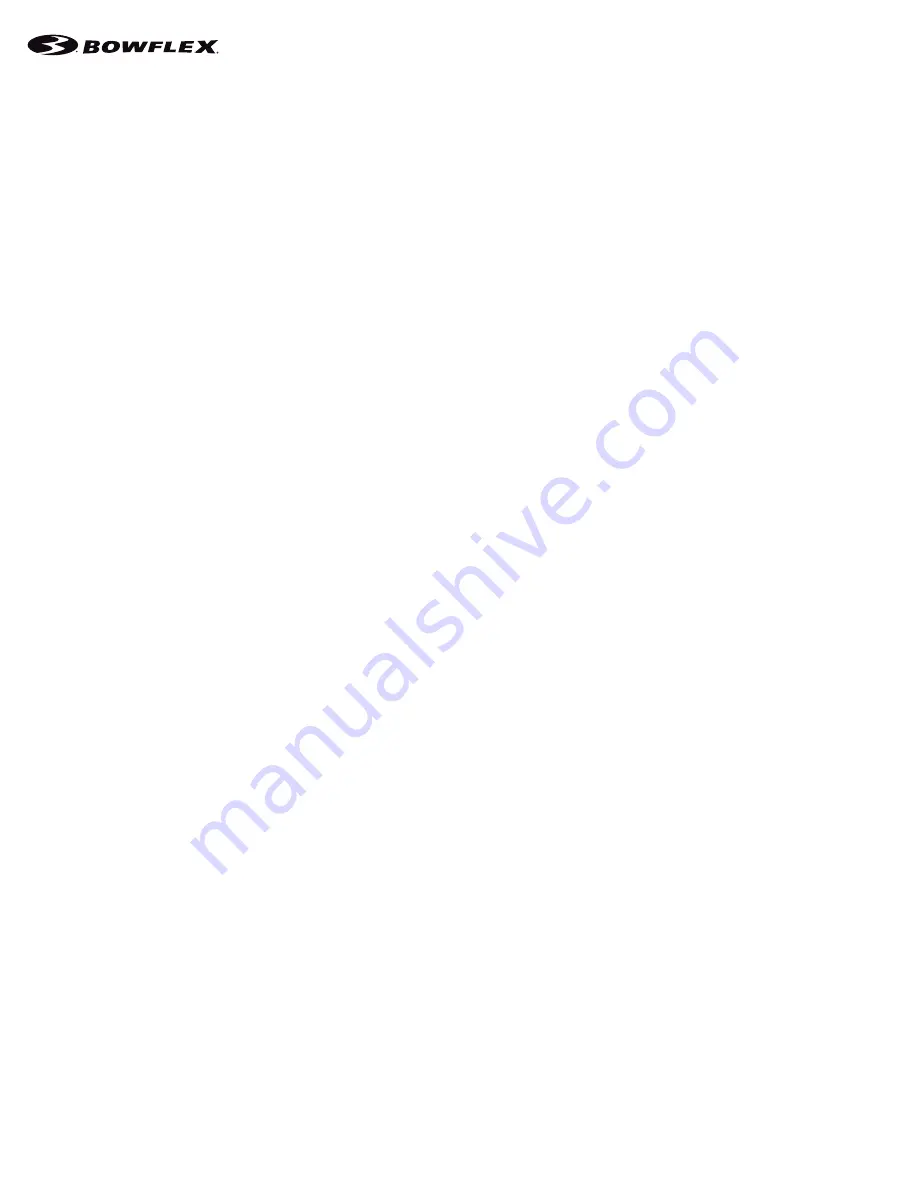
1
8014572.081518.D
8010214.081518.G
Service Manual
Table of Contents
Nautilus, Inc., (800) 605-3369, www.NautilusInc.com - Customer Service: North America (800) 605-3369, [email protected] | outside U.S. www.nautilusinternational.com | Printed in China | © 2015 Nautilus, Inc. |
® indicates trademarks registered in the United States. These marks may be registered in other nations or otherwise protected by common law. Bowflex, the B logo, and Bowflex Max Trainer are trademarks owned
by or licensed to Nautilus, Inc.
Bowflex Max Trainer
®
M7
Service Manual
Section
Code
Section
Page
Number
1
Important Safety Instructions
2
1
Safety Warning Labels and Serial Number
3
1
Specifications
4
1
Moving / Leveling the Machine
5
1
Connectivity
6
1
Maintenance
7
1
Maintenance Parts Exploded View
8
1
Troubleshooting
-
Sections
10
1
No Power / Display Will Not Turn On
11
1
Buttons Do Not Respond
12
1
Needle will Not Move / Machine Goes to Sleep While in Use
13
1
Resistance Does Not Respond
14
1
Machine
Seized
Up
15
1
Console Does Not Light Up Completely
16
1
Machine Slips During Use
17
1
Rollers
and
Pedals
18
1
Noises
-
Main
19
1
Noises - Metallic Grinding or Scraping
20
1
Noises - Rubbing / Belt
21
1
Noises - Clicking, Clunking or Knocking
22
1
Noises - Squeaking, Squealing or Chirping
23
1
Telemetric Heart Rate Issues
24
1
Contact Heart Rate Issues
25
1
Upper
(Drive)
Pulley
26
1
Console
Setup
Mode
27
1
Console
Board
Detail
28
1
Replacement Procedure Skill Level
29
Mechanical / Modification Procedures
2
Roller Wheel Maintenance Procedure
30
3
Adjust
the
Brake
Assembly
33
4
Adjust the Leg Assembly Alignment
38
5
Reset
the
Console
41
6
Set
the
Date
and
Time
43
Part Replacement
7
Replace
the
Brake
Assembly
44
8
Replace
the
Console
Assembly
49
9
Replace the Console Handlebar Assembly
53
10
Replace
the
Crank
Arm
57
11
Replace
the
Drive
Belt
61
12
Replace
the
Drive
Pulley
66
13
Replace the Hardware of the Drive Pulley
73
14
Replace
the
Fan
Assembly
79
15
Replace
the
Fan
Pulley
82
16
Replace
the
Frame
Assembly
90
17
Replace the Handlebar Pivot Assembly
99
18
Replace the Input/Output (I/O) Cable
101
19
Replace
the
Power
Inlet
105
20
Replace the Roller Wheel Assembly
108
21
Replace Self-Tensioning Fan Belt
110
22
Replace the Servo Motor
118
23
Replace
the
Shrouds
123
24
Replace the Speed Sensor
128
25
Replace
the
Tensioner
131
26
Replace the Wireless Heart Rate Module
136