VI 599 34 71 47 ...
Page 56: ...BASIC CIRCUIT DIAGRAM SSD P APdV EB HD 01 05 11 1 599 34 71 47 AC MOTOR ...
Page 57: ...BASIC CIRCUIT DIAGRAM SSD P APdV EB HD 01 05 11 2 599 34 71 47 DC MOTOR ...
Page 73: ...SSD P APdV EB HD 01 05 14 10 599 34 71 47 pic 34 pic 35 PICTURES LINKED TO FAULT FINDING ...
Page 74: ...NOTES SSD P APdV EB HD 01 05 14 11 599 34 71 47 ...