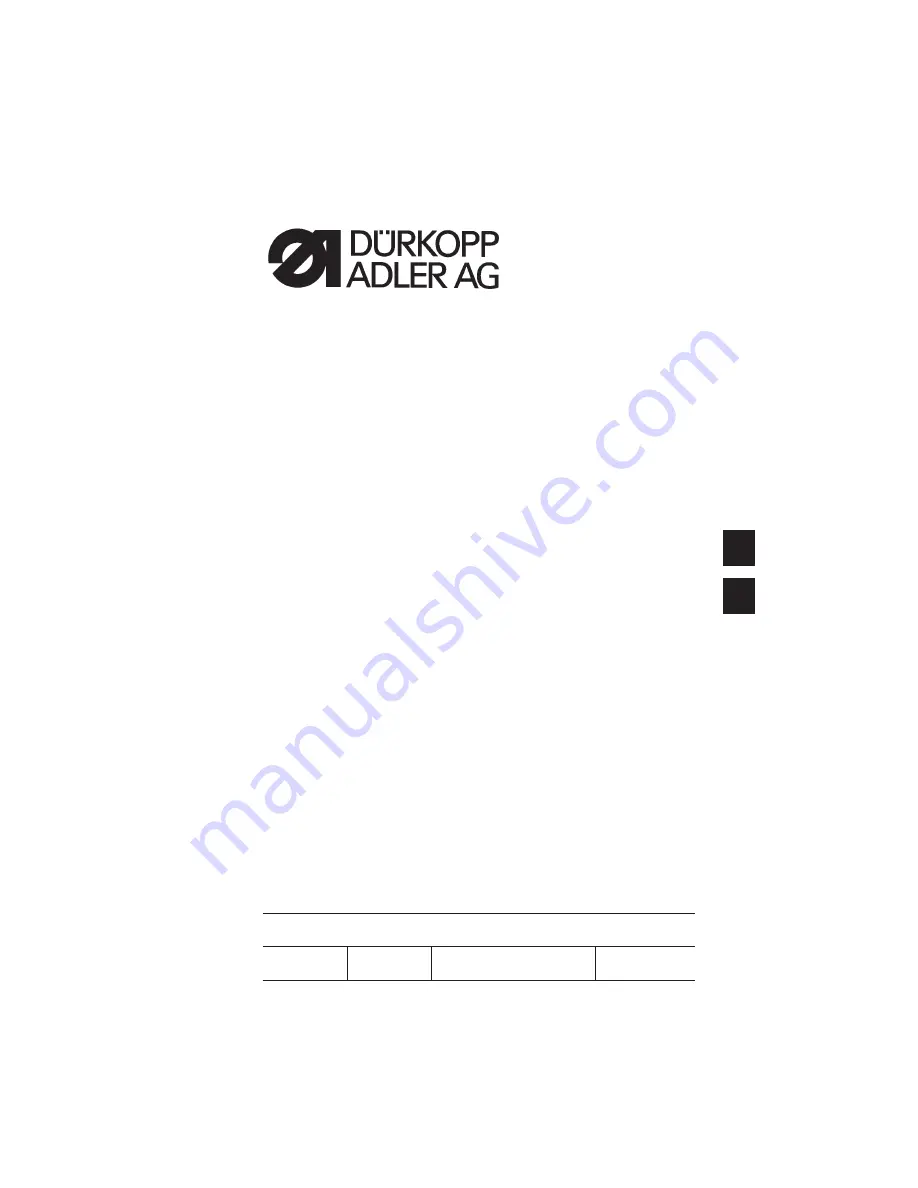
275
Spezialnähmaschine
mit Direktantrieb
Betriebsanleitung
Instruction manual
Postfach 17 03 51, D-33703 Bielefeld • Potsdamer Stra
ß
e 190, D-33719 Bielefeld
T49 (0) 521/ 9 25 - 00 • T49 (0) 521/ 9 25 24 35 • www.duerkopp-adler.com
GB
D
Ausgabe / Edition:
Änderungsindex
Teile-Nr./Part.-No.:
02/2002
Rev. index:
00.0
Printed in Germany
0791 275740
Summary of Contents for 275
Page 36: ......