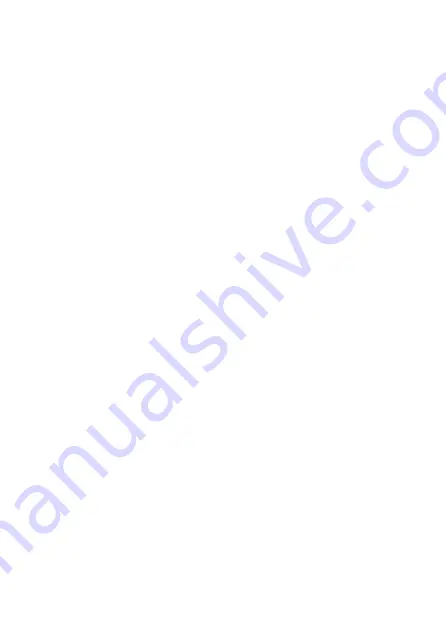
1
Preface
Thank you for purchasing CRAFTSMAN G10 Series frequency inverter made by
Guangxi Craftsman Electrical Technology Co.,Ltd.
G10 series inverter is a universal mini multi-function frequency converter. It adopts open-
loop vector and V/F control mode. It can realize asynchronous motor control with high-
performance current vector control technology. The power range covers 0.75kW~4kW.
Stable, reliable and easy to use are important features.
The company reserves the right to continuously improve the product without prior notice.
For the latest changes and more, please visit:
www.gxcraftsman.com