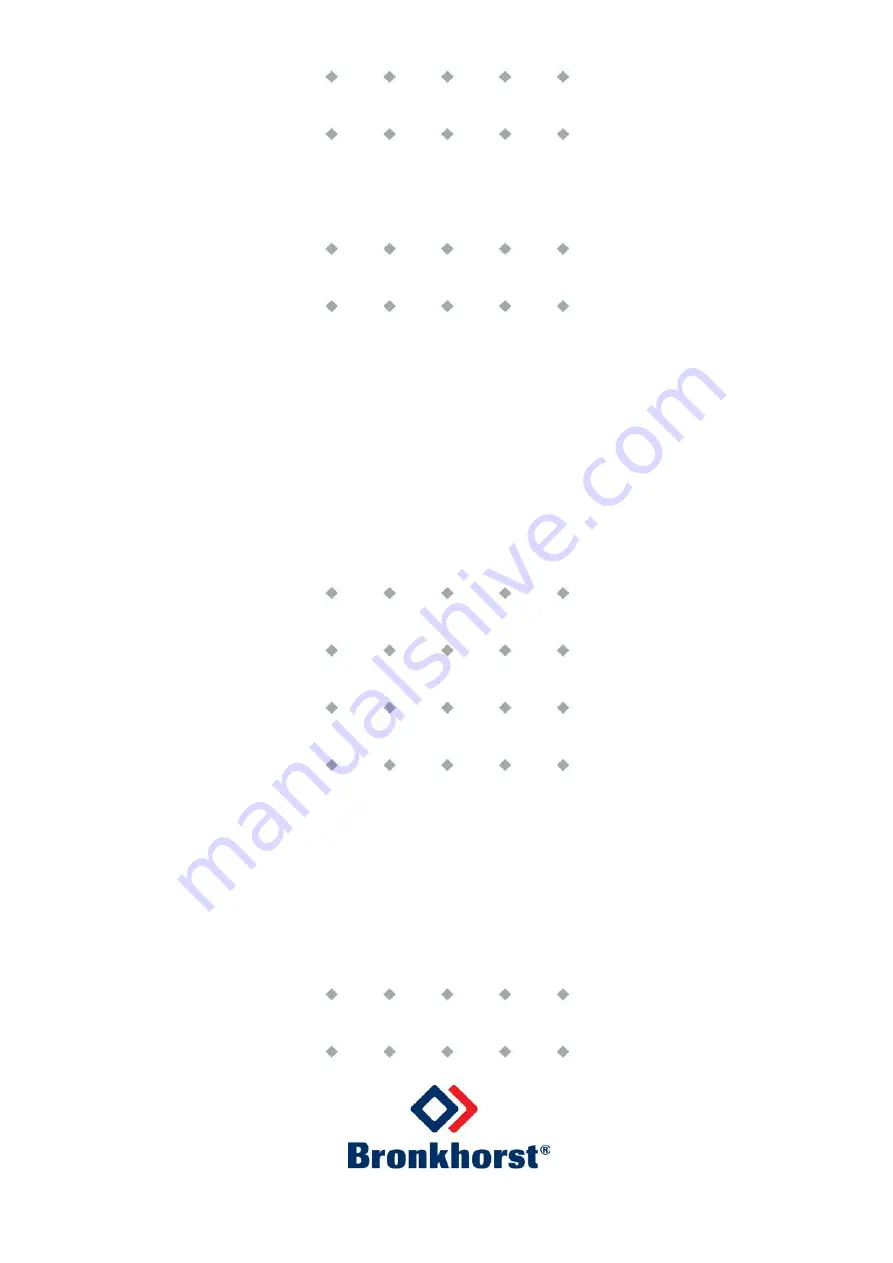
Doc. no.: 9.17.084 rev. N Date: 23-09-2020
ATTENTION
Please read this document carefully before installing and operating the product.
Not following the guidelines could result in personal injury and/or damage to the equipment.
EL-FLOW® Prestige series
Thermal Mass Flow Meters/Controllers
Instruction Manual