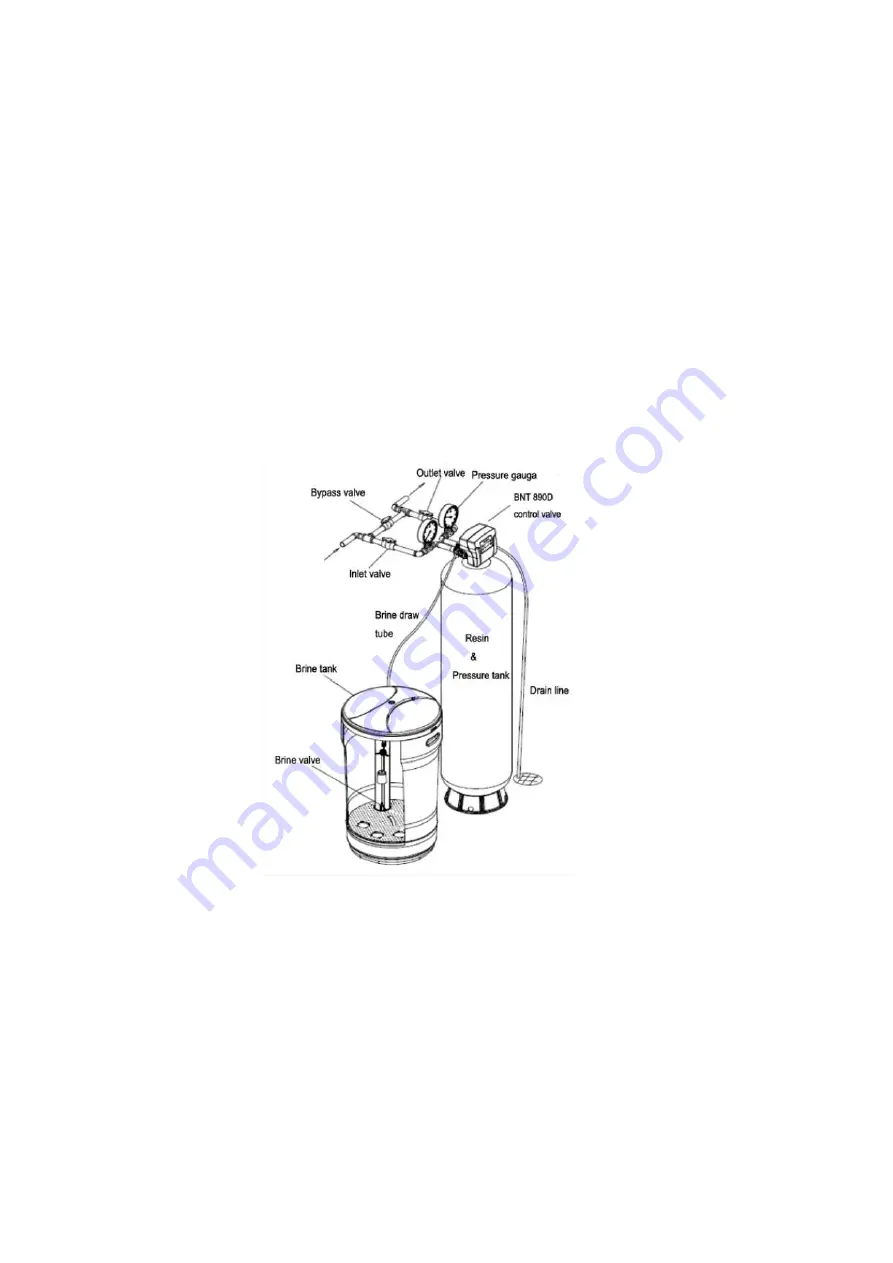
89 TLC
Tannins
Reduction System
O
w
n
e
rs
M
a
n
u
a
l
REVISION #
0
REVISION DATE May 4,2015
54616
1. Read all instructions carefully before operation.
2. Avoid pinched o-rings during installation by applying (provided with install kit) NSF certified
lubricant to all seals.
3. This system is not intended for treating water that is microbiologically unsafe or of unknown
quality without adequate disinfection before or after the system.
Canadian Head Office
655 Park St.
Regina, SK S4N 5N1
U.S. Head Office
8437 10th Avenue North
Golden Valley, MN 55427
IMPORTANT—PLEASE REFER TO THE PICTURE BELOW ON INLET/OUTLET SIDE OF THE
VALVE
Summary of Contents for Tannins 89 TLC
Page 7: ...7 Installation...
Page 20: ...20...