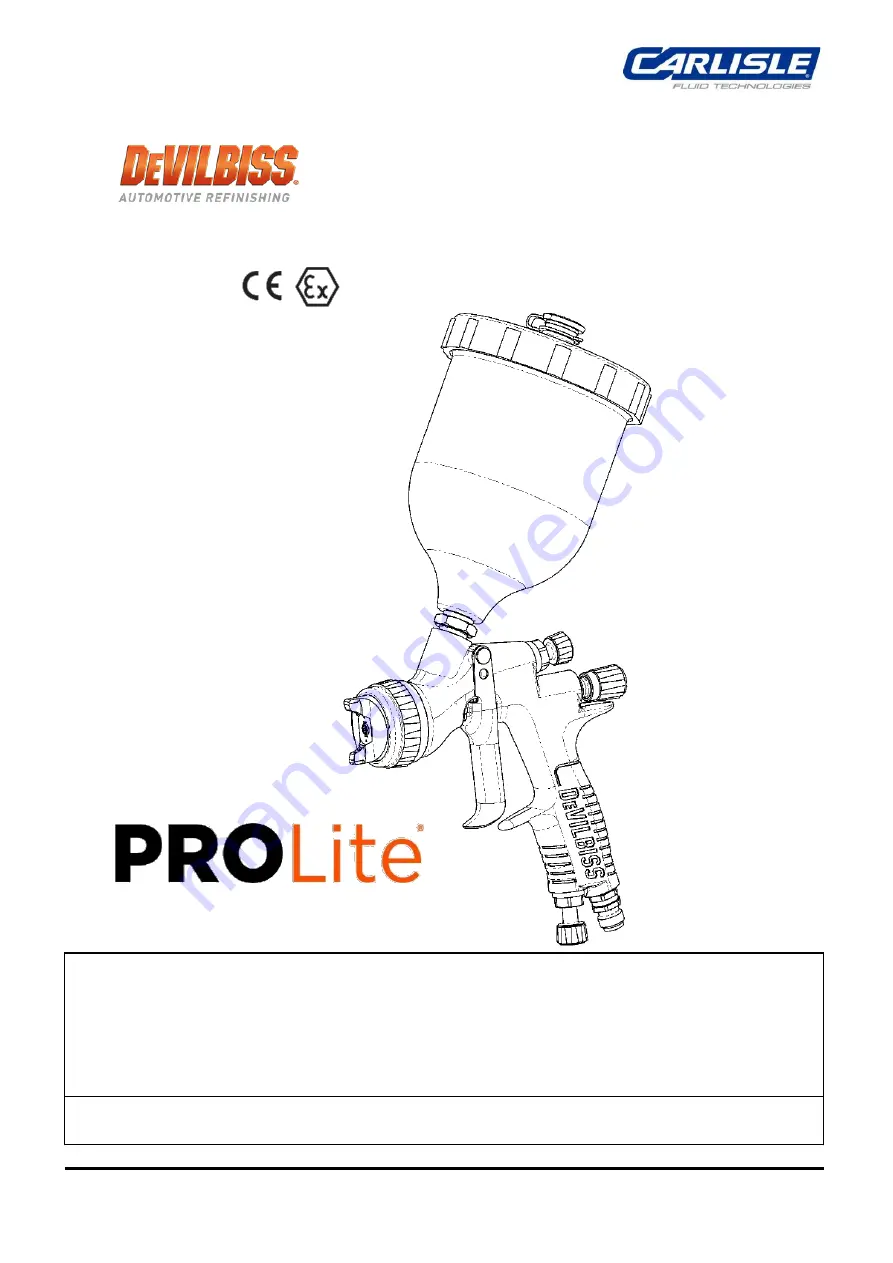
EN
IMPORTANT! DO NOT DESTROY
READ ALL INSTRUCTIONS BEFORE OPERATING THIS PRODUCT.
SERVICE MANUAL
It is the Customer's responsibility to have all operators and service personnel read and understand
this manual.
Contact your local Carlisle Fluid Technologies representative for additional copies of this manual.
II 2 G X/Ex h II Gb X
PROLite HVLP or High Efficiency -
Gravity Spray Gun
SB-E-2-996 R1.0
www.carlisleft.com
Summary of Contents for DeVILBISS 905038
Page 5: ...EN EXPLODED VIEW SB E 2 996 R1 0 5 24 www carlisleft com ...
Page 12: ...EN DISASSEMBLY PACKING DISASSEMBLY AIR VALVE SB E 2 996 R1 0 12 24 www carlisleft com ...
Page 13: ...EN ASSEMBLY AIR VALVE SEALS SB E 2 996 R1 0 13 24 www carlisleft com ...
Page 14: ...EN SPREADER VALVE REPLACEMENT SB E 2 996 R1 0 14 24 www carlisleft com ...
Page 21: ...EN DIMENSIONS SB E 2 996 R1 0 21 24 www carlisleft com ...
Page 22: ...EN NOTES SB E 2 996 R1 0 22 24 www carlisleft com ...
Page 23: ...EN NOTES SB E 2 996 R1 0 23 24 www carlisleft com ...