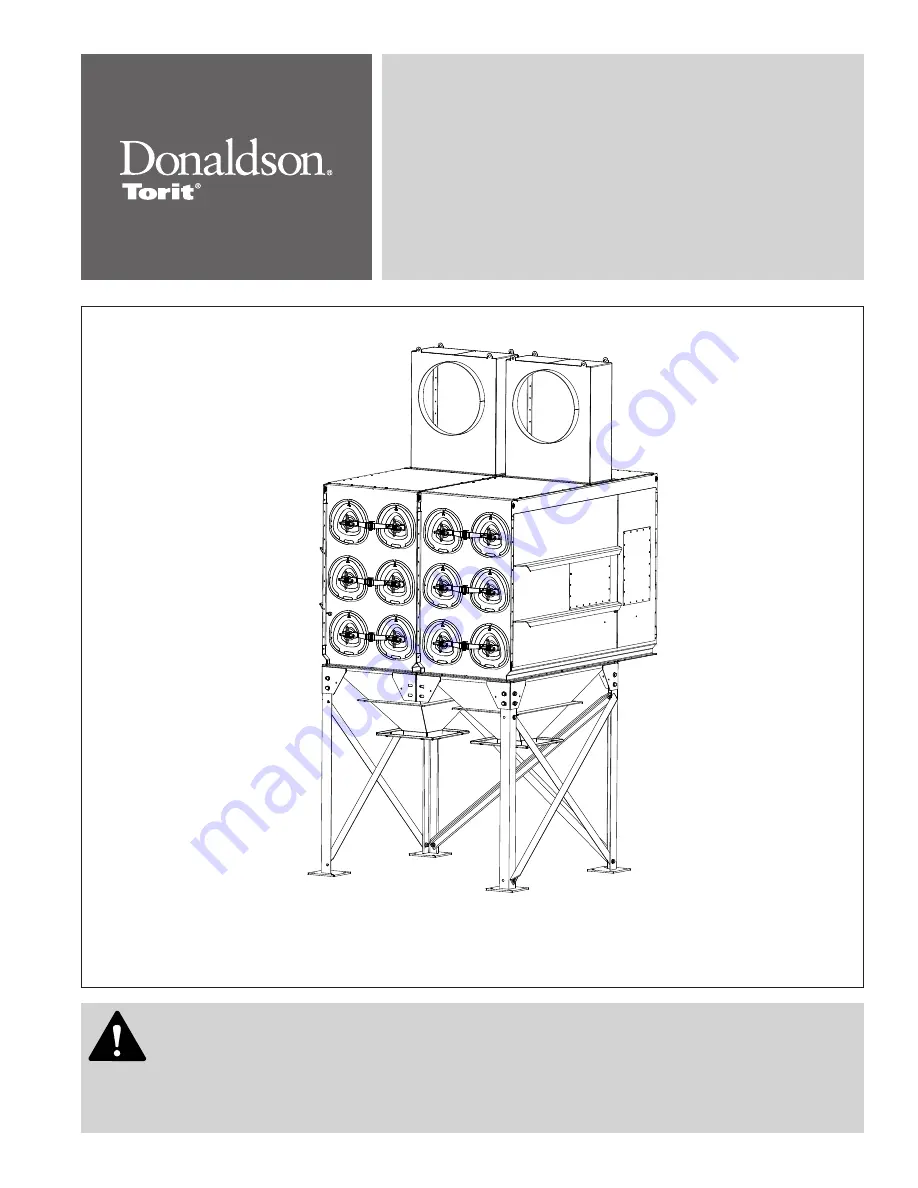
Downflo
®
Evolution
DFE 2-8, 2-12, 3-12, 3-18, 3-24, 3-36, 3-48, 3-60, 3-72, 4-16, 4-24,
4-32, 4-48, 4-64, 4-80, 5-20, 5-30, 5-40, 5-60 and 5-80
Installation and Operation Manual
Installation, Operation, and Service Information
This manual contains specific precautions related to worker safety. The hazard alert image denotes
safety related instructions and warnings in this manual. DO NOT operate or perform maintenance on this
collector until you have read and understood the instruction and warnings contained within this manual.
IOM AG8249101 (ENG)
Revision 3
English
Master Language
Summary of Contents for DFE 2-4
Page 42: ...A 1 Donaldson Company Inc Appendix A Clean Change Bag In Bag Out Filter and Liner System...
Page 56: ...B 2 Donaldson Company Inc Service Notes Date Service Performed Notes...
Page 57: ...Downflo Evolution DFE 2 8 to 5 80 B 3 Date Service Performed Notes...
Page 58: ...B 4 Donaldson Company Inc Date Service Performed Notes Service Notes...