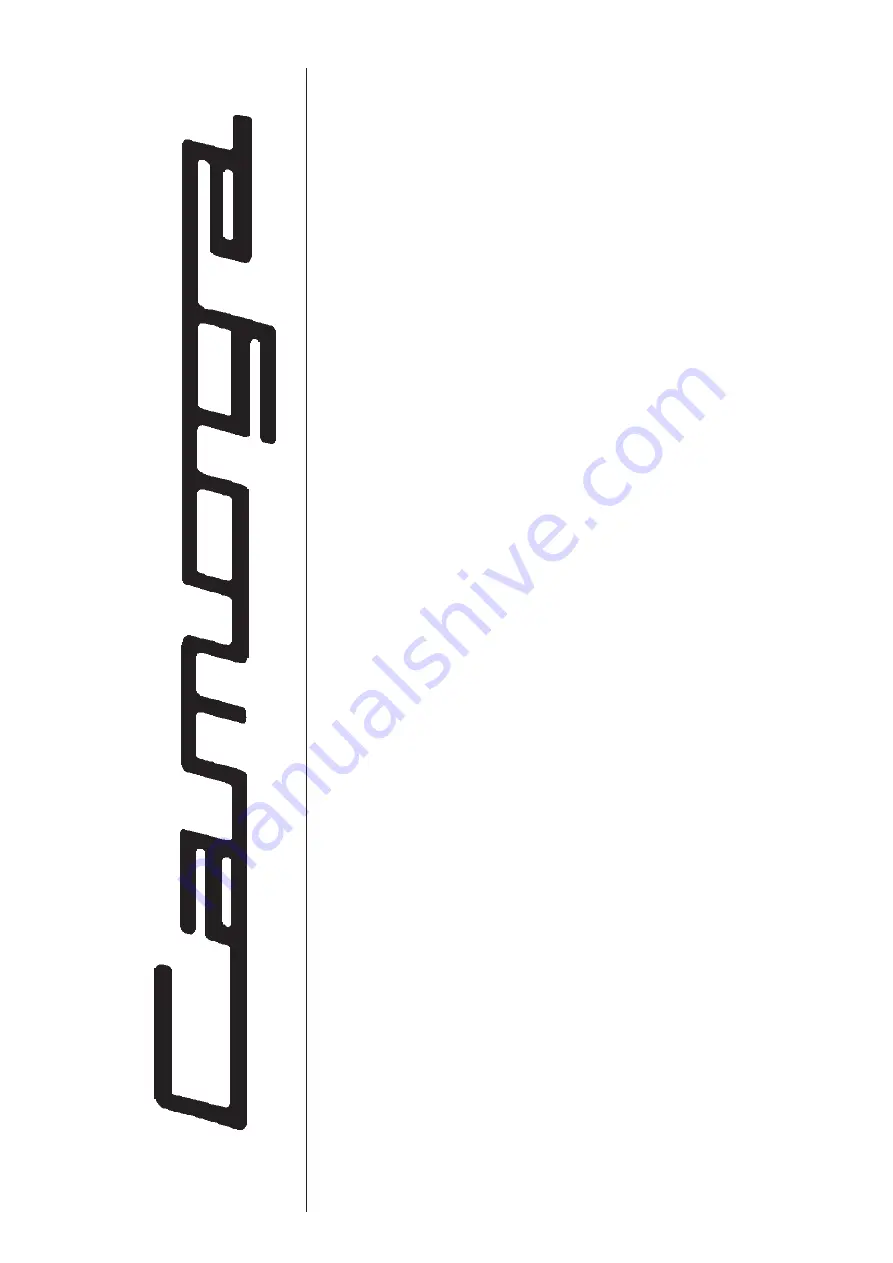
D U P
L
I C
A
T
E
Leather
Splitting
Machine
Model C 420
Instruction Manual
Serial No. .......................
20161 Milano Via Oroboni, 27
Tel. 026454000 Fax 026454007
site www.camoga.com e-mail [email protected]
S.p.A.
D U P
L
I C
A
T
E
Leather
Splitting
Machine
Model C 420
Instruction Manual
Serial No. .......................
20161 Milano Via Oroboni, 27
Tel. 026454000 Fax 026454007
site www.camoga.com e-mail [email protected]
S.p.A.