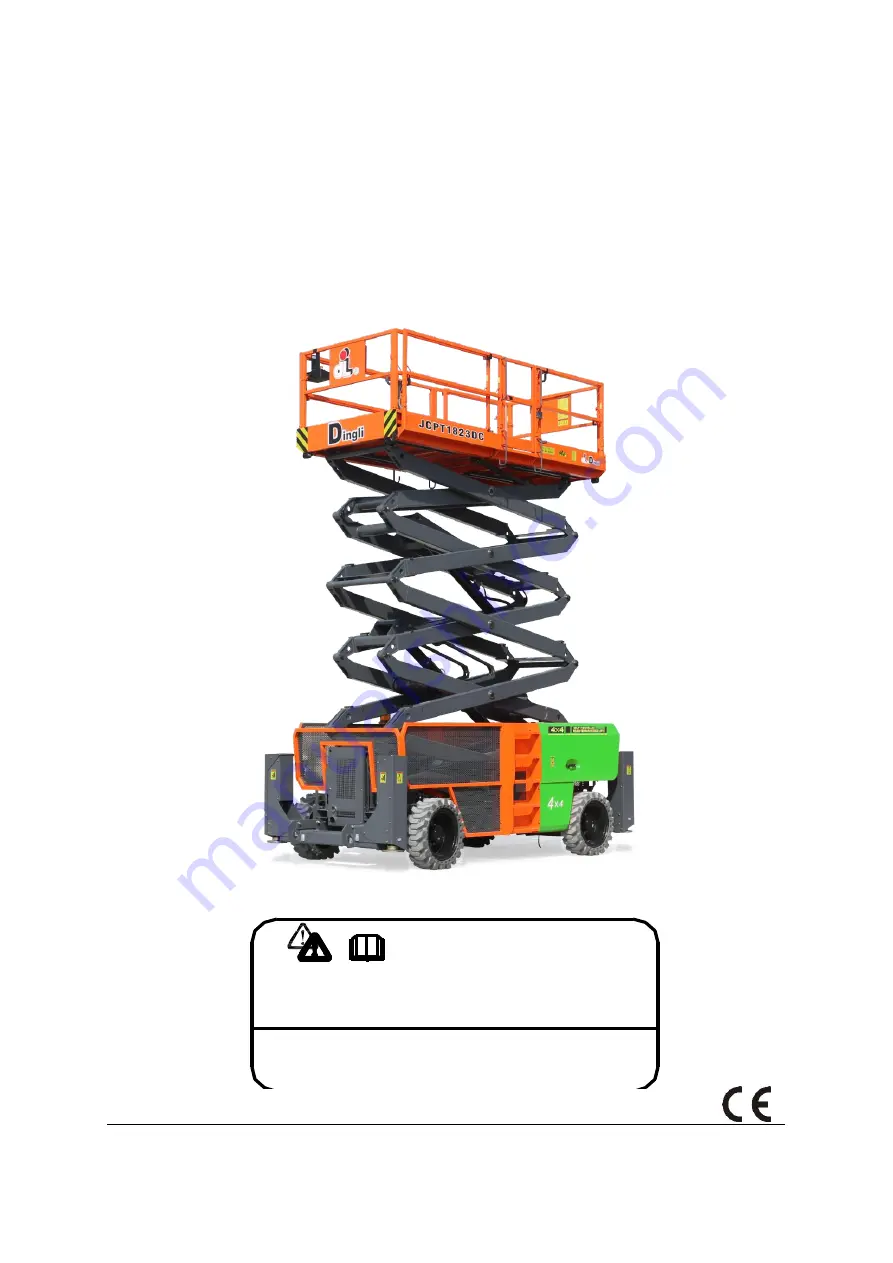
SELF-PROPELLED ROUGH-TERRAIN SCISSOR LIFTS
OPERATOR
’S MANUAL
with Maintenance Information
( For JCPT1523DC / JCPT1823DC )
Part Number: SM0121121_Rev1.0
Zhejiang Dingli Machinery Co., Ltd.
First Edition, April 2021
WARNING
THE MANUFACTURER SHALL NOT BE HELD LIABLE IN CASE OF FAULTS
OR ACCIDENTS DUE TO NEGLIGENCE, INCAPACITY, INSTALLATION BY
UNQUALIFIED TECHNICIANS AND IMPROPER USE OF THE MACHINE
DO NOT OPERATE THIS MACHINE UNTIL YOU READ AND UNDERSTAND
ALL THE DANGERS,WARNINGS AND CAUTIONS IN THIS MANUAL
Summary of Contents for JCPT1523DC
Page 3: ......
Page 5: ......
Page 17: ...OPERATOR S MANUAL with Maintenance Information Decals 12 ...
Page 18: ...OPERATOR S MANUAL with Maintenance Information Decals 13 ...