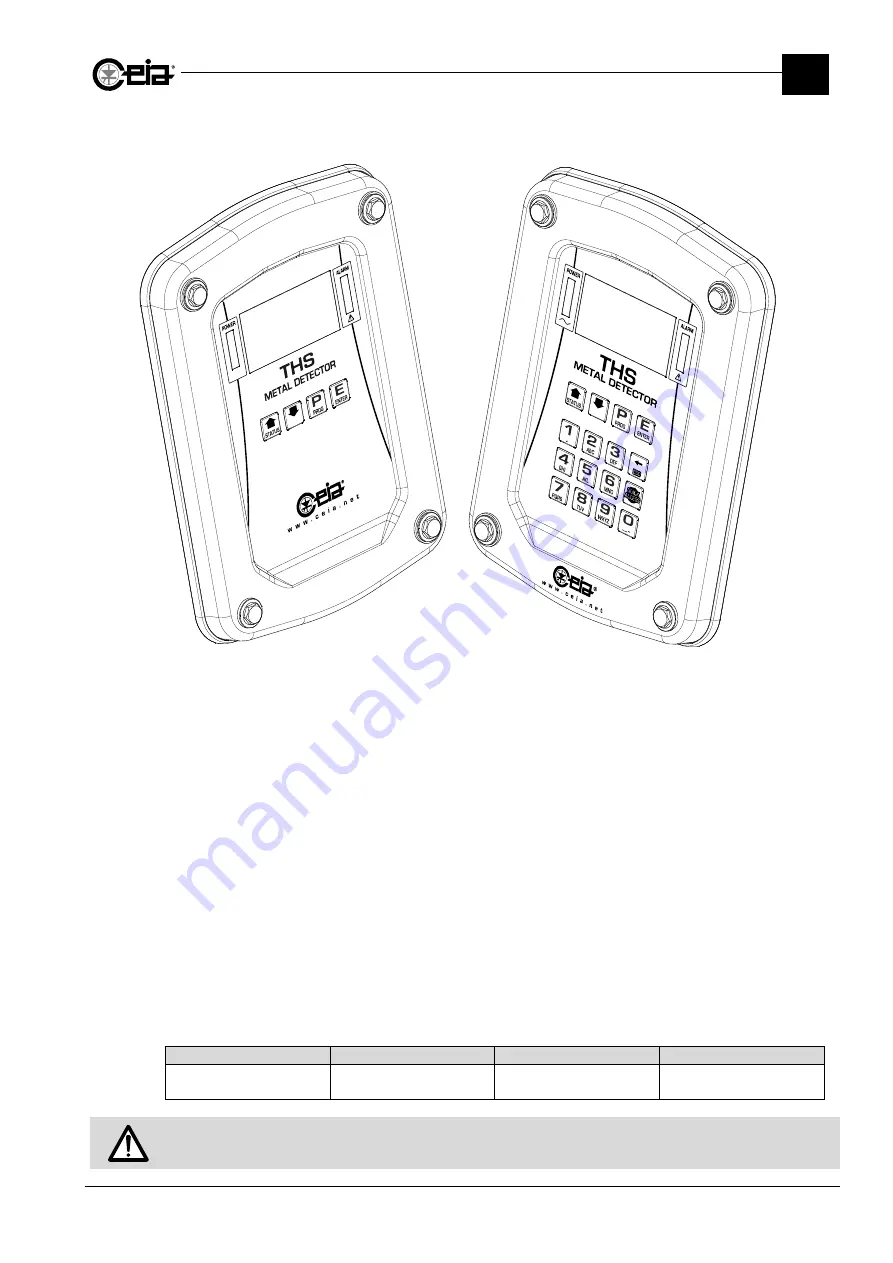
FI002K0018v1530hUK – THS/21 Instruction manual for installation, use and maintenance
UK
ORIGINAL
INSTRUCTION
1
Industrial Metal Detectors
and Integrated Systems with Conveyor Belt
THS/21E - THS/21
Instruction manual
for installation, use
and maintenance
Document
Date
Hardware
Software
FI002K0018v1530hUK 29/07/2020
HV5.xx
THSV5744
ALMV5430 / ALMV5730
Read this manual carefully before installing, operating or carrying out maintenance on the device. Keep the manual in a
safe place for future reference and in perfect condition. This manual must accompany the device described herein in the
case of change of ownership and until the device is decommissioned.