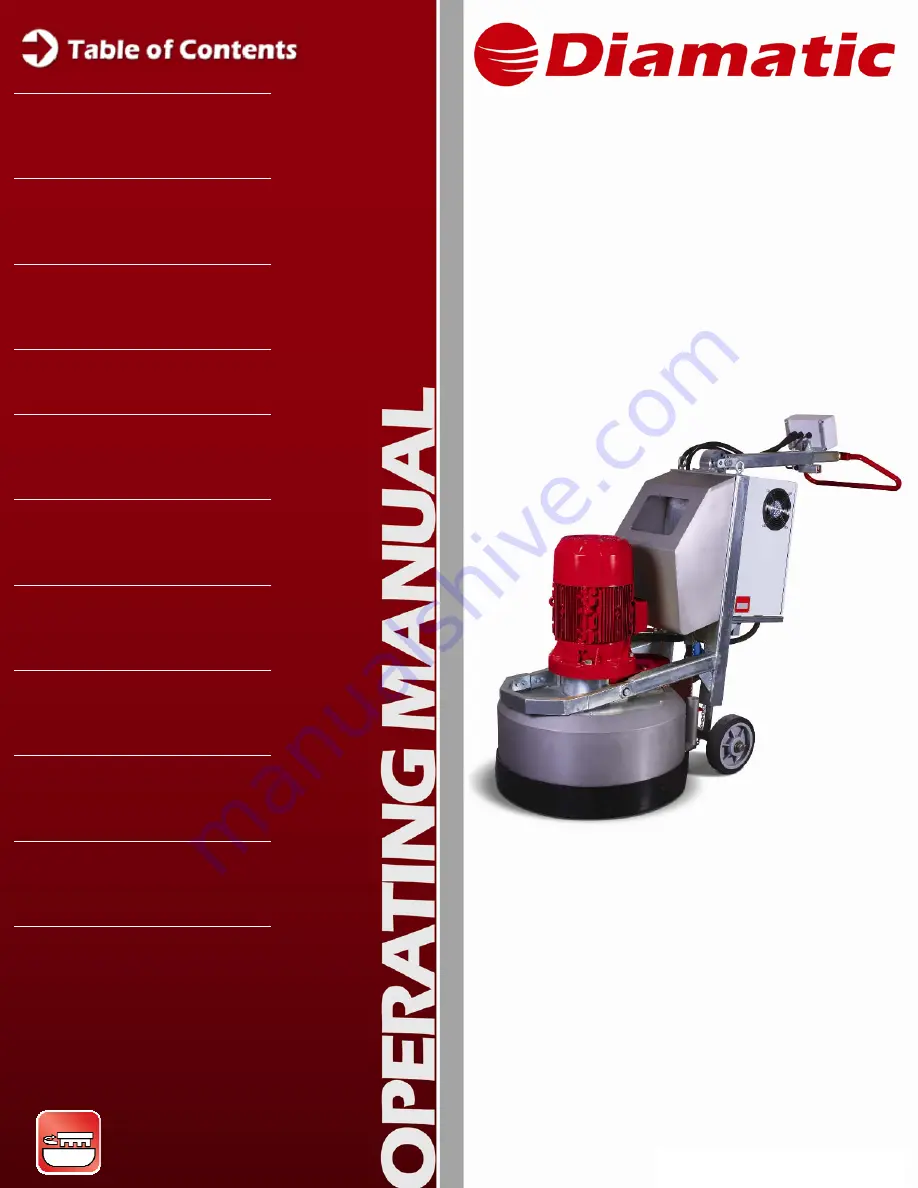
Grinding & Polishing
MODEL BMG-780 GRINDER
SECTION 2
SAFETY INSTRUCTIONS
1
OPERATING MANUAL
JANUARY 2008
Grinding & Polishing
MODEL
BMG-780
Planetary Grinder
Technical Data
1
Safety Instructions
2
General 3
Transport 4
Initial Operation
5
Operation 6
Maintenance 7
Electrical Systems
8
Fault Diagnosis
9
Spare Parts
10
Summary of Contents for BMG-780 ULTRAPRO
Page 32: ......