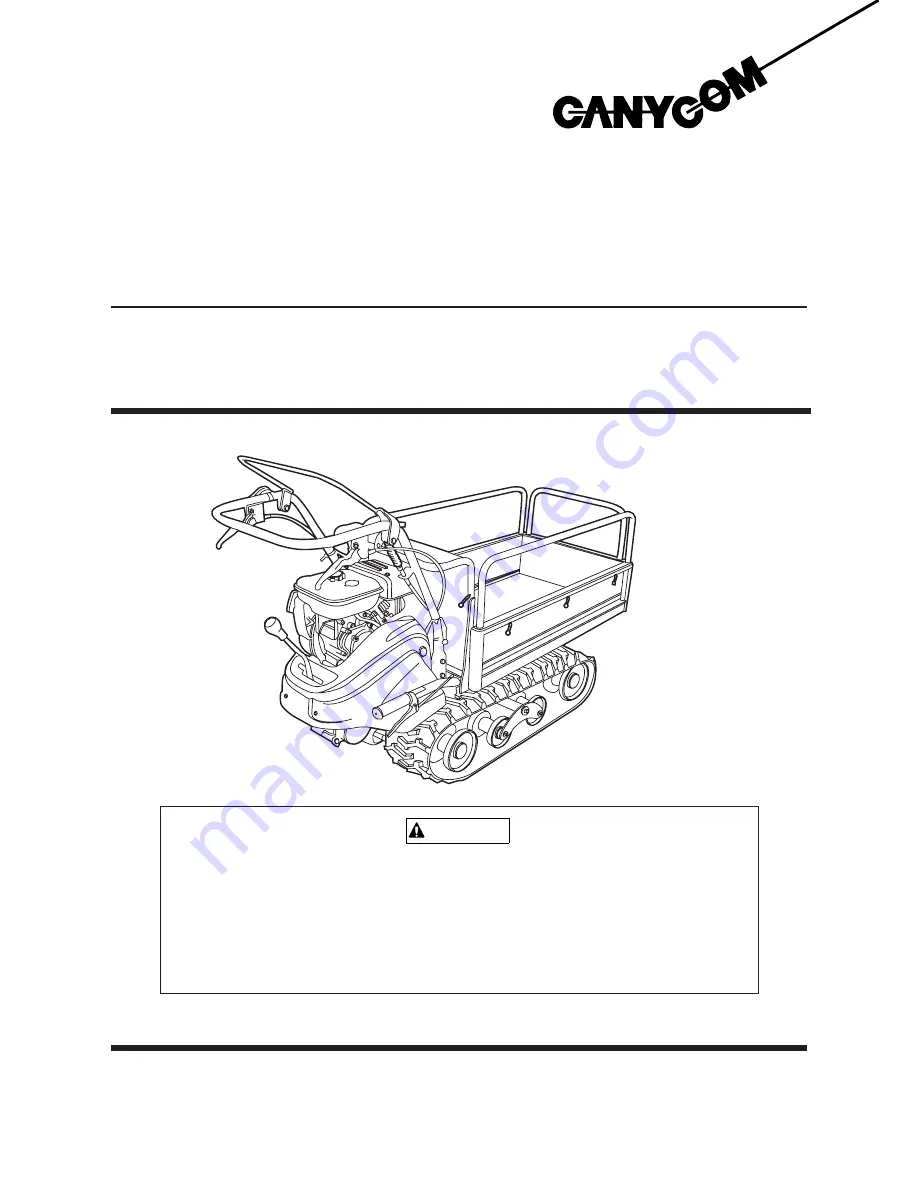
OPERATOR'S MANUAL
July 2003, 3558 7002 000
Read this manual completely before operating or maintaining this machine.
Failure to follow safety precautions could result in serious injury or death.
Keep this manual for future reference for you and for all those who operate and
maintain this machine.
WARNING
CHIKUSUI CANYCOM, INC.
90-1 Fukumasu, Yoshiimachi,
Ukihagun,Fukuoka,Japan839-1396
Tel.(09437)5-2195 Fax.(09437)5-4396
Off-Road Rubber Track Carrier
BP416/BP416D
BP415/BP415D