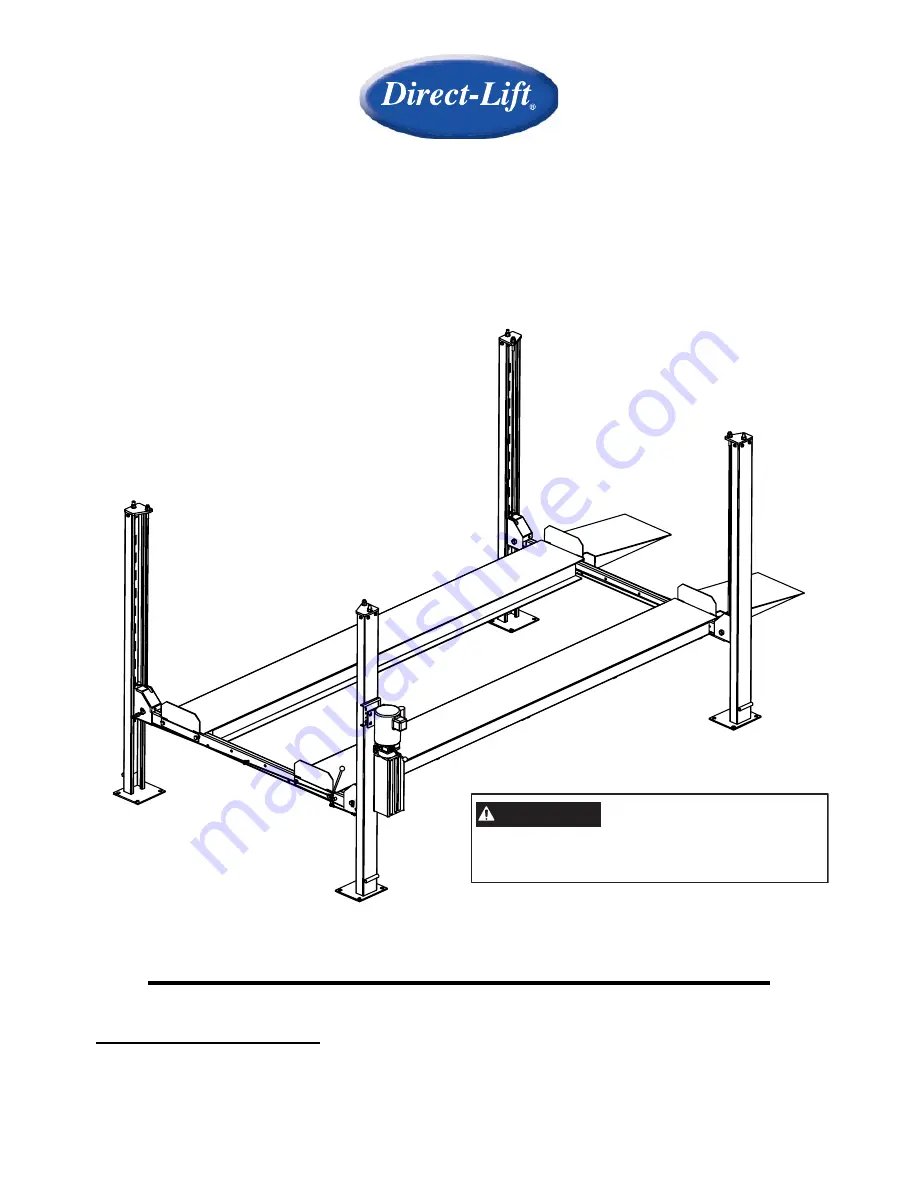
PP8 Plus
1
IN50001 Rev. C 04/30/2008
PP8 Plus
Four Post Lift
8,000 lbs. Capacity
(4,000 lbs. per axle)
Minimum wheelbase 100" at rated capacity
INSTALLATION / OWNERS MANUAL
Read this manual thoroughly
before installing, operating, or maintaining this lift. When done with
installation be sure to return documents to package and give all materials to lift owner/operator. When
installation is complete be sure to run lift up and down a few cycles with and without “typical” vehicle
loaded on lift.
IMPORTANT
Reference ANSI/ALI ALIS,
Safety Requirements for
Installation and Service of Automotive Lifts
before installing lift.