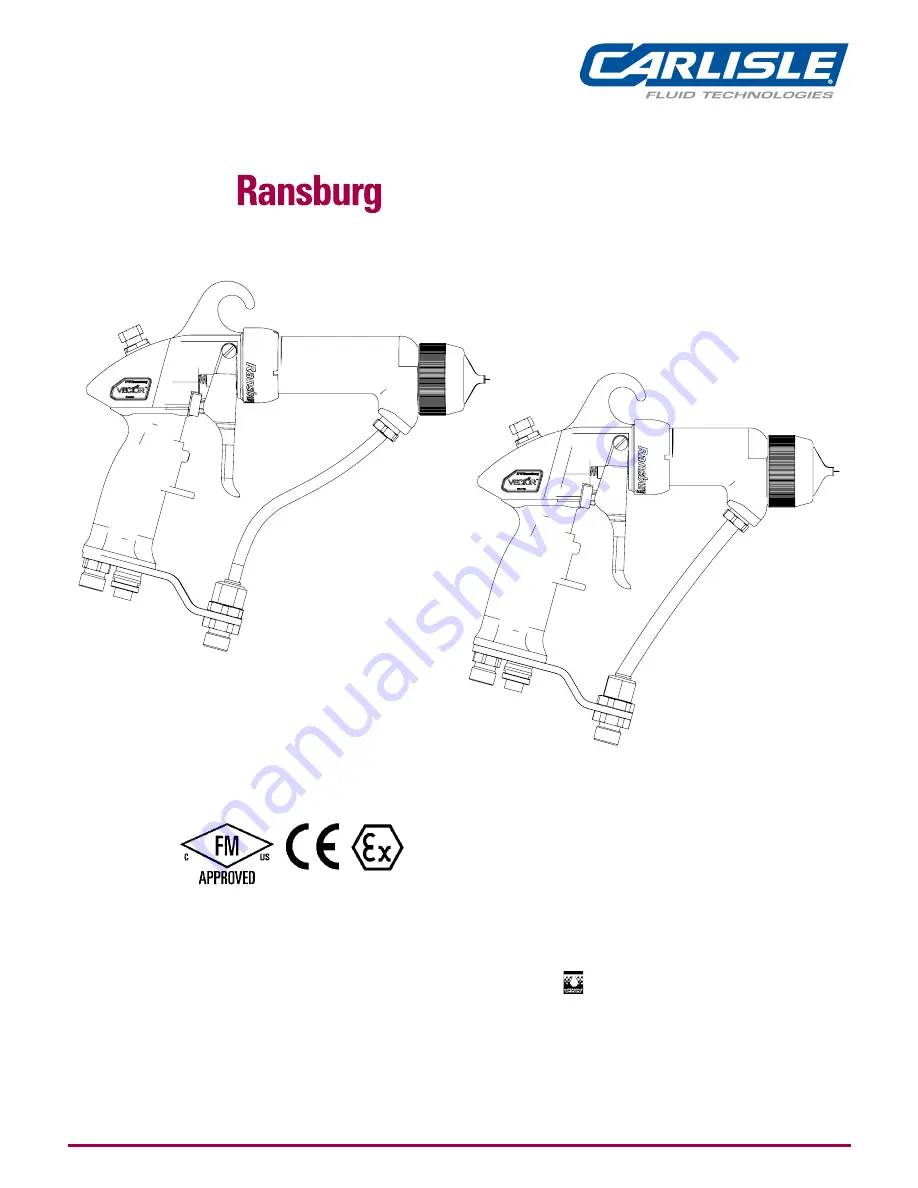
IMPORTANT:
Before using this equipment, carefully read SAFETY PRECAUTIONS and all
instructions in this manual. Keep this Service Manual for future reference.
Vector
TM
R Series
Cascade Applicators
Model:
79500 R90 Cascade - Solventborne
79501 R70 Cascade - Solventborne
79523 R90 Cascade - Waterborne
For Use With 80131-xxx Control Unit
AH-06-01-R17 (08/2019)
1 / 79
www.carlisleft.com
EN
SERVICE MANUAL