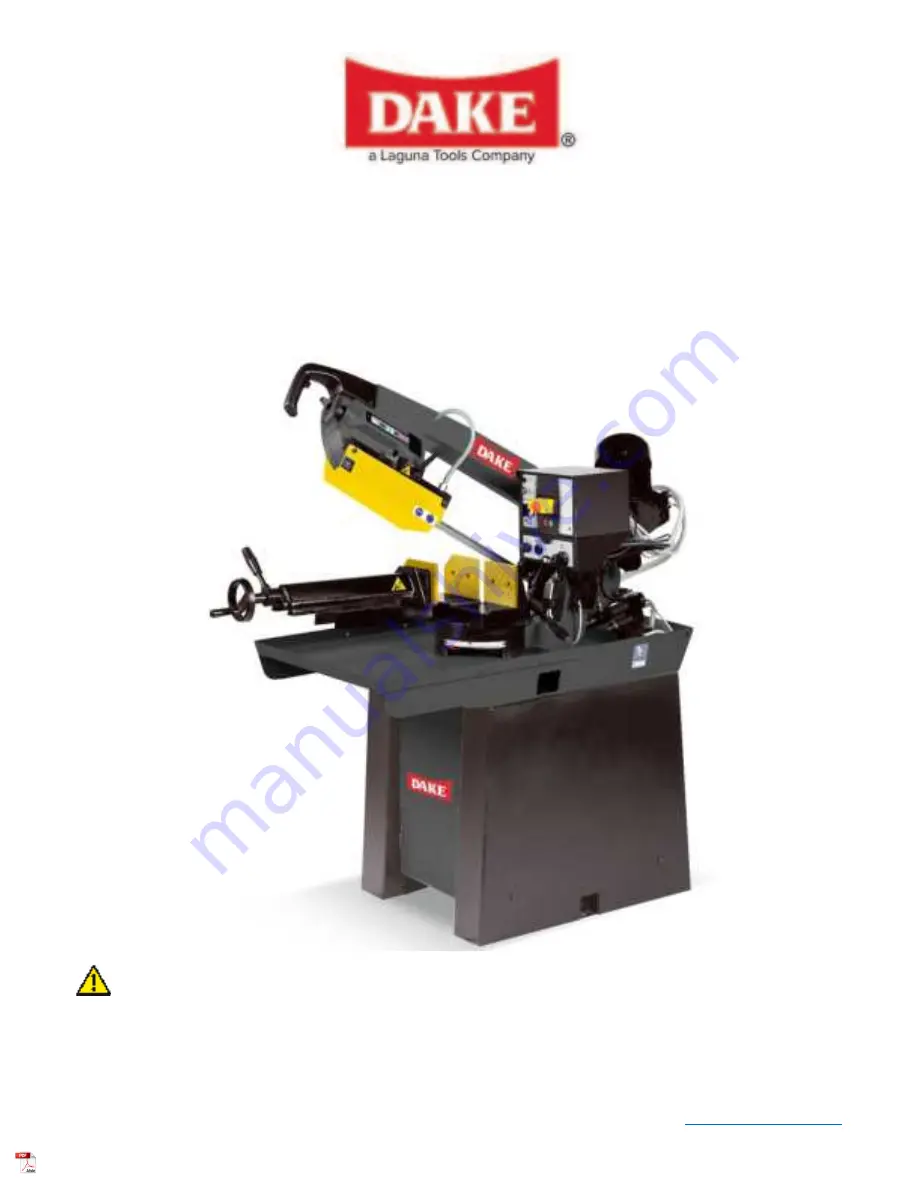
Dake Corporation
Phone: 800.937.3253
www.dakecorp.com
1809 Industrial Park Dr
Fax: 800.846.3253
Grand Haven, MI 49417
DAKE SEMI-AUTO MITERING BANDSAW
SE-8.5M
INSTRUCTIONAL MANUAL
WARNING!
Read and understand all instructions and responsibilities before operating. Failure to follow
safety instructions and labels could result in serious injury.