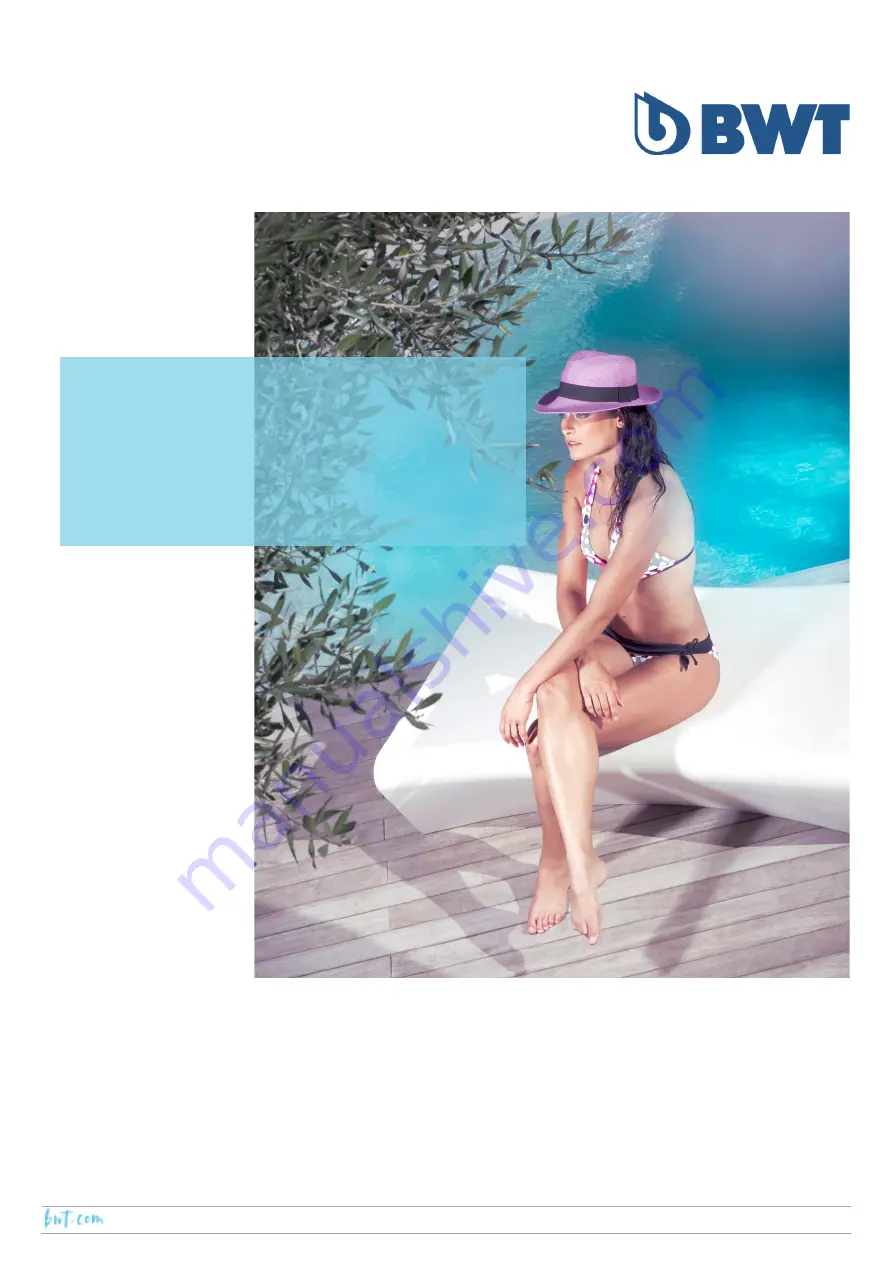
PROTECTION & SAFETY
1
2020/11 - Version: B - Code : 34561
INSTALLATION AND MAINTENANCE INSTRUCTIONS
To be read carefully and kept for future reference
You have just acquired an automatic pool cover, thank-you for placing your trust in us. Before
commencing installation and operation of the cover, please read the following document carefully, it
contains important recommendations concerning the various manipulations and advice for use. Keep
this manual and show it to any other users.
COVERDECK AX-IN
Submerged automatic
covers