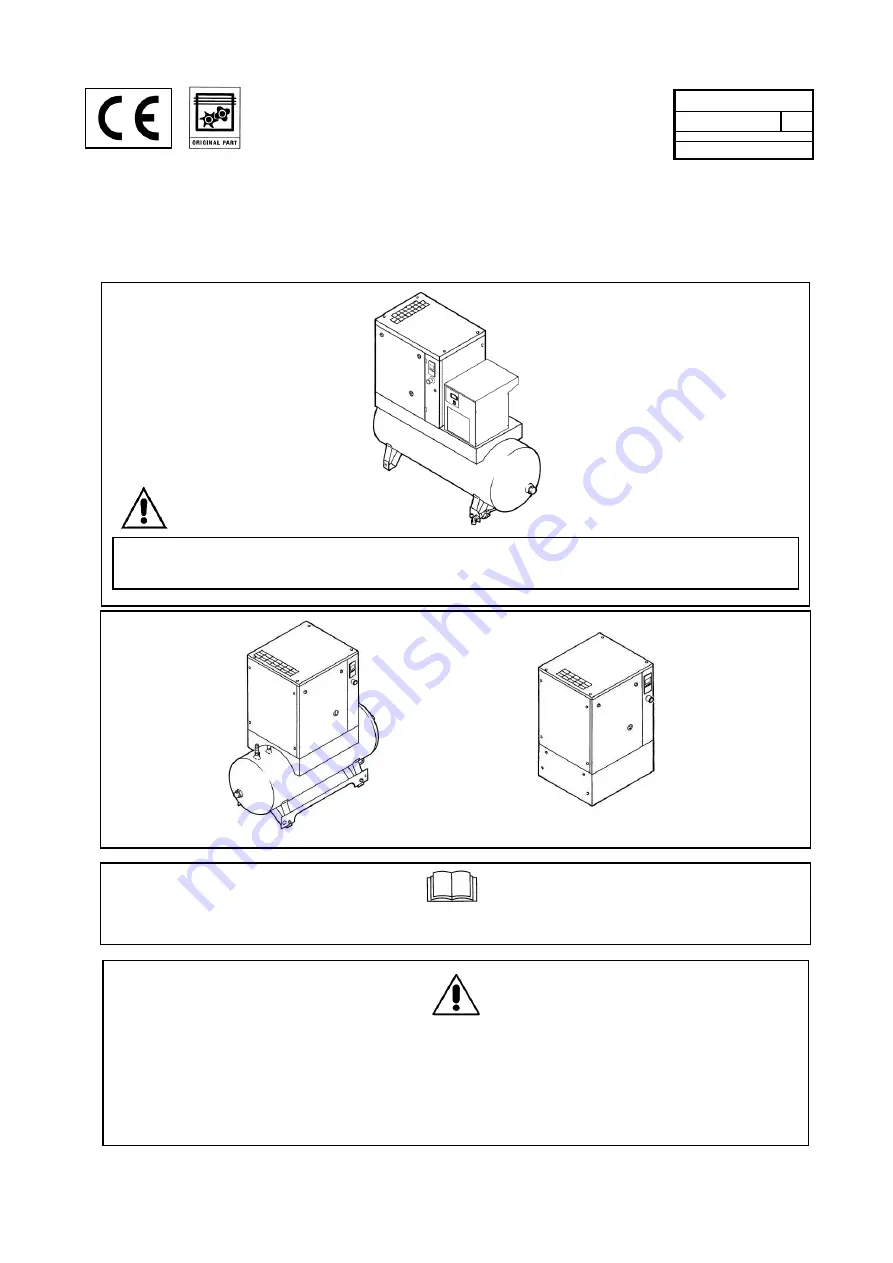
9828093379 ed 00 05/2020 1
INSTRUCTION AND MAINTENANCE MANUAL
SILENCED SCREW ROTARY COMPRESSOR UNITS
HP 3 - 4 - 5,5 - 7,5 - 10
KW 2,2 - 3 - 4 - 5,5 - 7,5
Code
9828093379 00
Edition 05/2020
READ THIS MANUAL CAREFULLY BEFORE CARRYING OUT ANY OPERATIONS ON THE COMPRESSOR
UNIT.
THIS MACHINE MUST BE CONNECTED TO TWO DIFFERENT POWER SUPPLIES: THREE-PHASE OR SINGLE-
PHASE SUPPLY FOR THE COMPRESSOR AND SINGLE-PHASE SUPPLY FOR THE DRYER
THIS MACHINE IS DESIGNED FOR BOTH CONTINUOUS AND INTERMITTENT WORKING,
HOWEVER TO AVOID CONDENSATION PROBLEMS IN THE OIL, THE MACHINE MUST OPERATE
CONTINUOUSLY IN LOAD FOR AT LEAST 10% OF THE TIME, CHECK FOR SIGNS OF
CONDENSATION IN THE OIL BY FOLLOWING THE INSTRUCTIONS GIVEN IN CHAPTER 15.2