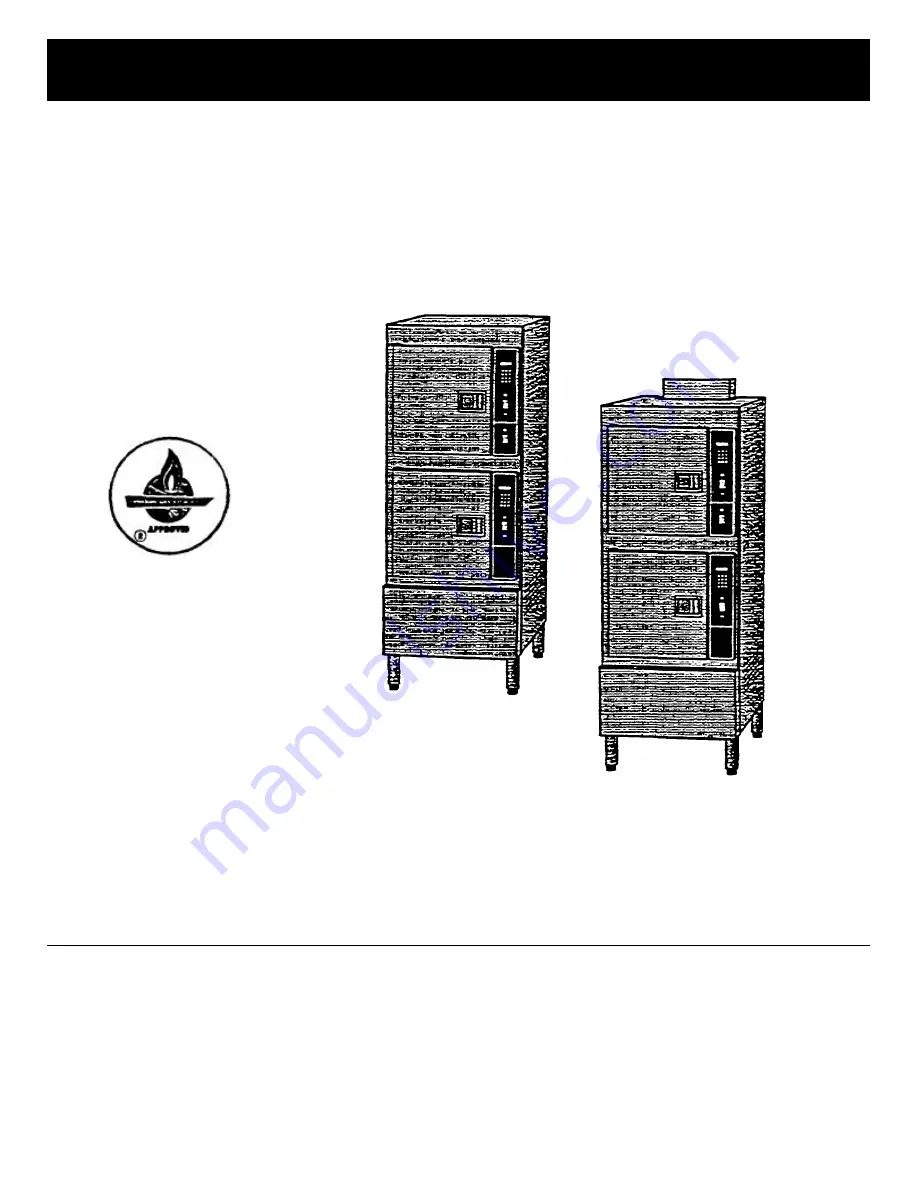
Cleveland Range
SteamCraft 10
®
Convection Steamer
MODELS: 24-CEA-10, & 24-CGA-10
Cleveland Range, Inc.
SERVICE
MANUAL
Printed 3/93
UNITED STATES
1333 East 179th St.. Cleveland, Ohio 44110 Phone: (216) 451-4900 •
Telex: 98-0546 • FAX: (216) 481-3782
CANADA
Garland Commercial
Ranges
1177 Kamato Road
Mississaugha, Ontario. Canada L4W1X4
Phone: (416) 624-0260 - FAX: (416) 624-0623