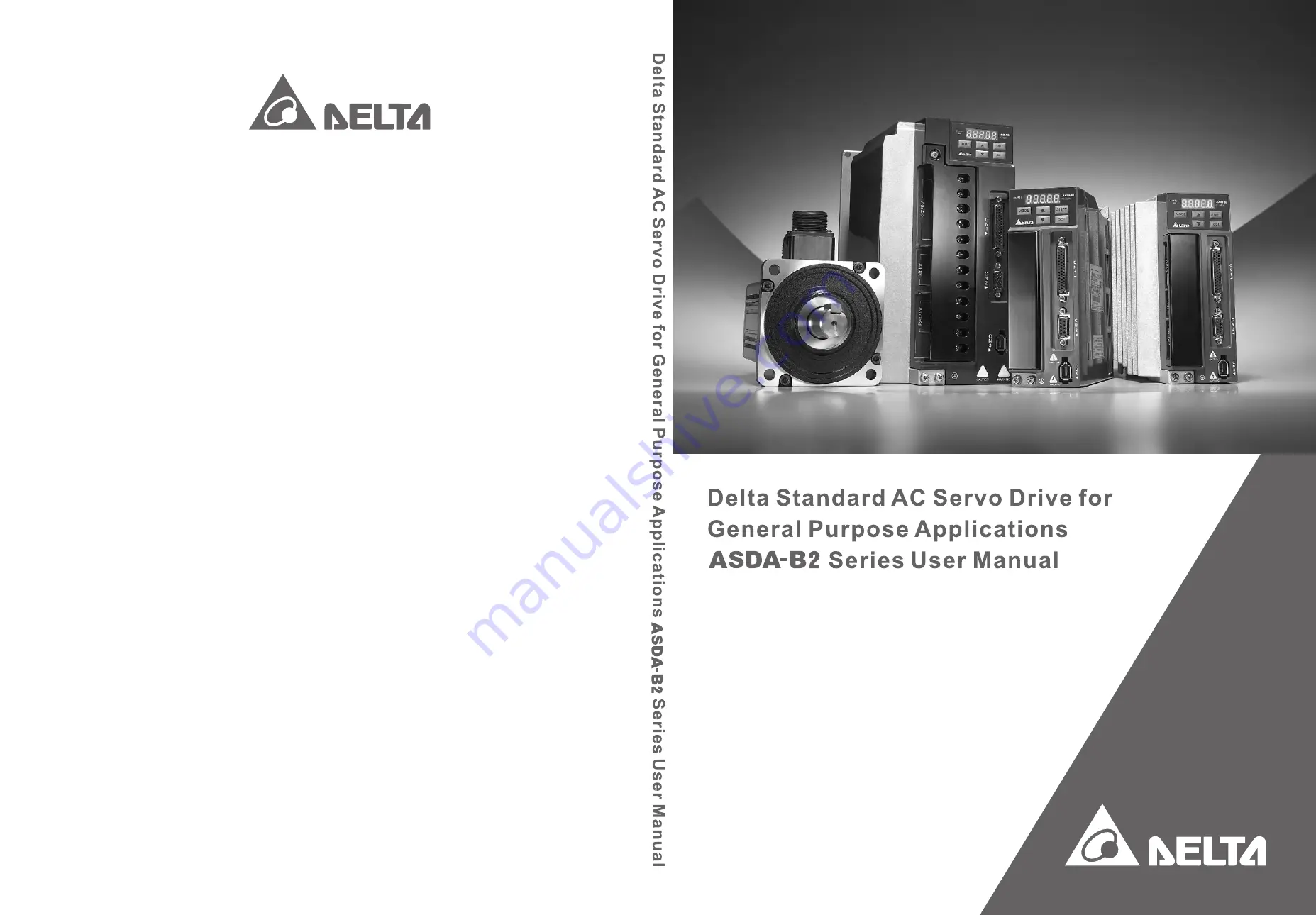
VARITEL INGENIERIA ELECTRONICA S.A.
[email protected] - www.varitel.com - Tel. (54) 11-4243-1171 / Fax: (54) 11-4292-7545
Manuel Baliña 456, Lomas de Zamora (B1832CCJ) Buenos Aires, Argentina.
Version: V1.0
DELTA_ASDA-B2_M_EN_20130906
VARITEL INGENIERIA ELECTRONICA S.A.
[email protected] - www.varitel.com - Tel. (54) 11-4243-1171 / Fax: (54) 11-4292-7545
Manuel Baliña 456, Lomas de Zamora (B1832CCJ) Buenos Aires, Argentina.
Version: V1.0
DELTA_ASDA-B2_M_EN_20130906