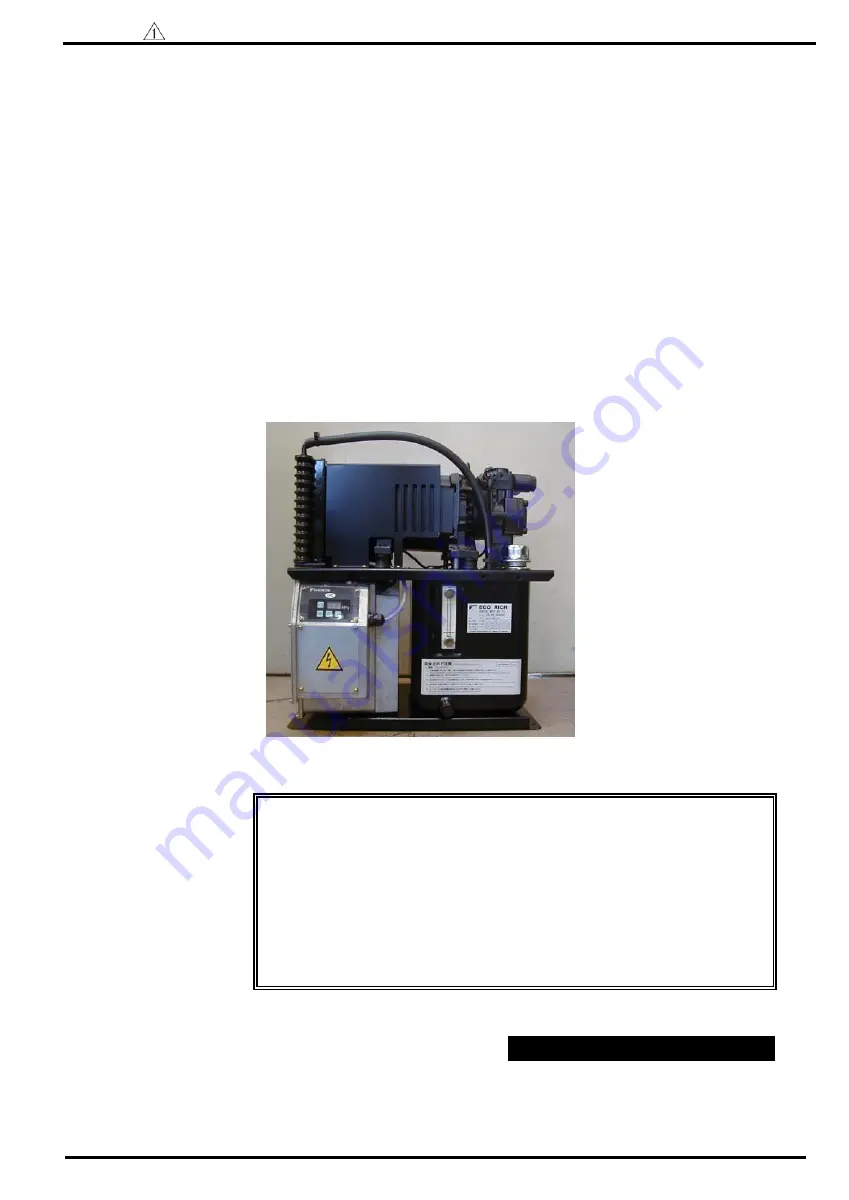
【INSTRUCTION MANUAL】
DAIKIN INDUSTRIES, LTD
.
SE-04430
Hybrid Hydraulic System
“ECO RICH”
EHU SERIES
Instruction Manual
DAIKIN INDUSTRIES, LTD.
Oil Hydraulics Division
《Photo: EHU25-M07-AE-30》
・
This instruction manual is based on these following types Eco Rich.
As for MGF.NO. before them, there is some difference in operating manual of
the panel and adjusting method.
□
EHU14-L04 -A -30
:
MFG.NO.
3C-
**
-
*****
□
EHU25-L04 -A -30
:
MFG.NO. 3C-
**
-
*****
□
EHU25-L07 -AE -30
:
MFG.NO. 3D-
**
-
*****
□
EHU25-M07-AE -30
:
MFG.NO. 3D-
**
-
*****
□
EHU30-M07-AE -30
:
MFG.NO. 3D-
**
-
*****
1