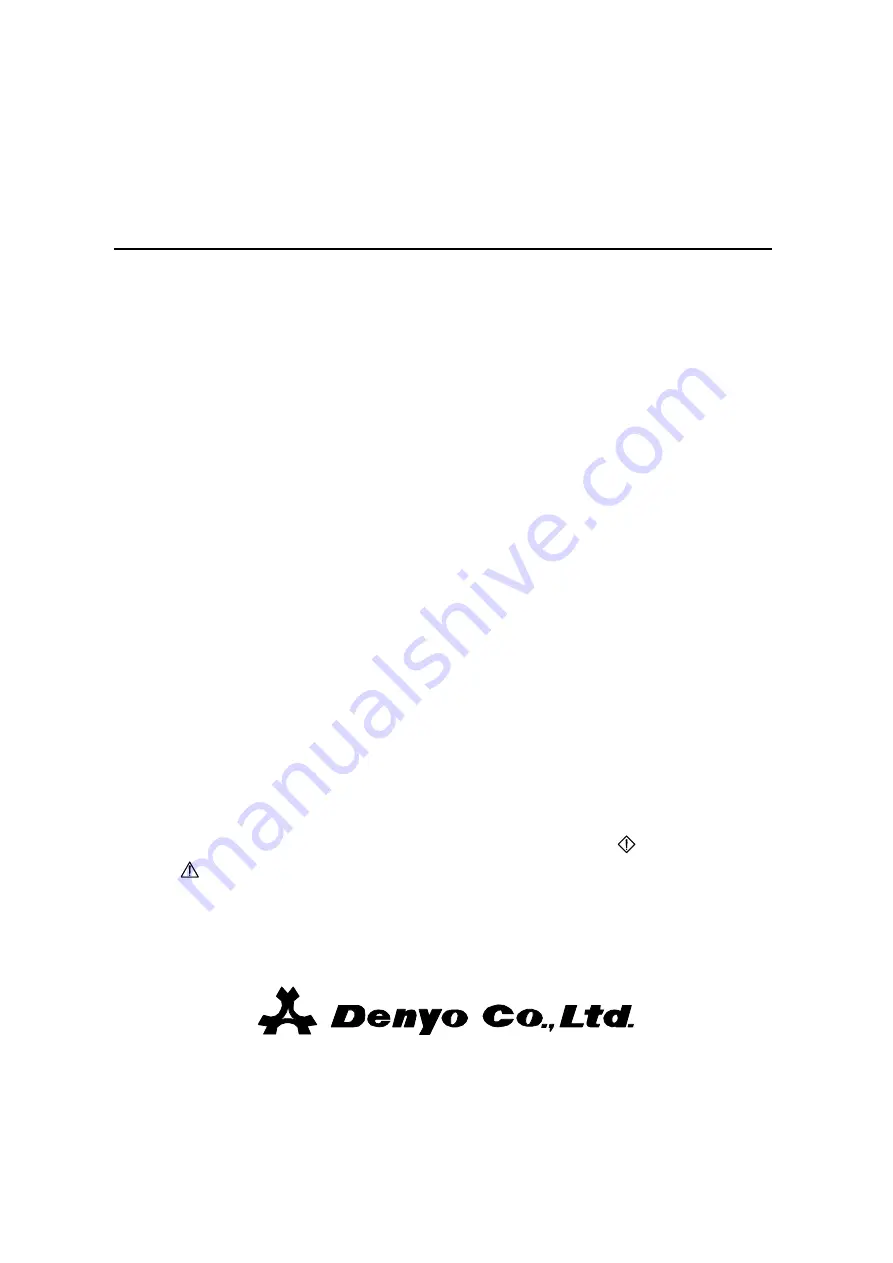
No. E48402 00204C
INSTRUCTION
INSTRUCTION
INSTRUCTION
INSTRUCTION
MANUAL
MANUAL
MANUAL
MANUAL
DENYO
DENYO
DENYO
DENYO
ENGINE
ENGINE
ENGINE
ENGINE
COMPRESSOR
COMPRESSOR
COMPRESSOR
COMPRESSOR
DIS-
DIS-
DIS-
DIS-390
390
390
390ES
ES
ES
ES
390
390
390
390ES-C
ES-C
ES-C
ES-C
390
390
390
390ES-D
ES-D
ES-D
ES-D
Before
using,
be
sure
to
read
this
manual
for
the
sake
of
safety.
Be
sure
to
observe
the
items
under
symbol
marks
"
WARNING
"
and
"
CAUTION
"
for
the
sake
of
safety.
Always
keep
this
manual
at
your
machine
for
the
sake
of
safety.
2-8-5,
Nihonbashi-horidomecho,
Chuo-ku,
Tokyo,
103-8566,
Japan
Summary of Contents for DIS-390ES
Page 58: ...55 10 2 Outline drawing DIS 390ES...
Page 59: ...56 DIS 390ES trailer type...
Page 60: ...57 DIS 390ES C...
Page 61: ...58 DIS 390ES C trailer type...
Page 62: ...59 DIS 390ES D...
Page 63: ...60 DIS 390ES D trailer type...
Page 64: ...61 10 3 Combined Piping Diagram DIS 390ES...
Page 65: ...62 DIS 390ES C...
Page 66: ...63 DIS 390ES D...
Page 67: ...64 10 4 Engine wiring diagram...