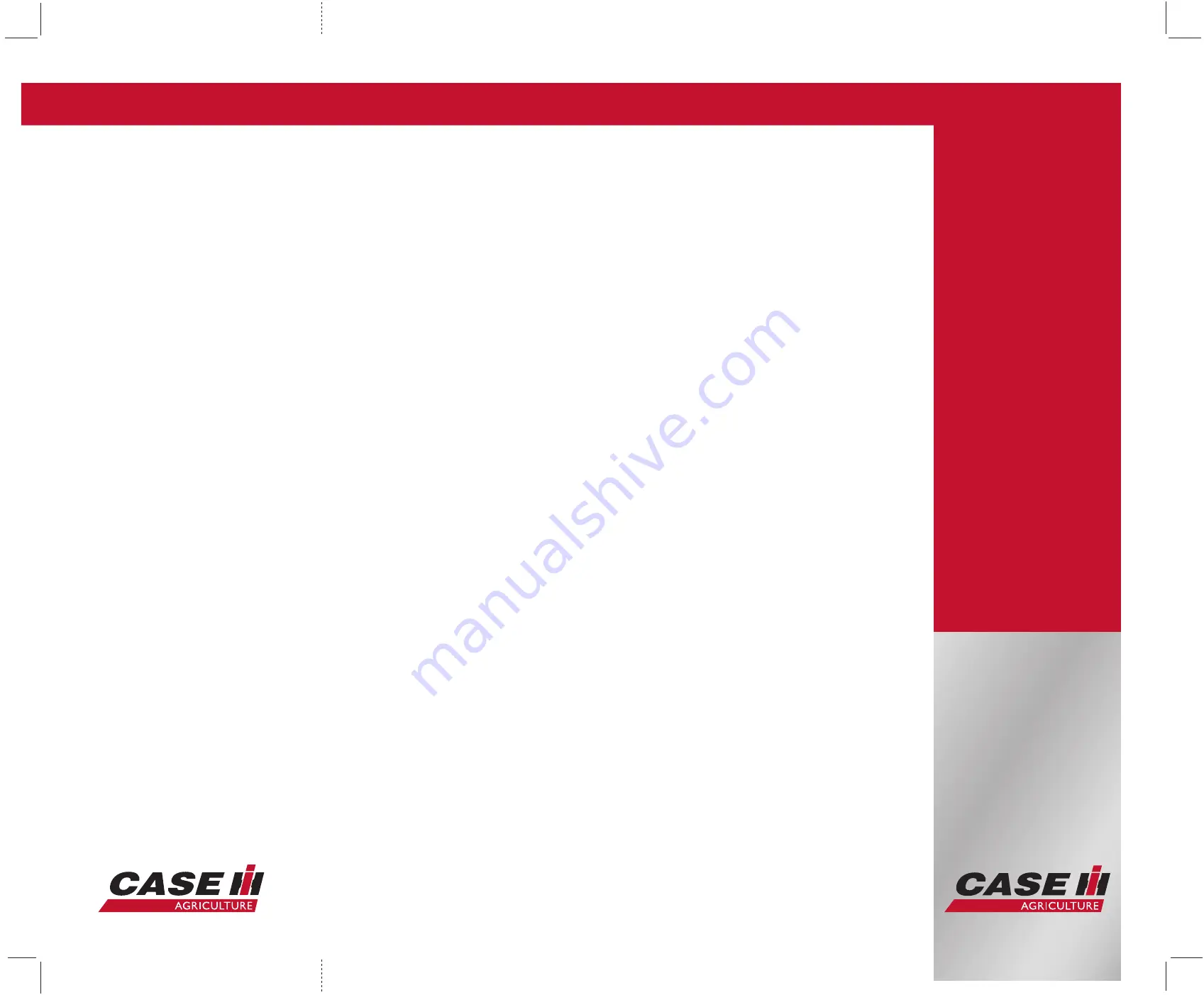
Part number 84568025
SER
VICE MANU
AL
1/3
Farmall 95U
Farmall 105U
Farmall 115U
Efficient Power
Tractor
SERVICE MANUAL
Farmall 95U Efficient Power
Farmall 105U Efficient Power
Farmall 115U Efficient Power
Tractor
Part number 84568025
English
March 2013
Copyright © 2013 CNH Europe Holding S.A. All Rights Reserved.
Summary of Contents for Farmall 105U Efficient Power
Page 7: ...84568025 22 03 2013 Find manuals at https best manuals com ...
Page 8: ...INTRODUCTION 84568025 22 03 2013 1 Find manuals at https best manuals com ...
Page 20: ...SERVICE MANUAL Engine Farmall 105U EP Farmall 115U EP Farmall 95U EP 84568025 22 03 2013 10 ...
Page 43: ...84568025 22 03 2013 10 1 10 001 22 ...
Page 61: ...This as a preview PDF file from best manuals com Download full PDF manual at best manuals com ...