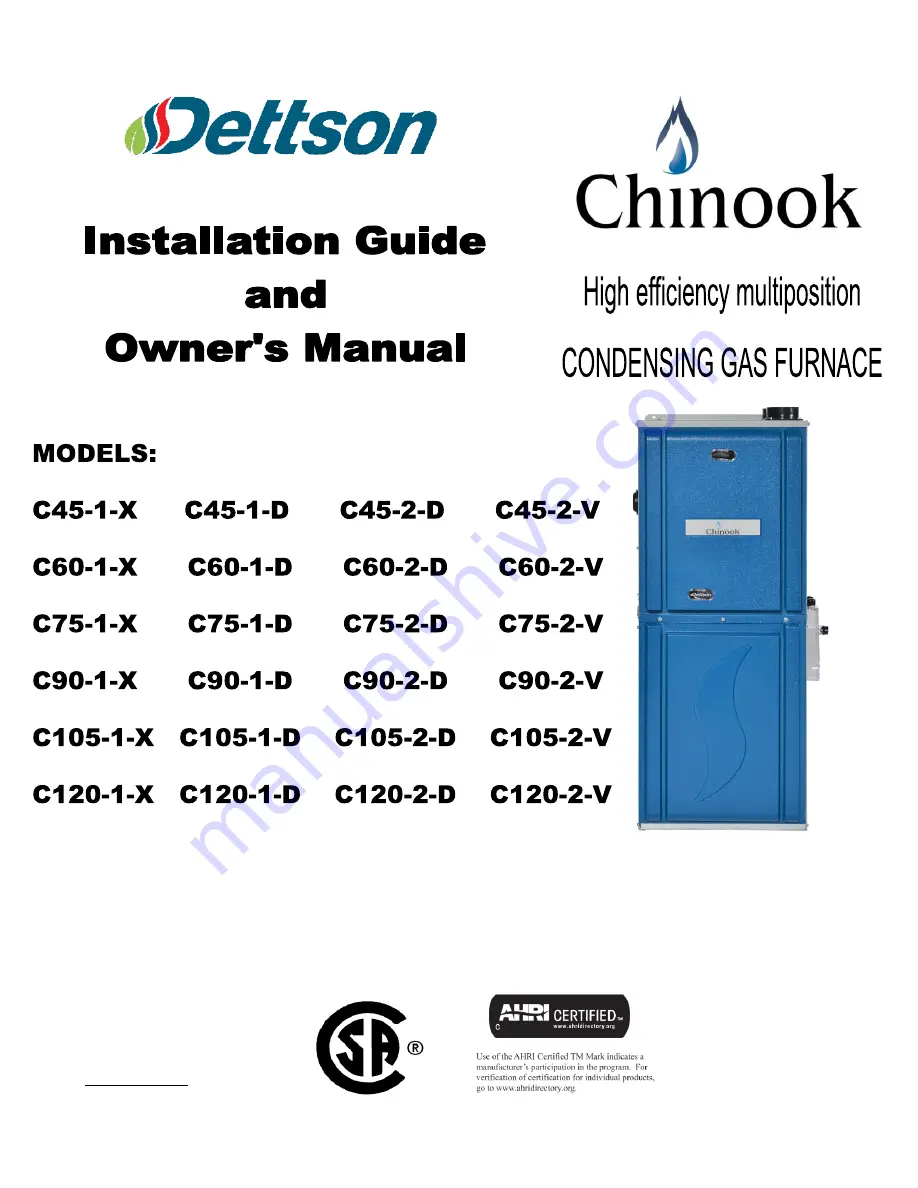
2016-01-29
X40223 rev. K
ATTENTION:
Do not tamper with the unit or its controls. Call a qualified service technician.
INSTALLER / SERVICE TECHNICIAN:
Use the information in this manual for the installation / servicing of the furnace and
keep the document near the unit for future reference.
These instructions must be read and understood completely before attempting installation.
HOMEOWNER:
PLEASE Keep this manual nears the furnace for future reference.
Manufactured by:
Industries Dettson Inc.
Sherbrooke (Québec) Canada
www.dettson.com
c
us
Summary of Contents for c105-1-d
Page 20: ...20 Figure 16 Wiring diagram One stage PSC ...
Page 21: ...21 Figure 17 Two Stage PSC Furnace Control ...
Page 22: ...22 Figure 18 Two Stage ECM Furnace Control ...
Page 26: ...26 Figure 21 Direct venting Figure 22 Multi venting ...
Page 37: ...37 Figure 25 Part list 1 Stage PSC ...
Page 38: ...38 Figure 26 Part list 1 Stage PSC continued ...
Page 41: ...41 Figure 27 Part list 2 Stage PSC ...
Page 42: ...42 Figure 28 Part list 2 stage PCS continued ...
Page 45: ...45 Figure 29 Part list X13 ...
Page 46: ...46 Figure 30 Part list X13 continued ...
Page 49: ...49 Figure 31 Part list 2 Stage ECM ...
Page 50: ...50 Figure 32 Part list 2 Stage ECM continued ...