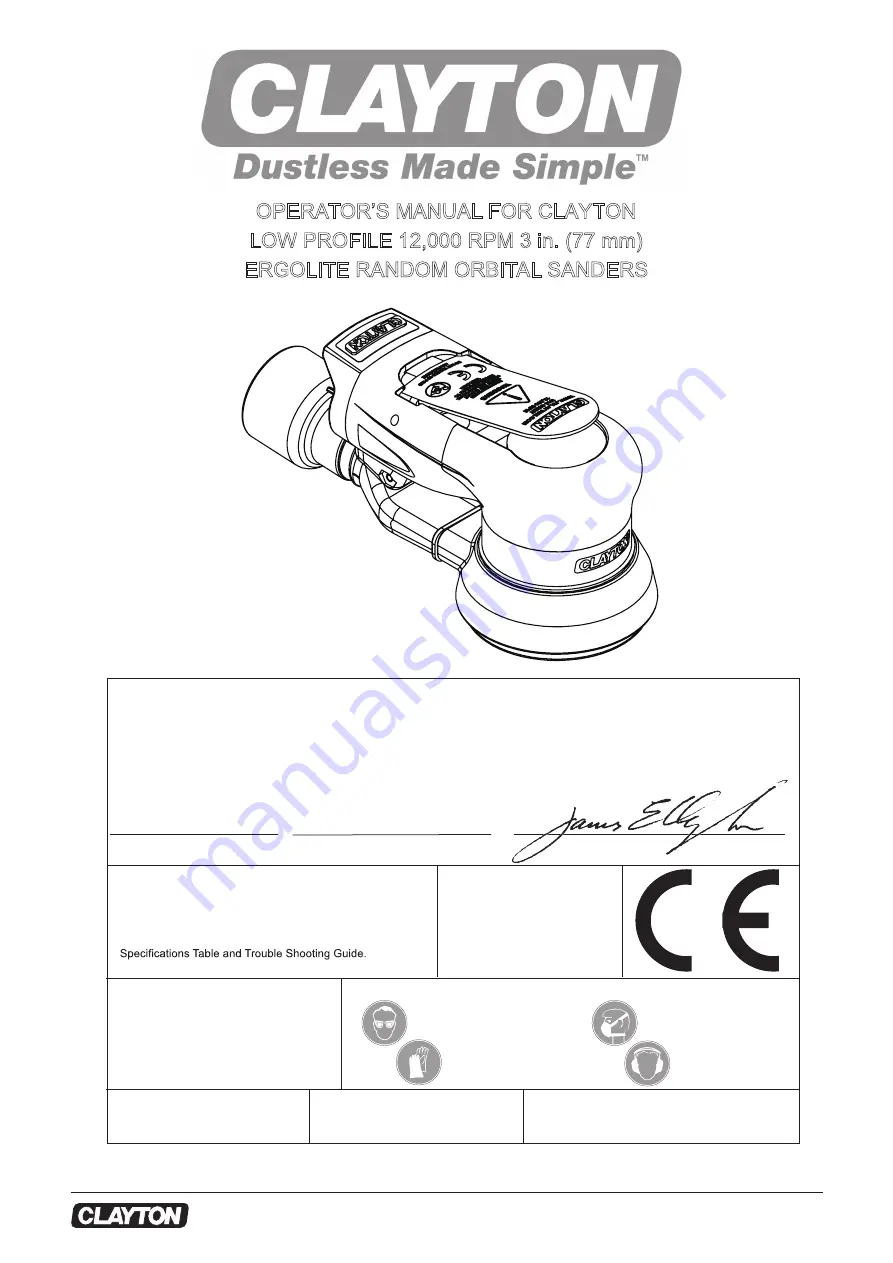
OPERATOR’S MANUAL FOR CLAYTON
LOW PROFILE 12,000 RPM 3 in. (77 mm)
ERGOLITE RANDOM ORBITAL SANDERS
Operator Instructions
Includes –Parts Page, Parts List, Please Read and Comply,
Proper Use of Tool, Work Stations, Putting the Tool Into Ser-
vice, Operating Instructions and Compressor Layout, Service
Tools and Accessories, Service Instructions, Back-Up Pads,
Declaration of Conformity
CLAYTON Associates, Inc. 1650 Oak Street Lakewood, NJ 08701 USA
declare on our sole responsibility that the products
Place and date of issue
Name
Signature or equivalent marking of authorized person
Important
Read these instructions care-
fully before installing, operating,
servicing or repairing this tool.
Keep these instructions in a safe
accessible location.
Manufacturer/Supplier
Required Personal Safety Equipment
Recommended Airline
Size - Minimum
3/8 in
10 mm
Recommended Maximum
Hose Length
25 feet
8 meters
Air Pressure
Maximum Working Pressure 90 psig 6.2 bar
Recommended Minimum
NA
NA
Breathing Masks
Ear Protection
Safety Glasses
Safety Gloves
Lakewood, NJ 2019-04
James E. CLAYTON
CLAYTON Associates, Inc.
TEL (732) 363-2100
www.VacuumSanding.com
3 in. (77 mm) Ergolite Random Orbital Sanders (See Product “Specifications” Table for particular Model) to which this declaration
relates is in conformity with the following standard(s) or other normative document(s) EN ISO 15744:2008. Following the provisions
of 89/392/EEC as amended by 91/368/EEC, 93/44/EEC & 93/68/EEC Directives and consolidating Directive 2006/42/EC
1
Copyright © 1984-2016 CLAYTON Associates, Inc.
(732) 363-2100 • ww
w.VacuumSanding.com
B-X3CT30-8
Revision 2019-05
Summary of Contents for 770-12300J
Page 13: ......