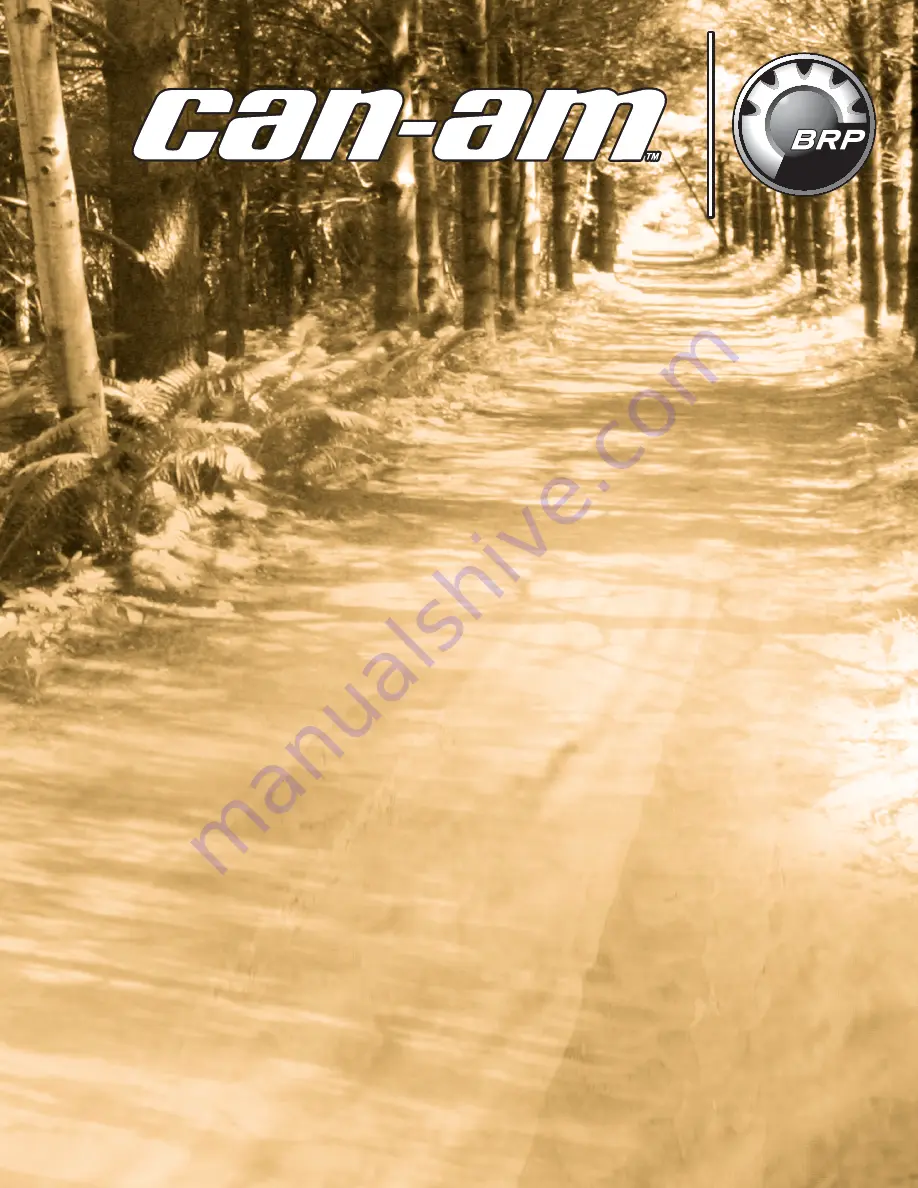
® AND THE BRP LOGO ARE TRADEMARKS OF BOMBARDIER RECREATIONAL PRODUCTS INC. OR ITS AFFILIATES.
©2009 BOMBARDIER RECREATIONAL PRODUCTS INC. ALL RIGHTS RESERVED. PRINTED IN CANADA.
219 100 388
CA
DPS/ACS TECHNICAL MANUAL / ENGLISH
MANUEL TECHNIQUE DPS/ACS / ANGLAIS
FAIT AU / MADE IN CANADA
U/M:P.C.
Technical Manual
2 1 9 1 0 0 3 8 8
DPS
TM
/ACS
DPS
TM
/ACS
2010
Summary of Contents for 2010 ACS
Page 1: ...Technical Manual 2 1 9 1 0 0 3 8 8 DPSTM ACS DPSTM ACS 2010 ...
Page 2: ...2010 DPS ACS Technical Manual ...
Page 7: ...IV vmr2010 002 ...
Page 9: ...2 ...
Page 56: ...NOTES ...
Page 57: ...NOTES ...