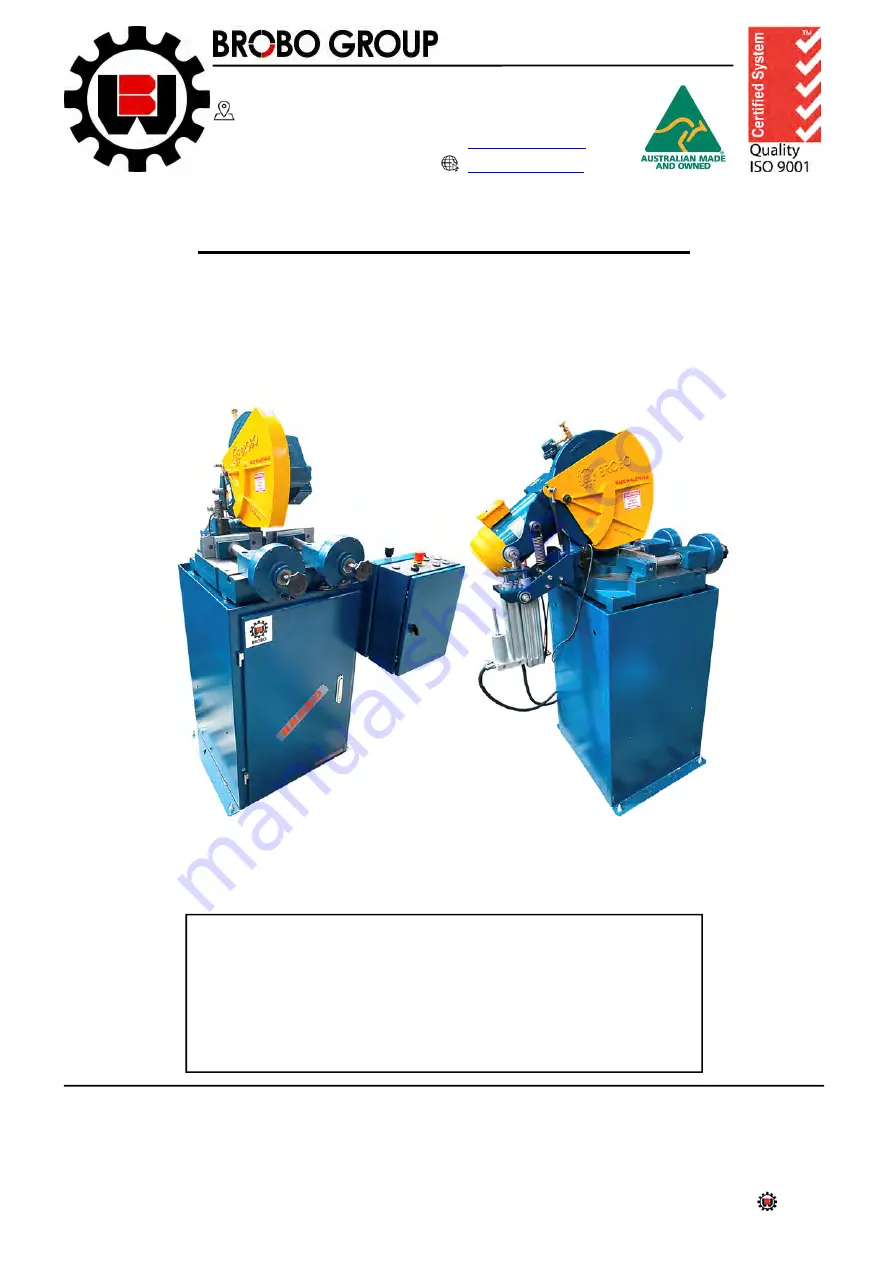
Brobo Group
brobo.com.au
©
BROBO GROUP (AUST) PTY. LTD.
8 Fowler Rd, Dandenong South
Victoria 3175, AUSTRALIA.
☏
+ 61 3 9794 8751
📧
🖷
+
61 3 9794 8792
www.brobo.com.au
PRODUCT & MAINTENANCE MANUAL
SEMI-AUTOMATIC HYDROCHECK SAW
MODEL No. SA350H, SA400H
Precision Drilling Machines
Tapping Machines
Multi-Head Drills
Tool Grinders
Tool Post Grinders
Machine Vices
Special Production Equipment
Accessories
Riveting Machines
Pedestal Grinders
Metal Cutting Saws
Linishers
YOUR BROBO DISTRIBUTOR IS:
A.C.N.
098 264 316
A.B.N.
42 098 264 316