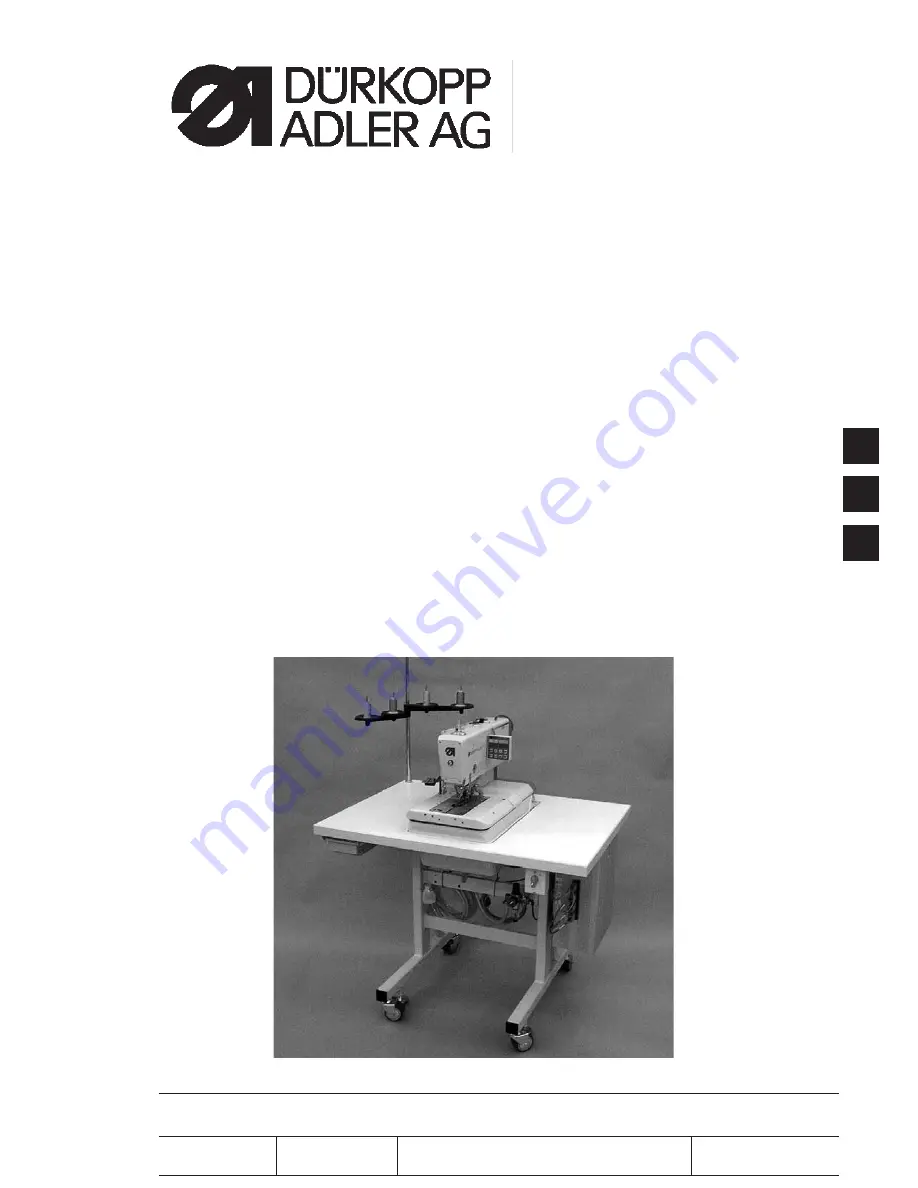
559
Doppelkettenstich Knopflochautomat
Einfachkettenstich Schnürlochautomat
Automatic double-chainstitch buttonholer
Automatic single-chainstitch eyelet machine
Bedienanleitung / Operating Instructions
Aufstellanleitung / Installation Instructions
Serviceanleitung /
Service Instructions
Postfach 17 03 51, D-33703 Bielefeld
Potsdamer Straße 190, D-33719 Bielefeld
T49 (0) 5 21/ 9 25-00
T49 (0) 5 21/ 9 25 24 35
www.duerkopp-adler.com
1
2
3
Ausgabe / Edition:
Änderungsindex
Teile-Nr./Part.-No.:
07/2007
Rev. index:
01.0
Printed in Federal Republic of Germany
0791 559001