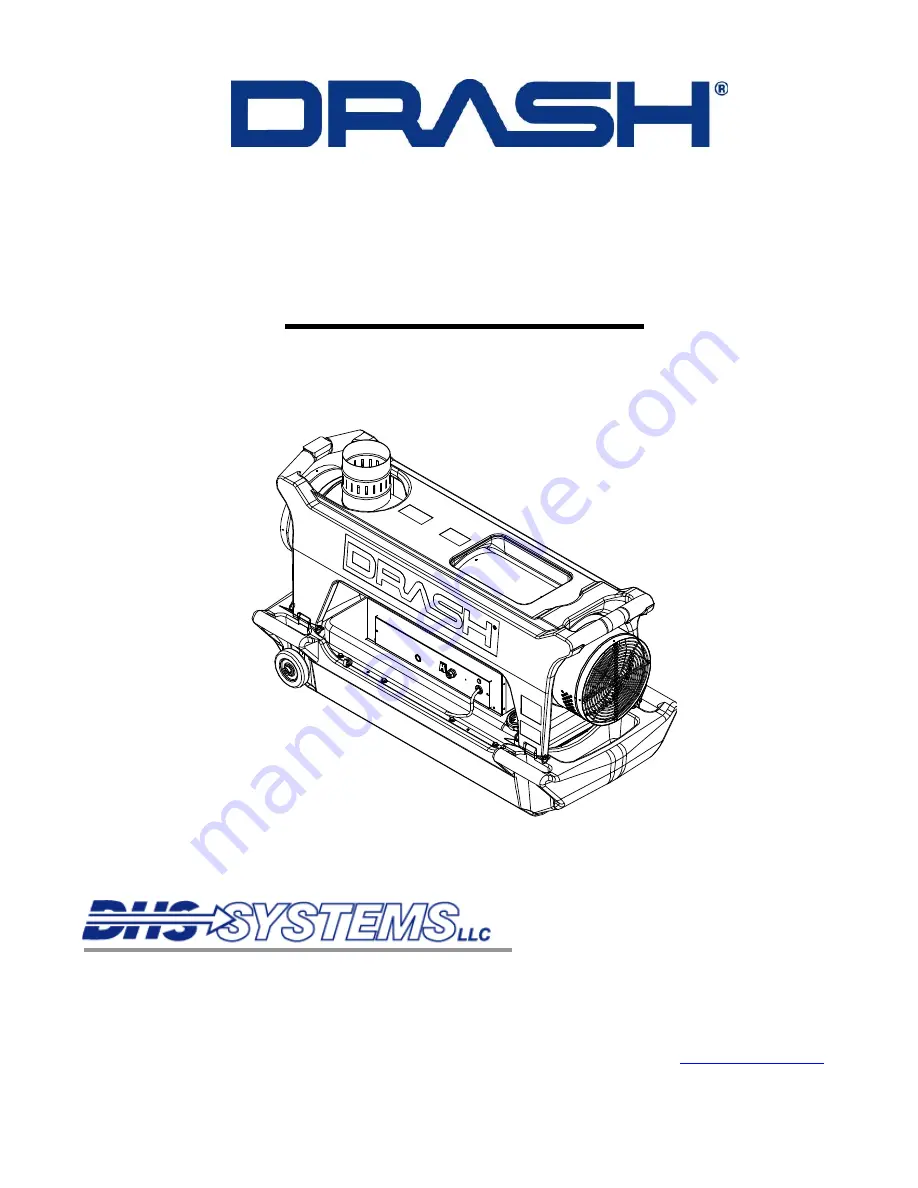
D-1000B HEATER
Outdoor Use Only
OPERATIONS & MAINTENANCE MANUAL
ISO 9001: 2000 Registered
Quality Management System
33 Kings Highway, Orangeburg, NY 10962
Phone: 845-359-6066
Fax: 845-365-2114
Hotline:
800-977-3647
DHS Manual Part Number: 1006395
Web: www.drash.com
Revision
Date:
01
APRIL
2010
Email: