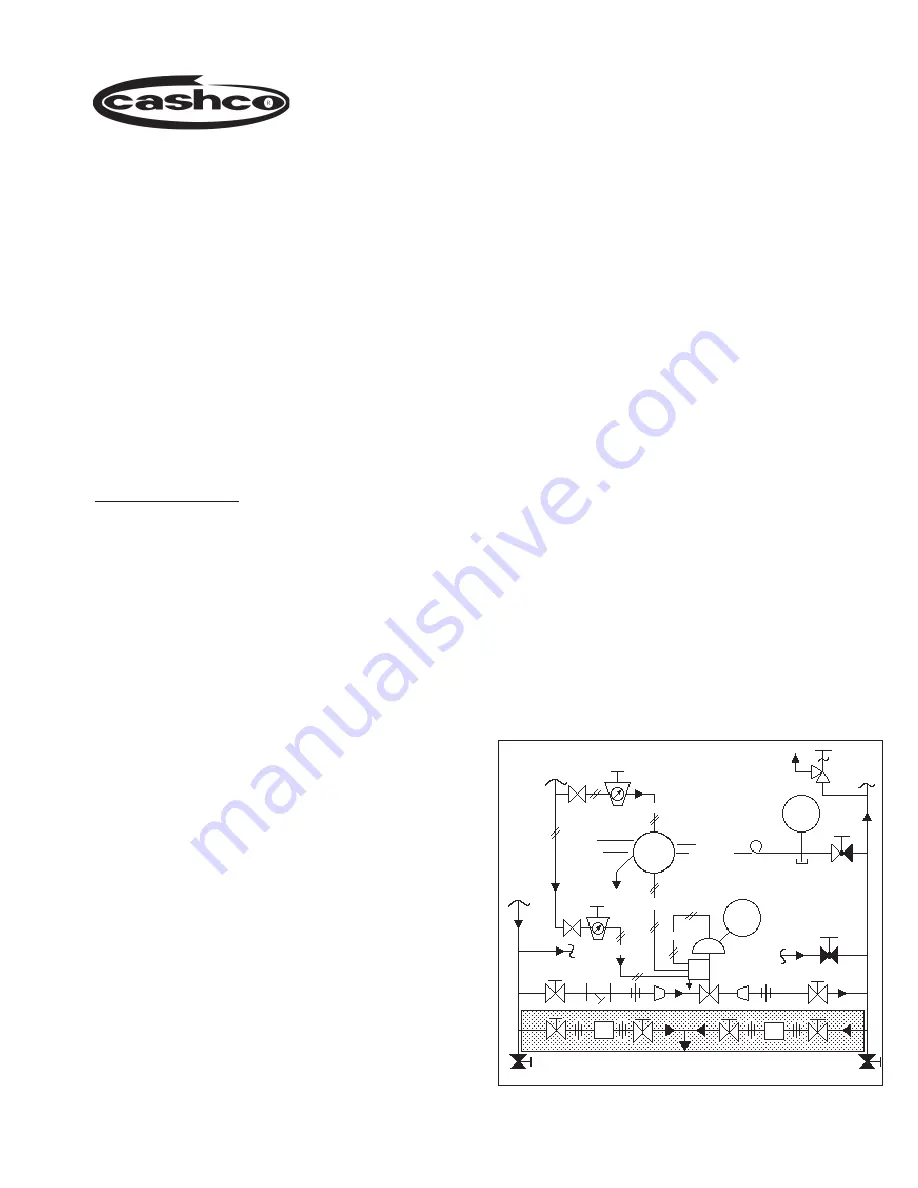
Outlet
@ P2
Port “B”
IAS @
60-100
psig
MODEL
764P
Port “A”
EXH
REV
SIG
“Output”
LOAD
P/P
Blowdown - Drain
Blowdown - Drain
(Shaded portion for steam/condensate systems)
PC
PI
PCV
Bypass
II. INSTALLATION
1. A block valve of the globe/needle type should
be installed at the location of the pressure
tapping. Ball, butterfly or gate valves are not
rec om mend ed.
2. Recommended sensing tap pipe size is 1/2"
(DN15).
3. Location of pressure sensing tap should be
in a zone not subject to flow disturbances.
Rec om mend a min i mum of 10 pipe diameters
upstream and 10 pipe diameters down stream
from any elbow, tee, valve, etc. that disturbs flow.
4. A pressure gauge is recommended at the location
of each tapping. Differential pressure designs
may in cor po rate a differential pressure gauge.
5. A pigtail siphon is required for hot condensing
fluids, such as steam, to assure a liquid trap at
the controller. The siphon should be installed
as near to the pressure connection(s) on the
controller’s diaphragm hous ing as practical.
Figure 1:
Recommended Piping Schematic for Pres sure
Reducing Control Valve with Positioner
I. DESCRIPTION AND SCOPE
The Model 764P is a pressure controller used for sensing static pressure, and outputting a pneumatic signal
pro por tion al to the deviation from the setpoint.
The Model 764PD is a differential pressure controller used for sensing two static pressures (“HIGH” and “LOW”),
and outputting a pneumatic signal proportional to the deviation from the setpoint.
With proper materials selection, the units are suitable for gaseous, liquid or steam service. Refer to Tech ni cal Bulletin
764P-TB for design con di tions and selection rec om men da tions.
Use of oxygen gas as the IAS for a 764P or 764PD is outside the scope of this IOM, and is considered “special
construction”.
Abbreviations Utilized:
CCW – Counter Clockwise
P1 –
Inlet Pressure
P/P – Pneu mat ic-to-Pneu mat ic
CW – Clockwise
P2 –
Outlet Pressure
REV – Rev o lu tion or Re verse
DIR – Direct
PB –
Proportional Band
SIG – Sig nal
EXH – Exhaust
PC – Pressure Controller
SRV – Safe ty Relief Valve
IAS – Instrument Air Supply
PCV – Pres sure Control Valve
TR –
Con den sate Trap
PI
–
Pres
sure Indicator
V –
Vent
SECTION I
MODEL 764P & 764PD
PNEUMATIC PRESSURE CONTROLLERS
INSTALLATION, OPERATION & MAINTENANCE MANUAL (IOM)
IOM-764P / PD
02-20
TR
Supply
Supply @
P1
DIR
TR
Supply
Airset
SRV
PROCESS
Pigtail
Siphon
V
SECTION II
ISO Registered Company