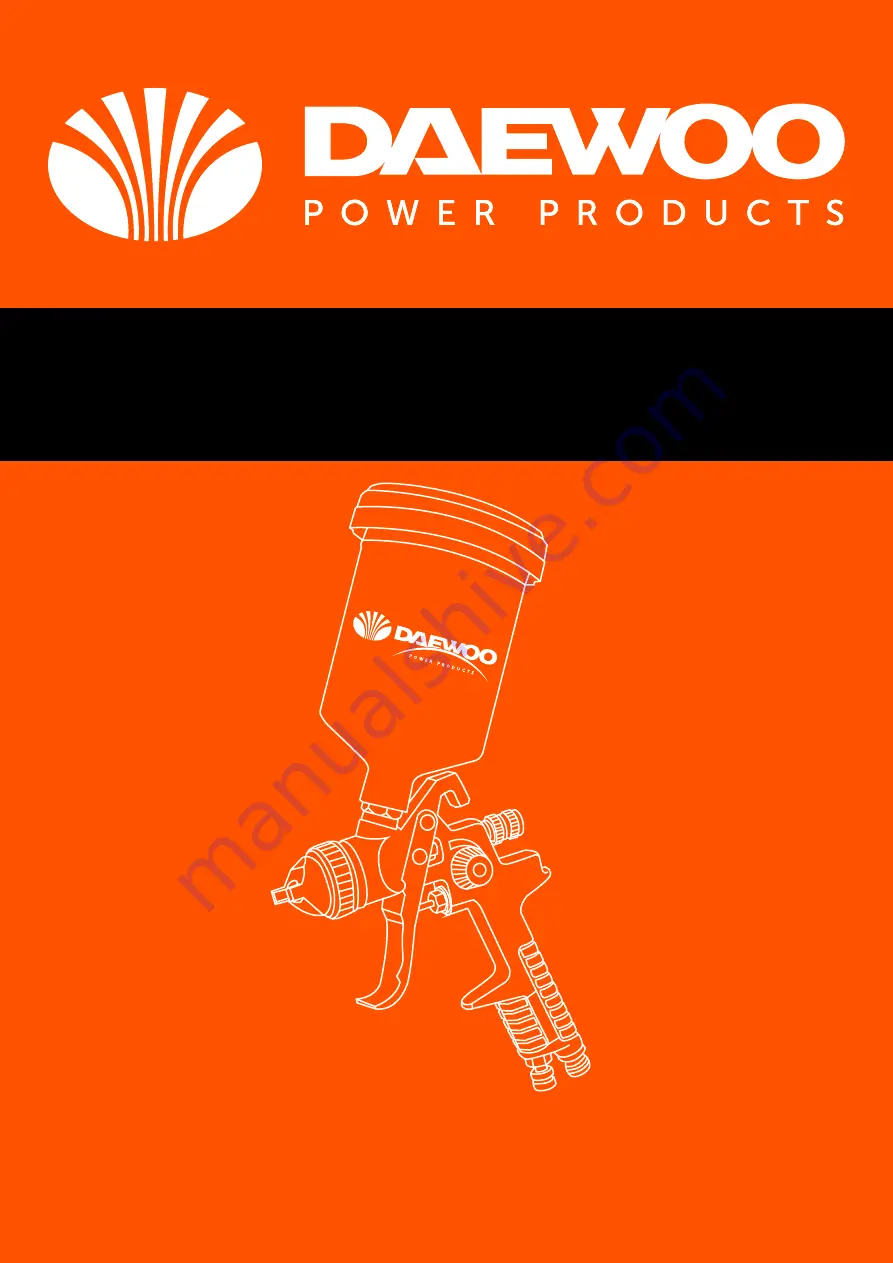
Manufactured under license of
Daewoo International Corporation
, Korea
www.daewoopowerproducts.com
USER'S MANUAL
DASP
600L
Spray Gun
Keep this manual for the safety warnings and precautions, assembly, operating, inspection, mainte-
nance and cleaning procedures.
NOTICE
Clean the Spray Gun IMMEDIATELY after EVERY use, in between coats, and when it will be idle for
more than 5 minutes.
Delayed or inadequate cleaning will permanently clog the Spray Gun.
WARNING
Read this material before using this product. Failure to do so can result in serious injury. SAVE THIS
MANUAL.
1. WARNING SYMBOLS AND DEFINITIONS
2. IMPORTANT SAFETY INSTRUCTIONS
INSTRUCTIONS PERTAINING TO A RISK OF FIRE, ELECTRIC SHOCK, OR INJURY TO PERSONS
The warnings and precautions discussed in this manual cannot cover all possible conditions and
situations that may occur. It must be understood by the operator that common sense and caution
are factors which cannot be built into this product, but must be supplied by the operator.
WARNING – When using tools, basic precautions should always be followed, including the following:
Work Area
a. Keep the work area clean and well lighted. Cluttered benches and dark areas increase the risks of
electric shock, fire, and injury to persons.
b. Keep bystanders, children, and visitors away while operating the tool. Distractions are able to
result in the loss of control of the tool.
3. Using two hands, one to steady the Cup and the other to operate the Spray Gun, aim Nozzle at
the workpiece.
CAUTION! DO NOT STOP WHEN SPRAYING. Spraying materials will start to set and dry
as soon as they come in contact with the air. They will cause a permanent clog if not cleared imme-
diately. If discontinuing spraying for more than half an hour, turn off the air supply, disconnect Cup
from Gun Body and thoroughly rinse Cup and Gun Body with fresh, clean water.
4. Pull Trigger slowly and move Spray Gun in parallel strokes to the workpiece. Keep the distance
from the workpiece at about 6 to 9 , depending on the flow adjustment and the paint.
5. To avoid paint build up, start moving the Spray Gun before squeezing the Trigger.
When finished with the stroke, release the Trigger while still moving the Spray Gun - see Figure O.
Doing this will produce a smoother finish. Do not stop moving the Spray Gun while spraying. If the
Spray Gun stops even briefly while spraying the paint will build up and run down the workpiece.
Note: The stroke speed, the Fluid Knob adjustment, and the distance from the workpiece, will deter-
mine how much paint is being applied. Apply two thin coats rather than one thick coat.
CAUTION! Air hose fittings may get hot. Allow fittings to cool before disconnecting, or wear gloves
to prevent burns.
6. To prevent accidents, release trigger, detach air supply, safely discharge any residual air pressu-
re, and again release trigger after use.
7. Clean the Spray Gun IMMEDIATELY after EVERY use, in between coats, and when it will be idle for
more than 5 minutes.
CLEANING
a. Follow solvent manufacturer’s clean up instructions and safety precautions.
b. Flush Spray Gun a full hose length from air compressor.
c. If collecting flushed solvents in metal container, transfer to nonmetal container, and flush metal
container.
d. Work far away from any ignition sources in a vapor free area.
e. Keep class ABC fire extinguisher nearby.
Solvent Selection:
Follow the paint and solvent manufacturer’s recommendations for cleaning, solvent type, and dispo-
sal.
IMPORTANT: Do not use mineral spirits with latex paints, doing so will make the paint very difficult
to remove
After Every Use:
1. Use solvent recommended by paint manufacturer.
2. Remove the Cup, along with any tubes or filters. Carefully scrape paint out of Cup. Dispose of
excess paint properly, then clean Cup and accessories with solvent.
3. Reduce air pressure to minimum, then fill the Cup with solvent and spray it through the Spray Gun
into the spent solvent container, while shaking the Spray Gun. Once the Cup is empty, repeat the
process until the solvent comes out clean.
4. Disconnect from the air source.
5. After disconnecting, point the Spray Gun into the spent solvent container and squeeze the Trigger
again to make sure no air remains.
Note: Do not immerse Spray Gun Body in solvent. Do not allow solvent to enter the air inlet.
6. Remove Nozzle by hand and soak it in solvent until it is clean. Use brush and toothpicks (sold
separately) to remove any paint.
Note: To prevent damage to the passages, do not use metal objects to clean the Nozzle.
7. Wipe down Spray Gun Body with a clean cloth and solvent.
8. Make sure all parts are free from residual paint.
9. If switching from oil-based to latex paint, after cleaning with solvent, clean all parts with warm
soapy water.
10. Rinse with warm water, then thoroughly blow dry all parts with compressed air.
11. Reassemble Spray Gun.
12. Use spray gun lubricant (sold separately) on EXTERNAL moving parts. (See Figure P)
NOTICE: Do not use any kind of lubricant in air supply or air inlet. The lubricant will mix with paint,
causing poor results.
Spent Solvent Disposal:
After cleaning, dispose of spent solvent according to the solvent manufacturer’s directions and local
hazardous waste standards.
11. USER-MAINTENANCE INSTRUCTIONS
Procedures not specifically explained in this manual must be performed only by a qualified
technician.
WARNING
TO PREVENT SERIOUS INJURY:
Detach the air supply and safely discharge any residual air pressure in the tool
before performing any inspection, maintenance, or cleaning procedures.
TO PREVENT SERIOUS INJURY FROM TOOL FAILURE: Do not use damaged equipment.
If abnormal noise, vibration, or leaking air occurs, have the problem corrected before further use.
Inspection:
Note: These procedures are in addition to the regular checks and maintenance explained as part of
the regular operation of the air-operated tool.
BEFORE EACH USE, inspect the general condition of the tool. Check for:
• loose screws,
• misalignment or binding of moving parts,
• clogged nozzle or fluid tip,
• damaged air supply hose,
• cracked or broken parts, and
• any other condition that may affect its safe operation.
Air Supply Maintenance:
Every day, perform maintenance on the air supply according to the component manufacturers’
instructions.
STORAGE
Store in a dry, secure area out of reach of children.
TROUBLESHOOTING - SPRAY PATTERN DIAGNOSIS
Note: The drawings on the left below resemble symptoms of spray pattern problems. Refer to the
accompanying possible causes and likely solutions to the right.
GENERAL TROUBLESHOOTING CHART
12. EXPLODED VIEW AND PART LIST
Turn Pattern Knob counterclockwise
(all the way open) to flatten the spray pattern. Turn it clockwise for a round spray pattern
- see Figure K: Pattern Adjustment.
Fan Direction:
16. To change the direction of the fan from horizontal to vertical, loosen the Lock Ring and turn the
Nozzle 90°.
17. After the adjustment, tighten the Lock Ring by hand.
SPRAYING TECHNIQUE
IMPORTANT: Proper spraying technique is ESSENTIAL to achieve good results.
1. First, clean and prepare the Spray Gun according to the instructions under Before First Use on
page 10 and Spray Gun Setup Adjustment on page 11.
2. Keep the Spray Gun upright and at a right angle to the workpiece - See Figure M and Figure N.
9. Turn the Fluid Knob clockwise until it reaches a natural stopping point.
10. Release the trigger.
11. Tighten Collar on Fluid Knob to lock fluid adjustment settings.
Air Adjustment:
12. Attach Spray Gun to spray gun regulator (sold separately). Use spray gun regulator to measure
airflow PSI.
13. Adjust the air supply pressure during operation with the Trigger fully depressed and the Air Knob
fully open. If reducing air pressure for specific areas, use the Air Knob.
14. To fine-tune airflow, turn Air Knob clockwise to lessen airflow pressure. Turn Air Knob counter-
clockwise to increase airflow pressure.
Pattern Adjustment:
15. Use the Pattern Knob to adjust the spray pattern.
SPRAY GUN SETUP ADJUSTMENT
WARNING
TO PREVENT SERIOUS INJURY: Do not adjust or tamper with any control or component in a way
not specifically explained within this manual. Improper adjustment can result in tool failure or other
serious hazards.
CAUTION! Keep hands away from Trigger while making adjustments.
1. Thread the Cup to the top of the Gun Body and tighten until the Cup is securely in place.
Note: This Spray Gun can be used for spraying oil-based or latex paints.
Paint Preparation and Filling:
Note: Proper paint mixture is essential. Follow the manufacturer’s directions. Most paints will spray
easily if they are thinned properly.
2. Thin the paint according to manufacturer’s directions and mix thoroughly.
3. Carefully strain the paint through a paint strainer or a piece of cheesecloth.
4. Fill the Cup to 3/4 full. Close Cup.
5. Start the air compressor and set the regulator to needed pressure.
Do not exceed maximum air pressure.
6. Test the consistency by spraying on a piece of scrap material.
If it still appears too thick, add a very small amount of thinner (not included) and mix thoroughly.
Use the proper thinner for the type of paint.
Thin CAUTIOUSLY. Proceed slowly, adding minimal amounts at a time. DO NOT exceed the manu-
facturer’s thinning recommendations.
Fluid Adjustment:
7. Loosen Collar on Fluid Knob. Turn the Fluid Knob counterclockwise until it is open enough to
show 3 or 4 threads.
8. Fully depress the Trigger.
Note: To prevent damage to the passages, do not use metal objects to clean the Nozzle and Fluid
Tip.
5. Clean inside of Spray Gun by pouring warm soapy water into the Fluid Inlet, then run a flexible
round brush (sold separately) through the passage between the Fluid Inlet and Nozzle opening.
6. Wipe down Spray Gun Body with a clean cloth and warm soapy water.
7. Rinse Cup, along with any tubes or filters, in warm soapy water.
8. Make sure all parts are free from grease and oil. Repeat cleaning if necessary.
9. Rinse all parts and inside of Spray Gun, except Air Inlet, with warm water.
10. Thoroughly blow dry all parts and inside of Spray Gun with compressed air.
11. Reassemble Spray Gun, making sure to retract Fluid Needle when replacing Fluid Tip.
FLUID TIP SELECTION
The choice of Fluid Tip Set will vary according to the consistency of the fluid being sprayed. Consult
paint manufacturer recommended spray tips and use Table A to select a Tip Set appropriate to the
job.
Note: Chart provided for reference only. Additional fluid tips sizes not included.
10. OPERATING INSTRUCTIONS
Inspect tool before use, looking for damaged, loose, and missing parts. If any problems are found,
do not use tool until repaired.
WORKPIECE AND WORK AREA SET UP
BEFORE FIRST USE
NOTICE: Before first use, clean the Spray Gun thoroughly.
If not removed, the material used for testing and corrosion prevention will contaminate paint.
1. Remove Nozzle by hand.
2. Depress Trigger to retract Fluid Needle, then remove Fluid Tip with spray gun wrench (sold sepa-
rately). Release Trigger.
Note: Do not bend Fluid Needle.
3. Remove Fluid Knob by hand, then remove Fluid Spring and Fluid Needle.
Note: Do not immerse Spray Gun Body in liquid. Do not allow liquid to enter the air inlet.
4. Place parts, other than Spray Gun Body, into container with warm soapy water. Allow to soak,
then scrub parts, using brushes and toothpicks from spray gun cleaning kit (sold separately).
4. The air hose must be long enough to reach the work area with enough extra length to allow free
movement while working.
5. Close the in-line shutoff valve between the compressor and the tool.
6. Turn on the air compressor according to the manufacturer’s directions and allow it to build up
pressure until it cycles off.
7. Open the in-line shutoff valve.
8. Adjust the air compressor’s output regulator so that the air output is enough to properly power
the tool, but the output will not exceed the tool’s maximum air pressure at any time. Adjust the
pressure gradually, while checking the air output gauge to set the right pressure range.
9. Inspect the air connections for leaks. Repair any leaks found.
10. If the tool will not be used at this time, turn off and detach the air supply and safely discharge
any residual air pressure to prevent accidental operation.
Note: Residual air pressure should not be present after the tool is disconnected from the air supply.
However, it is a good safety measure to attempt to discharge the tool in a safe fashion after discon-
necting to ensure that the tool is disconnected and unpowered.
Personal Safety
a. Stay alert. Watch what you are doing and use common sense when operating the tool. Do not
use the tool while tired or under the influence of drugs, alcohol, or medication. A moment of inatten-
tion while operating the tool increases the risk of injury to persons.
b. Dress properly. Do not wear loose clothing or jewelry. Contain long hair. Keep hair, clothing, and
gloves away from moving parts. Loose clothes, jewelry, or long hair increases the risk of injury to
persons as a result of being caught in moving parts.
c. Do not overreach. Keep proper footing and balance at all times. Proper footing and balance
enables better control of the tool in unexpected situations.
d.
e.
3. TOOL USE AND CARE
a. Do not force the tool. Use the correct tool for the application. The correct tool will do the job
better and safer at the rate for which the tool is designed.
b. Disconnect the tool from the air source before making any adjustments, changing accessories, or
storing the tool. Such preventive safety measures reduce the risk of starting the tool unintentionally.
Turn off and detach the air supply, safely discharge any residual air pressure, and release the thrott-
le and/or turn the switch to its off position before leaving the work area.
c. Store the tool when it is idle out of reach of children and other untrained persons.
A tool is dangerous in the hands of untrained users.
d. Check for misalignment or binding of moving parts, breakage of parts, and any other condition
that affects the tool’s operation. If damaged, have the tool serviced before using. Many accidents
are caused by poorly maintained tools. There is a risk of bursting if the tool is damaged.
e. Use only accessories that are identified by the manufacturer for the specific tool model. Use of
an accessory not intended for use with the specific tool model, increases the risk of injury to
persons.
4. SERVICE
a. Tool service must be performed only by qualified repair personnel.
b. When servicing a tool, use only identical replacement parts. Use only authorized parts.
c. Use only lubricants supplied with the tool or specified by the manufacturer.
5. AIR SOURCE
a. Never connect to an air source that is capable of exceeding 200 psi. Over pressurizing the tool
may cause bursting, abnormal operation, breakage of the tool or serious injury to persons. Use only
clean, dry, regulated compressed air at the rated pressure or within the rated pressure range as
marked on the tool. Always verify prior to using the tool that the air source has been adjusted to the
rated air pressure or within the rated air-pressure range.
b. Never use oxygen, carbon dioxide, combustible gases or any bottled gas as an air source for the
tool. Such gases are capable of explosion and serious injury to persons.
6. SYMBOL DEFINITIONS
7. SPECIFIC SAFETY INSTRUCTIONS
1. Do not direct spray at people or animals.
2. Do not exceed maximum air pressure.
3. Do not spray near open flames, pilot lights, stoves, heaters, the air compressor, or any other heat
source. Most solvents and coatings are highly flammable, particularly when sprayed. Maintain a
distance of at least 25 feet from the air compressor. If possible, locate the air compressor in a
separate room.
4. Read all of the information concerning coating products and cleaning solvents.
Do not use chlorinated solvents (e.g. 1-1-1 trichloroethylene and dichloromethane, also known as
methylene chloride) to clean spray guns. Many spray guns contain aluminum, which reacts strongly
to chlorinated solvents. Contact the solvent or coating manufacturer as needed regarding potential
chemical reactions.
5. RISK OF INJECTION - Do not point spray gun at any person or any part of the body. In case of
skin injection, seek medical attention immediately.
6. Industrial applications must follow OSHA requirements.
7. Spraying hazardous materials may result in serious injury or death. Do not spray pesticide, acid,
corrosive material, fertilizer, or toxic chemicals.
8. Paints and solvents may be harmful or fatal if swallowed or inhaled. Avoid prolonged skin contact
with solvents or paints as they will irritate skin. After any contact, immediately wash off exposed
area with hot, soapy water.
9. Attach all accessories properly to the tool before connecting the air supply. A loose accessory
may detach or break during operation.
10. Install an in-line shutoff valve to allow immediate control over the air supply in an emergency,
even if a hose is ruptured.
11. Air hose fittings may get hot during use. Allow fittings to cool before disconnecting.
8. SPECIFICATIONS
Max spraying pressure: 2.0 - 3.5 bar
Spray width: 160 - 260 mm
Consumption: 6 CFM
Tank capacity: 600 ml
Nozzle diameter: 1.4 mm
9. INITIAL SET UP
Read the ENTIRE IMPORTANT SAFETY INFORMATION section at the beginning of this manual
including all text under subheadings therein before set up or use of this product.
Note: For additional information regarding the parts listed in the following pages, refer to the
Assembly Diagram near the end of this manual.
BEFORE SETUP
This air tool may be shipped with a protective plug covering the air inlet. Remove this plug before
set up.
AIR SUPPLY SETUP
WARNING
1. Incorporate a filter, regulator with pressure gauge, in-line shutoff valve, and quick coupler for best
service, as shown on Figure A on page 7 and Figure B on page 8. An in-line shutoff ball valve is an
important safety device because it controls the air supply even if the air hose is ruptured. The
shutoff valve should be a ball valve because it can be closed quickly.
Note: Do not use an automatic oiler system or add oil to airline. The oil will contaminate the mate-
rial being propelled, ruining the final result.
2. Attach an air hose to the compressor’s air outlet.
3. Connect the air hose to the air inlet of the tool. Other components, such as a coupler plug and
quick coupler, will make operation more efficient, but are not required.
WARNING! TO PREVENT SERIOUS INJURY FROM ACCIDENTAL OPERATION:
Do not install a female quick coupler on the tool. Such a coupler contains an air valve that will
allow the air tool to retain pressure and operate accidentally after the air supply is disconnected.
Note: Air flow, and therefore tool performance, can be hindered by undersized air supply compo-
nents.