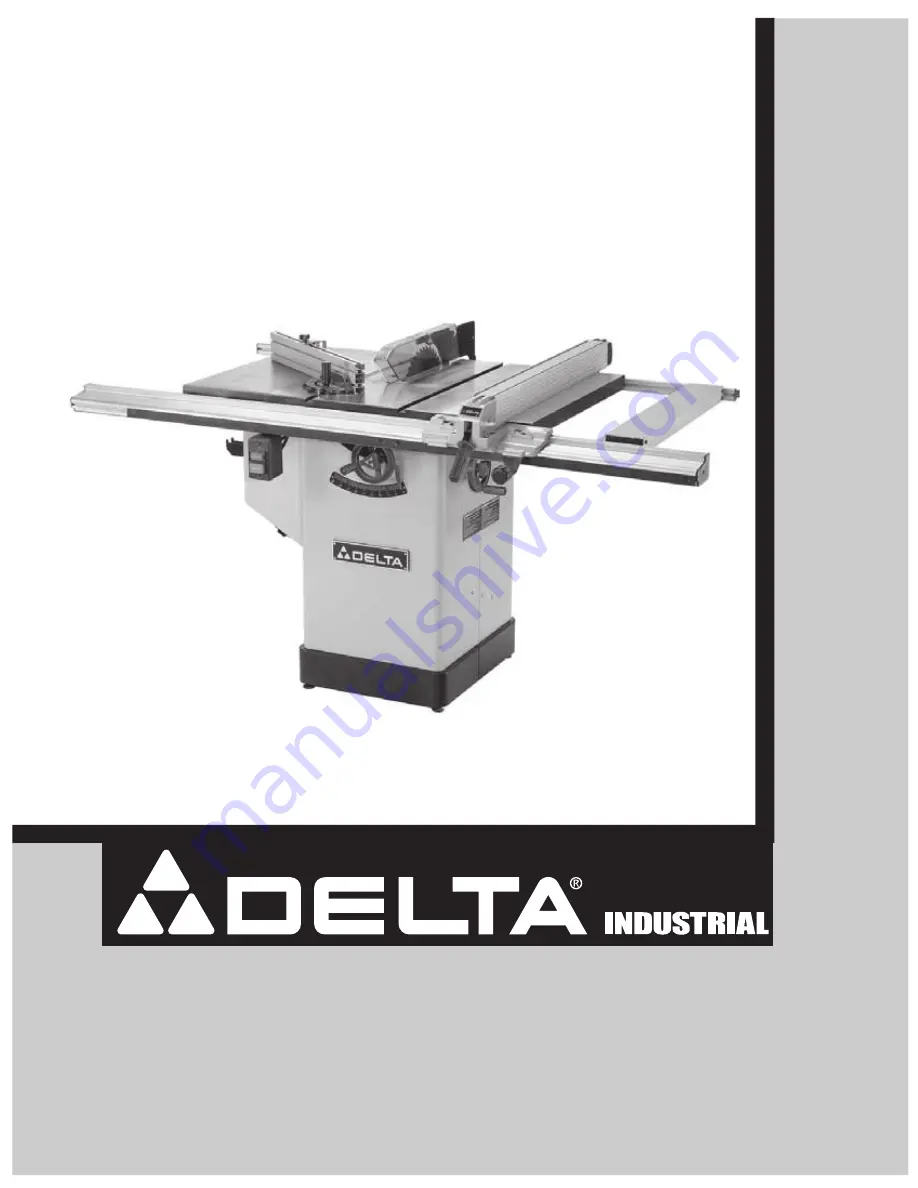
To learn more about
DELTA MACHINERY
visit our website at:
www.deltamachinery.com.
For Parts, Service, Warranty or other Assistance,
please call
1-800-223-7278
(
In Canada call
1-800-463-3582
).
Part No. 1238007
Copyright © 2003 Delta Machinery
Dated 11-01-03
I
N
S
TR
U
C
TI
O
N
MA
N
U
A
L
10” Tilting Arbour Saw
(Model 36-655)