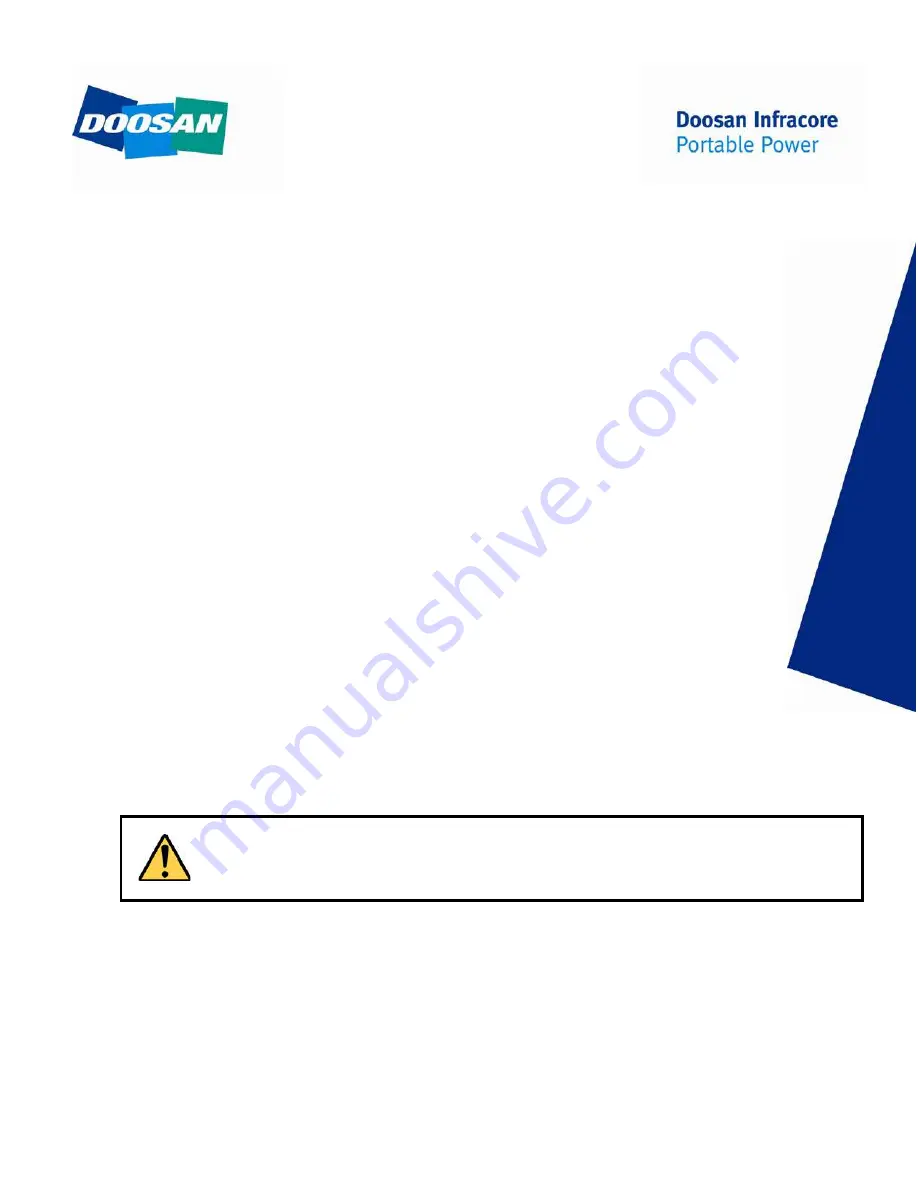
COMPRESSOR MODEL
P600/XP535WCU-T4i (E90)
HP450/VHP400WCU-T4i (E91)
Doosan Infracore Portable Power
1293 Glenway Drive
Statesville, N.C. 28625
DoosanPortablePower.com
P/N: 46614501 (07-2012) Rev A
This manual contains important safety information.
Do not destroy this manual.
This manual must be available to the personnel who operate and maintain this compressor.
OPERATION and MAINTENANCE
MANUAL
Summary of Contents for HP450/VHP400WCU-T4i
Page 2: ...2 ...
Page 6: ...6 ...
Page 7: ...7 Foreword ...
Page 10: ...Operation Maintenance Manual Foreword 10 ...
Page 11: ...11 Safety ...
Page 21: ...Safety Operation Maintenance Manual 21 ...
Page 22: ...Operation Maintenance Manual Safety 22 ...
Page 23: ...Safety Operation Maintenance Manual 23 ...
Page 28: ...Operation Maintenance Manual Safety 28 ...
Page 29: ...29 Noise Emission ...
Page 35: ...35 General Data ...
Page 38: ...Operating Maintenance Manual General Data 38 ...
Page 39: ...39 Operating Instructions ...
Page 56: ...Operating Maintenance Manual Operating Instructions 56 ...
Page 57: ...57 Maintenance ...
Page 74: ...Operation Maintenance Manual Maintenance 74 ...
Page 75: ...75 Lubrication ...
Page 79: ...79 Troubleshooting ...
Page 99: ...Troubleshooting Operation Maintenance Manual 99 ...
Page 100: ...Operation Maintenance Manual Troubleshooting 100 ...
Page 101: ...103 Options ...
Page 107: ...Revision History Rev EC Number Comments A CN023581 Original release ...