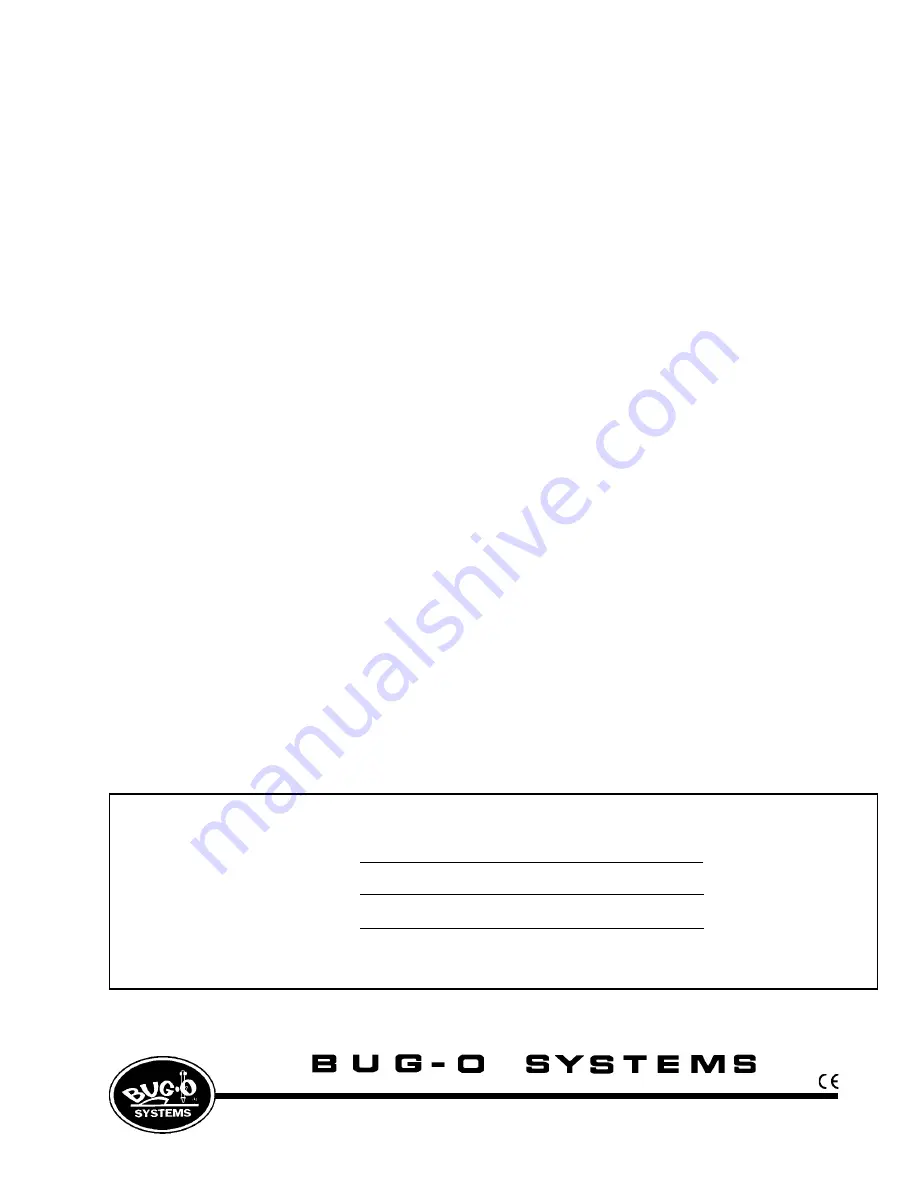
INSTRUCTIONS
aNd
PaRTS MaNUaL
aLL TIME GIRTH WELdER
BGW-1000 BGW-2000
a dIVISION OF WELd TOOLING CORPORaTION
280 TECHNOLOGY
dRIVE CaNONSBURG, PENNSYLVaNIa 15317-9564 USa
PHONE: 1-412-331-1776 http://www.bugo.com FaX: 1- 412-331- 0383
Please record your equipment identification information below for future reference. This information can be found
on your machine nameplate.
Model Number
Serial Number
Date of Purchase
Whenever you request replacement parts or information on this equipment, always supply the information you have
recorded above.
LIT-BGW-IPM-1209