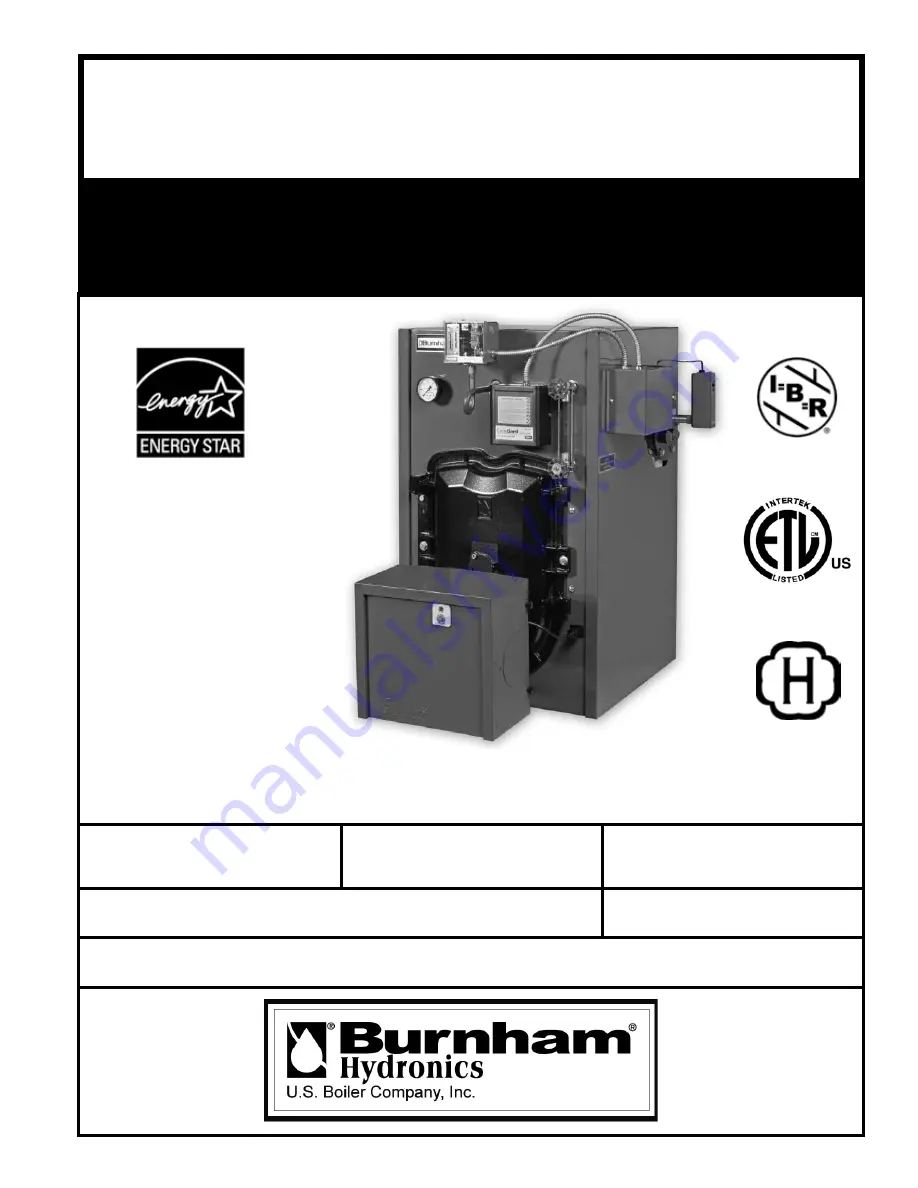
100618-01R5-4/09
As an
ENERGY STAR
®
Partner,
Burnham Hydronics
has determined that the
MST288, MST396, MST513 and
MST629 meet the
ENERGY STAR
®
guidelines for Energy
efficiency established by the
United States Environmental
Protection Agency (EPA).
Price - $3.00
D
N
A
G
N
I
T
A
R
E
P
O
,
N
O
I
T
A
L
L
A
T
S
N
I
R
O
F
S
N
O
I
T
C
U
R
T
S
N
I
E
C
I
V
R
E
S
™
m
a
e
t
S
a
g
e
M
R
E
L
I
O
B
L
I
O
S
S
A
P
-
3
g
n
i
k
e
e
s
n
e
h
W
.
r
e
il
p
p
u
s
li
o
r
o
r
o
t
c
a
r
t
n
o
c
g
n
it
a
e
h
r
u
o
y
ll
a
c
,r
e
li
o
b
o
t
s
r
i
a
p
e
r
r
o
e
c
i
v
r
e
s
r
o
F
g
n
it
a
R
n
o
n
w
o
h
s
s
a
r
e
b
m
u
N
l
a
i
r
e
S
d
n
a
r
e
b
m
u
N
l
e
d
o
M
r
e
li
o
B
e
d
i
v
o
r
p
,
r
e
li
o
b
n
o
n
o
it
a
m
r
o
f
n
i
.
r
e
li
o
b
e
h
t
f
o
p
o
t
n
o
d
e
t
a
c
o
l
l
e
b
a
L
r
e
b
m
u
N
l
e
d
o
M
r
e
li
o
B
r
e
b
m
u
N
l
a
i
r
e
S
r
e
li
o
B
e
t
a
D
n
o
it
a
ll
a
t
s
n
I
T
S
M
r
o
t
c
a
r
t
n
o
C
g
n
it
a
e
H
r
e
b
m
u
N
e
n
o
h
P
s
s
e
r
d
d
A
Summary of Contents for MST288
Page 11: ...11 Figure 4 Boiler Removal from Skid ...
Page 19: ...19 Figure 9 Float Type LWCO and Pressure Limit Installation ...
Page 25: ...25 Figure 12 Recommended Boiler Piping for Gravity Return Steam Boiler ...
Page 34: ...34 Figure 18 Wiring Diagram Steam Hydrolevel CG450 Probe LWCO ...
Page 35: ...35 Figure 18A Wiring Diagram Riello 40 Series Burner Steam Hydrolevel CG450 Probe LWCO ...
Page 36: ...36 Figure 19 Wiring Diagram Steam McDonnell Miller PS 801 Probe LWCO ...
Page 37: ...37 Figure 19A Wiring Diagram Riello 40 Series Burner Steam McDonnell Miller PS 801 Probe LWCO ...
Page 38: ...38 Figure 20 Wiring Diagram Steam McDonnell Miller 67 Float LWCO ...
Page 39: ...39 Figure 20A Wiring Diagram Riello 40 Series Burner Steam McDonnell Miller 67 Float LWCO ...
Page 45: ...45 Figure 24 L1 and V1 Head Electrode Positioning and Gun Setting Beckett AFG ...
Page 58: ...58 Bare Boiler Assembly ...
Page 60: ...60 Jacket Assembly ...
Page 62: ...62 MST288 Thru MST629 Steam Boilers Trim and Controls ...
Page 64: ...64 Beckett AFG Burner ...